Flexco Defeats Dust in Local Quarry Operation
ELLAINA GRIXTI, National Marketing Executive for Flexco Australia provides details of a Case Study on containing dust in a quarry.
Transporting dry concrete involves high levels of dust, because of this, it can be one of the most difficult aggregates to manoeuvre – especially when conveyed as fine particles. Eliminating dust is a priority for most sites as it can cause and contribute heavily to a variety of respiratory and cardiovascular health issues as well as being a skin and eye irritant. As a result, it is an important goal for most sites to contain as much dust as possible. This is especially important due to the strict environmental policy companies must adhere to around Australia.
To eliminate dust usually requires some sort of enclosed skirting system at the transfer point. When dust hits the belt from a transfer chute, it tends to have a ‘rebound’ effect, causing large levels of dust to rebound off of the belt and into the atmosphere, contributing heavily to the afore mentioned health risks. A system that encloses this dust at the load zone is the only effective way to eliminate such hazards.
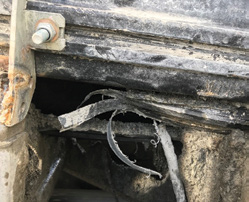
At the time of plant construction, this particular site installed a complex skirting system, which made maintenance and replacement of belt conveyor products extremely difficult. The design of the current system required unnecessary components to be removed in order to access and replace parts – meaning a mammoth loss in productivity for this site. In addition to the design complexity, the spare parts for the system were difficult to source, as the manufacturer was based in Europe, resulting in long lead times.
Apart from maintenance issues, the previous system was also insufficient in protecting the belt conveyor system against serious safety and productivity issues such as spillage. The spillage on the current system was immense, making it difficult to conduct maintenance tasks safely. The severe levels of spillage also resulted in a loss of profit due to wasted and unsellable aggregate material. In addition to these issues, the spillage caused a material build up on one side of the conveyor belt, causing the belt to mistrack – damaging the soft skirt and also the conveyor structure.
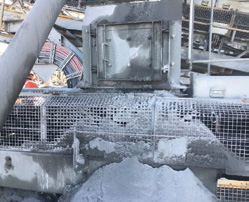
Flexco’s distributor, Fenner Dunlop installed Flexco’s enclosed skirting system with great ease due to the simple, yet effective design of the product. Dean Callaway, Sales Manager for Fenner Dunlop Wollongong, oversaw the project and states that it took only two, twelve hour shifts to complete the installation of the thirteen metre enclosed skirting system.
In addition to ease of installation, the simplicity of the design meant production time no longer had to be compromised to complete maintenance tasks such as soft skirt change out and adjustments. The system also incorporates easily adjustable hard skirts for longer wearing side panels.
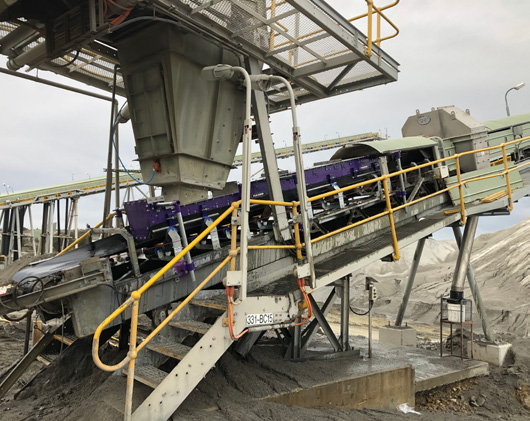
Adding to the ease of the product itself, is the extra assistance Flexco provides “Flexco engineers came to site to measure and provide support, as not all systems were standard – they required engineered modifications”, Callaway comments.
Fenner Dunlop installed the first two systems in November 2018 and since then an additional three systems have been installed. A true testament to the ease, rigour and efficiency of Flexco’s enclosed skirting system which is able to prevent spillage and contain dust, making it safer for maintenance crews to conduct work both on and around the belt conveyor systems. Callaway comments on the effectiveness of the system: “Flexco’s enclosed skirting system has significantly reduced spillage making it safer and easier for maintenance crews”.
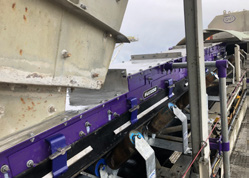
For more details on enclosed skirting systems please contact
[email protected]
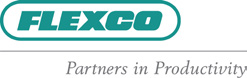
You must be logged in to post a comment Login