What to consider when buying your manganese steel wear parts for your crusher?
MICHAEL EWING, General Manager of Amsted Global Solutions Australia, Associate Member of the CMPA since 2002.
Plant maintenance is an important issue for the quarry manager, and it is critical that it is planned and not reactive. There are many decisions that must be made to ensure the most cost effective approach is made to obtain the best short and long term outcomes. The short term outcomes include the initial cost of replacement parts however, one must not exclude the effect of cheap substandard parts on the long term outcome. Crusher wear liner replacement is probably one of the most important areas and decisions that can have a significant influence on the cost per tonne produced. When decision time comes to buy replacement manganese steel wear liners for your crusher, it is important to look beyond the part number in the manual.
To ensure you will be getting the best liner profile option for your plant, and a quality product that will perform without premature failure or damage to your crusher, the quarry manager should consider the following points and ask the relevant questions.
- Where is the liner manufactured?
- Does the supplier and manufacturers have ISO Quality accreditation?
- Does the liner supplier have the expertise and facilities to support the end user?
- What liner material best suits your crushing plant?
- Does the liner manufacturer have the appropriate expertise?
- Are liner test certificates available?
- What should the end user look for in the test certificates?
- What should the end user look for when receiving new liners?
- What should the end user look for when examining worn liners?
Where is the liner manufactured?
In excess of 95 percent of cast manganese steel crusher wear liners are manufactured overseas and supplied to the Australian market through original equipment manufacturers outlets, third party suppliers and direct sales from the Foundry through their Australian subsidiary company. Amsted Global Solutions Pty Ltd with offices in Perth, Brisbane and
Melbourne is the subsidiary of the Amsted Industries Group, comprising foundries in South Africa, Mexico, Brazil, USA with the capacity to produce over 5,000 tonnes per month of cast manganese steel wear liners.
Does the supplier and manufactures have ISO Quality accreditation?
Repeatability and traceability are the key issues that relate to quality wear liner performance. It is expected of the manufacturer to produce a consistent product that will give the end user the confidence to make decisions based on consistent wear liner performance. Traceability is the responsibility of the supplier and manufacturer combined to provide for the end user to support the repeatability commitment.
Does the Liner Supplier have the Expertise and Support Facilities?
It is important the supplier knows their product and can offer the correct wear liner for each crusher and include advice that will assist the quarry manager with the decision for jaw liner profiles, cone liner wear face profiles, cone liner feed openings and liner material. The requirement for backup stock must also be considered should the quarry not be carrying spare liners. Amsted Global Solutions Pty Ltd has the expertise in WA, Vic and Qld, combined with the Amsted Industries Group, to provide technical service to individual crushing plants across Australia. This is further supported with a large stock of wear liners for the common liner requirements and individual consignment stock agreements.
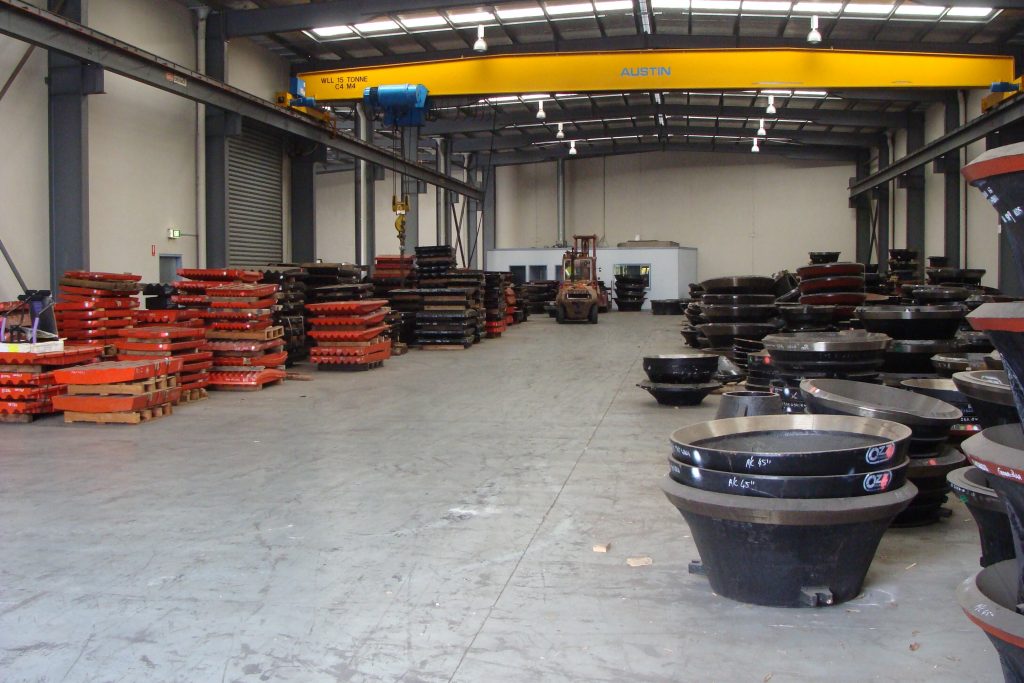
What Liner Material best suits your Crushing Plant?
