Kinder invest in light weight Materials Handling Equipment & Avoid Heavy Duty Personal Injury Claims.
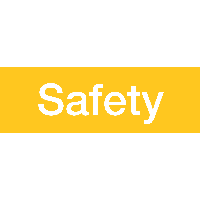
CHRISTINE KINDER, Marketing Manager for Kinder Australia reports on the need to improve workplace and worker OHS standards.
The indirect costs associated with lower back pain has been reported by an Australian workplace health and OH&S expert* to be costing the Australian Economy $60.15 billion each year (4.8 per cent of GDP) due to loss of earnings and productivity, with small and medium employers said to be paying the highest in rehabilitation costs.
The need to improve workplace and worker OHS standards should be a priority for all operations, regardless of size, as the benefits are the same. Not only will it help prevent Management from being on the receiving end of any legal personal injury prosecutions, but being OHS compliant reduces the accumulation of daily inefficiencies that can prevent achieving overall productivity gains.
“Regretfully one of the key reasons for the slow uptake of some of these OHS friendly equipment solutions is that Management overlooks the cost of OHS compliance. Instead they can be too driven by daily production targets at the expense of injuries to their human resources. What isn’t being considered is that short-term back pain can lead to more enduring and serious physically debilitating conditions. The situation then needs further financial investment to cover the salary costs of replacement contract workers” Neil Kinder comments.
Kinder Australia offers a range of lightweight bulk materials handling componentry – engineered utilising composite polymer technology as a modern substitute to the much heavier steel or rubber constructed equivalents.
A recent customer case study from a Pilbara-based crushing plant, demonstrates how OHS hazards are reduced by switching to using polymer-based composites such as the wear liner system – K-Superline®. The plant has benefitted in the following 2 simple but very effective ways:
- Reduced the material build up occurring: the B93 durometer type specified for the 1″ thick K-Superline® Polyurethane Lining has a low-friction surface so it immediately eliminated the problem of build up and congestion through to the screen.
- Reduced OHS hazards (noise and physical injury):
unlike any metal lining, polyurethane absorbs all of the impact so it immediately reduced the noise levels of the material being handled. The repetitive jack-hammering also very physical for the resources deployed to keep crushing production going. Also, as the polyurethane is much lighter than steel, it was less much less awkward to carry and manoeuvre when installing. This is especially helpful in confined spaces such as chutes.
Avoid small temporary injuries and reduce the risk of your workers developing more serious incapacitating skeletal conditions by switching to these polymer equivalents. K-Superline is available in various durometer formulas to suit the specific impact and sliding abrasion criteria of different applications.
*As published in the Konect Market Report Volume 2
For more marketing information, contact Christine Kinder, Kinder Australia on 03 8587 9111 or [email protected]
You must be logged in to post a comment Login