Quarry Decreases Maintenance Time, Increases Productivity with Flexco Solution
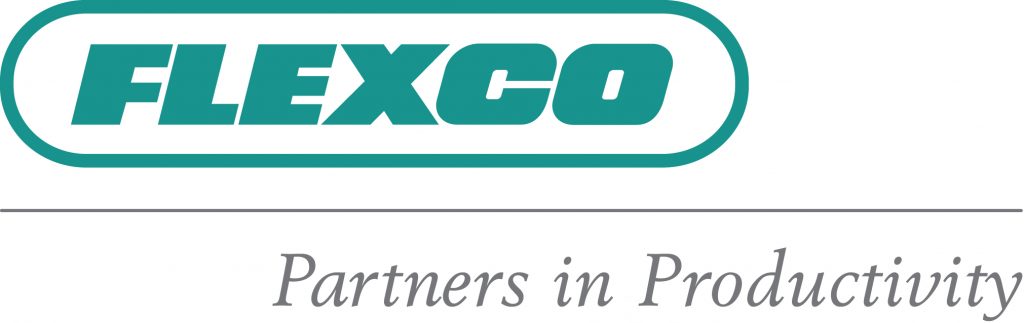
Quarrying has long been a part of South Australia’s history. The Mount Lofty Ranges have been quarried since 1837. For over 180 years the East-Coast of South Australia has been providing the nation with rich aggregate materials to build and support the growing need for infrastructure in Australia.
The demands for aggregate materials have changed vastly over the past 180 years, differing largely from the small quarries which supplied stone to build houses for colonial settlers. The quarries, which now provide building materials for a much larger and ever-growing population, introduce a higher demand for output tonnages. This demand drives the need to increase efficiency and productivity on sites throughout the region.
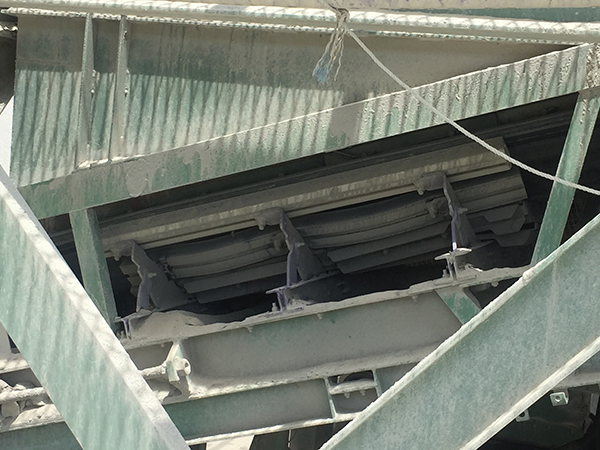
LOAD ZONE DAMAGE HALTS PRODUCTION
A large quarry in South Australia had difficulty equipping their belt conveyor system with the products necessary to handle such tonnages. The quarry was experiencing severe belt wear and spillage around the load zone, with damage to the structure from the impact energy of the large rock being conveyed. The conveyor presenting the most difficult challenge was a critical conveyor, which feeds the secondary crusher, so achieving optimum efficiency was a matter of great importance for the site’s operational managers.
The average rock size that fell onto this conveyor was around 500mm x 500mm, falling from a height of four metres onto a 19mm thick and 1200mm wide belt running at 3m/sec. This particular belt saw 1500 tonnes of quarry rock per day. With 1500 tonnes of material hitting the same spot every single day from a height of 4 metres without the necessary support, it’s no wonder the belt and structure became severely damaged.
The impact bed that was originally installed was not strong enough to support the extreme tonnages the load point saw day in and day out. As a result, the idler frames would break every few weeks and the belt quickly became severely damaged – to the point of needing replacement. The idler frames would also have to be replaced every 4 to 6 weeks, with shutdowns occurring at the same rate, to replace the frames and repair or replace the belt. The belt itself was even replaced and upgraded multiple times to try and combat this issue.
This constant cycle of maintenance and repair amounted to a total of 24 hours of downtime per month. Not only did the shutdowns occur to replace broken belt conveyor system components, but also to clean up the mass amount of spillage that was occurring – from the overflow of material which could not be contained by the impact bed.
SAVING THE LOAD ZONE WITH RUGGED IMPACT BEDS
Operation managers turned to Flexco specialists to source or create a solution to these problems, which were affecting both productivity and also profitability of the quarry. Traditionally, Flexco DRX Impact Beds are available in four different sizes, dependent on impact energy (200, 750, 1500 and 3000). However, for this application, the impact energy was far
greater than the acceptable and safe standard of the largest, DRX 3000 bed, so a custom solution was made with extra support in the impact bars and absorbing mounts. The custom solution offered the same benefits of the rest of the DRX line of beds and was designed and manufactured in Australia.
DRX models feature velocity reduction technology, which ensure a level of protection like no other, resulting in less belt wear and damage, less rebounding and material degradation and two levels of impact-absorbing force reduction. The DRX bed also separates in the middle, allowing the two sides to slide apart, providing access to all the bars and bolts for quick, easy, and safe maintenance.
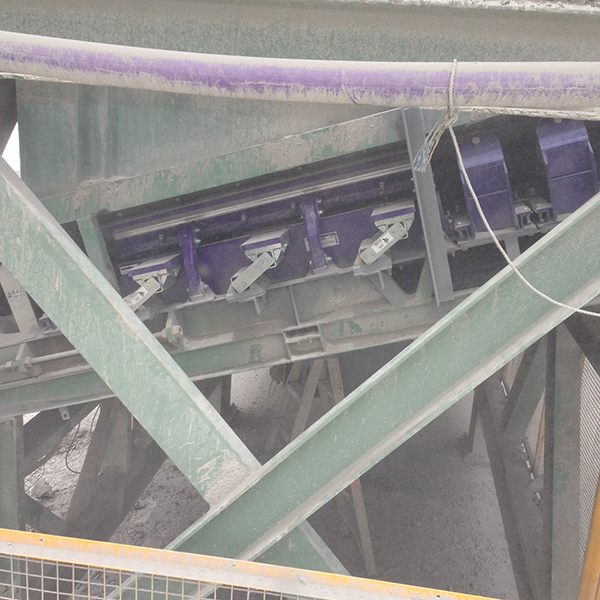
SUCCESS AT THE LOAD ZONE
After the custom DRX 4500 bed was installed, the site saw an outstanding amount of change. The biggest and most impressive difference in operation was that the belt could now run 24/7. Since the product was installed, the site has only performed planned maintenance and scheduled shutdowns. This results in not only higher output tonnages, but less need for maintenance, allowing maintenance crews to focus their time and knowledge on other areas of the site instead of reacting to the same issue repeatedly.
Due to the fact that the new impact bed is more than adequately supporting the tonnages seen by the belt – there is no need to replace the idler frames, impact bed support bars, or the belt. Not only does this save time for the quarry, but also a huge amount of money that can be allocated towards funding upgrades for other areas of the site.
Flexco are looking to expand their business into Victorian quarries and have been an active Associate Member of the CMPA since 2015.
To find out how you can replicate the success of this quarry, reach out to our technical support team at [email protected], or call 1300 098 435 for more information.
You must be logged in to post a comment Login