Manganese steel was invented by Sir Robert Hadfield in 1882 and was unique in that it combined high toughness and ductility with exceptional work-hardening capacity. The material developed for crusher wear liners contained around 1% C carbon, 11% Mn manganese and the balance Fe iron. This material was cast followed by heat treatment after initial cooling.
The heat treatment process included heating to above 1,000 ⁰C, to convert the brittle as-cast multi phase microstructure to a single-phase austenite, followed by a rapid water quench. The single-phase austenitic microstructure remains stable at room temperature producing a ductile high strength material resistant to the fatigue subjected by the rock crushing process . The material can readily revert back to the brittle as-cast structure in weld areas or during other thermal processes and care should be taken to avoid this. The standard Hadfield austenitic manganese steel described in Australian Standard AS2074 Grade H1A remains the most reliable material for crusher wear liners. The material has a starting Brinell hardness of around 200 and the ability for the working surface to harden to above 500. With C above 1% and Mn above 11% It is considered the best material for the crushing of high compressive strength rock. Increasing the carbon and manganese level does change material properties that can improve the wear life when crushing lower compressive strength rock although the reduction in the liner fatigue resistance must be considered.
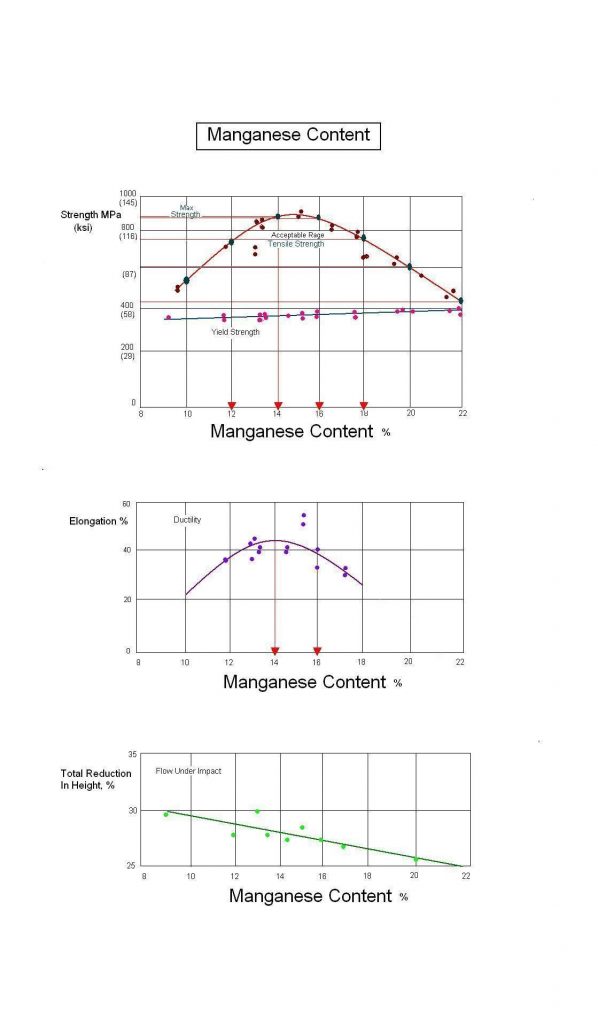
manganese steel with increased C and Mn)
Amsted Global Pty Ltd has developed three grades of manganese steels with assistance from original equipment manufacturers and ongoing feedback from end users operating in a variety of crushing applications. There is evidence a liner can have up to double the wear life changing from a standard manganese grade to a higher C-Mn grade when crushing a low compressive strength and high silica content material. At the same time using the high C-Mn grades for high compressive strength rock can lead to premature failure before the liner reaches its expected life.
