Flomax Wire Harp-Screens
Mobile Plants
DAVID HASTIE, Director for Advanced Engineering Group reports on the product Flomax Wire Harp Screens.
SCREENING fines and other difficult materials via your Mobile Screening Plant can be best achieved by using Harp screens (also known as Piano Wire Screens).
This screen media is still the most efficient & productive worldwide and when it comes to damp and sticky materials, it solves more problems than not.
Generally Harp Screens will screen 80% more than the rate of equivalent aperture in woven wire mesh, meaning more tons per hour of production.
With Harp Screens you get very little material build-up as there are no cross wires, therefore no corners for fines to start building up from, plus the diameter of the wire is normally smaller than wire mesh, so giving less surface area for fines to take hold.
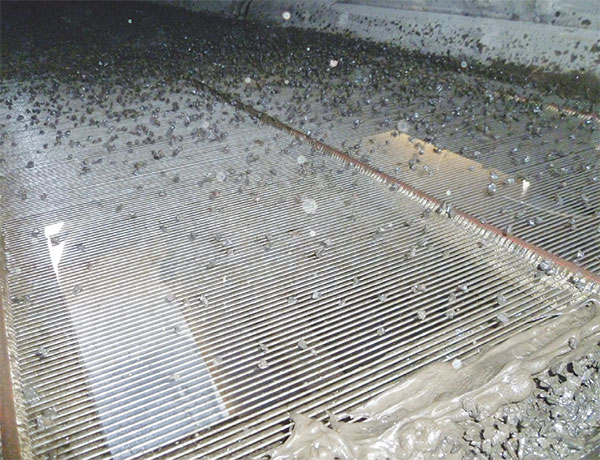
If you’re currently using Woven Wire Mesh to screen those difficult materials then you’re possibly also facing some blinding and pegging of your screens.
If you’re working with sticky and damp aggregate then consider using a Harp Screen for getting a more efficient result. Harp Screens, unlike Woven Mesh is made up of individually tensioned wires that are straight and run hook to hook.
These wires move independently of each other during the screening process and cut through the material creating higher production rates and offers maximum percentage of open area.
There are times when you wouldn’t use a harp screen i.e. you have large material coming down directly on the harp. You need to remove the oversize product or have protection from the upper deck as they aren’t designed for impact.
Also, depending on what material you are screening and what your product sizing requirements are you can get long flat pieces which could cause oversize in the finished product. Discuss your requirements with your local AEG sales representative.
To ensure the longest life from the screen the Harp must be fitted correctly i.e. the tension bar must be all the way into the back of the hook prior to tensioning and the profiles must be fitted onto the stringers correctly.
After some 4-6 hours use from installation recheck the screen tension and adjust as necessary. Most screen tension adjustments are made with-in the first two weeks of use.
Wire screens, by virtue of its construction and use, will ‘stretch’ and therefore lose its initial tension. The tension on these screens should be checked on an on-going basis.
The hooks are designed for durability but also for easy
installation. The plastic profiles are also designed to fit with ease and come in round profile to fit over round top capping rubber or square to fit direct over your stringer rail.
The wire we use when making our Flomax Harp screens is of a higher carbon content than regular woven mesh (approx. 30%) so offers longest wear-life possible.
Flomax Harp-Screens are the highest production screen on the market. AEG supply Harp/Piano wire screencloths to suit all types of mobile screening plants. We can supply almost any specification of Harp screen with-in the following limits.
- The overall dimensions can be any combination up to 3300mm inside hooks (length) and 1830mm wide.
- The apertures we supply are from 1.0mm up to 16mm. Almost any aperture is achievable.
- Wire sizes are 0.7mm up to 2.50mm in either carbon steel or Stainless Steel.
- We are able to vary the hooks to suit all tension bar setups in the market.
Ex-Stock:
No one else in Australia or New Zealand keeps an inventory of re-made Harp Screens like AEG does. We can give same day service for Harps to fit most Mobile Screening Plants, including: Powerscreen, Finlay, Precision Screen, McCloskey, Metso (Nordberg), Fintec, Extec, Keestrack and many more.
HOOKS
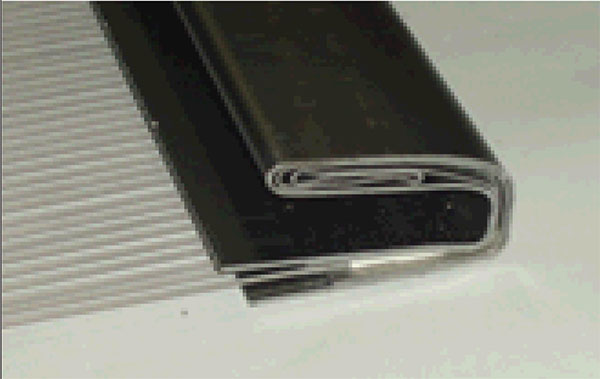
SUPPORT PROFILE TYPES
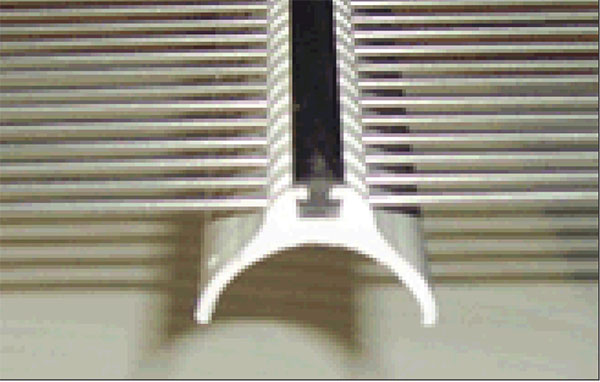
(For round top capping rubber)
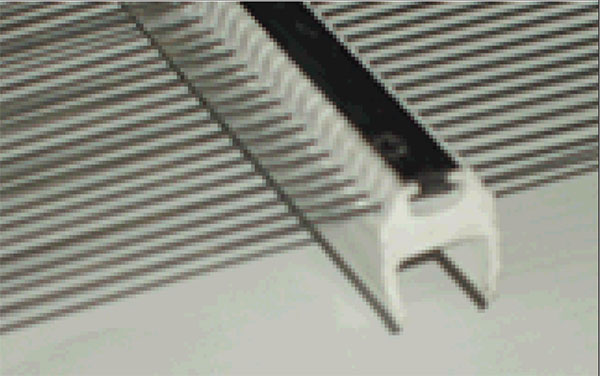
(Sits direct over your stringer rail)
“The AEG harp wire screens installed at Northern Quarries (basalt source) have yielded increased production output compared with traditional stainless steel woven wire screens.
The screens have prevented blinding and build up on our fine aggregate screens, which was an issue causing downtime and contamination requiring regular manual labour to clean the screens.”
“AEG has been a member of the CMPA since 2010 and see great value and importance in networking with fellow members to improve the performance of their products.”
For further information contact:
ARTHUR SUMMIT
Advanced Engineering Group
Phone: 03 9363 1577 or 0413 395 567
Email: [email protected]
You must be logged in to post a comment Login