The three primary grades include:
a. Grade 845: Standard Hadfield Manganese Steel: 13% Mn and 1.2% C
b. Grade 846: 18% High Carbon Manganese Steel: 18%Mn and 1.3% C
c. Grade 843: 23% XAlloy: 23%Mn and 1.35%C
All the above manganese steel grades are generally covered by the relevant specifications in standards AS2074 grade H1A, BS3100 Grade BW10, ASTM A128 Grade A and SABS 407 grade 1 containing carbon levels ranging from 1.0% – 1.35% and manganese from 11%. Carbon is the main element that
will determine the life of the wear liner. As the carbon level is increased a corresponding increase in manganese is made to accommodate carbon in a fully austenitic material that will retain sufficient fatigue strength for the application. The high C-Mn grades give the best results compared to standard manganese when crushing the the lower compressive strength and high silica content materials.
The quarry manager must do their homework before making a wear liner material change. Technicians at Amsted Global Solutions Pty Ltd with support from the Amsted Industries Group will provide the technical support required to assist with this decision.
Does the liner Manufacturer have the Appropriate Expertise ?
The manufacture of austenitic manganese steel is not just from a textbook. Expertise has been established by a number of producers that have been developing their procedures in conjunction with their end users over many years. Many new suppliers have failed trying to introduce manganese casting manufacture into their traditional foundry operation without understanding the risks to final produce quality. Amsted Global Pty Ltd have been producing manganese steel wear liners for over 50 years supplying original equipment manufacturers and end users around the world.
Are liner test certificates available?
A good test of a supplier’s commitment to their customers is the ability to provide test certificates. Crusher wear liners do not roll off an automatic assembly line and their manufacture to a consistent standard is important for the end user. The manufacture must have procedures, practices and checks in place for this to occur and be able to support their commitment with relevant documentation in the form of test certificates.
Amsted Global Solutions deals only with accredited suppliers of Manganese with the commitment to provide test reports on request and support their liner end users with a customer service report to assist with all issues raised.
What should the end user look for in the test certificates:
Test certificates may be supplied for:
a. Chemistry
b. Dimensional inspection
c. Heat treatment
Chemistry reports must include the main elements of carbon and manganese along with residual elements that can occur as deliberate additions or unintentional additions from melting recycled scrap or a carryover from previous melts in the foundry. It is important that the supplier can explain the effects of the residual elements present and the relationship between carbon and manganese levels.
Dimensional inspection is important at the manufacturing stage to ensure the liner will fit the crusher. If not supplied with the liner should be available if requested.
Heat treatment reports can be subjective, and the reporting of heat times and temperatures does not mean the material properties have been met. A simple check is the magnetic test. Austenitic manganese steel, only achieved with correct chemistry and heat treatment, is non-magnetic. This can be determined by holding a magnet to a surface of the liner where the surface oxidised layer has been removed by grinding 1 – 2mm . An attraction to the magnet will indicate unsatisfactory heat treatment and should be investigated. Should subsequent cracking or premature failure occur the cause can best be determined from a metallurgical examination.
What should the end user look for when receiving new liners?
New wear liners supplied for your crusher are usually supplied neatly painted and packed for good presentation. An initial visual inspection is usually all that is possible and provided there are no surface imperfections present the liner is stored for later use. There are a number of simple checks that can be made.
a. Cone liners are manufactured as a casting in two sections, the inner surface and the outer surface. For a bowl liner the inner surface is the crushing face, and the outer surface is the fitting face and for the mantle this is opposite. It is important that for each liner these surfaces are concentric and the best way to ensure this is for the manufacturer to machine both faces. This requires only a light skim on the large end wear face of each liner and for fine crushing is particularly relevant to obtain an accurate closed side setting at startup.
b. The supplier part number and foundry cast number (or heat number) should be cast or at least stamped on a non wearing surface of each liner and that number matches the delivery docket supplied with the liner. A supplier operating under a certified quality management system will have full traceability through all phases of manufacture through to liner disposal after use. Should a problem occur during the service life of the liner the end
user must be in a position to refer back to test reports even if not requested with the initial supply.
What should the end user look for when examining worn liners;
There may be an incentive to dispose of worn crusher liners and clean up the yard. An inspection of the worn liners is the best way to examine how successful you were with liner selection and identify any quality issues that have been exposed during the life of the liner. Changes and corrective actions can be made before ordering future sets. There are a number of areas to review and include:
a. The wear liner was no doubt selected to accommodate rock size and product size. This is usually the first area to review and includes examining the liner for high or disproportionate wear areas. The outcome may lead to a liner profile change, feed size change (Screen size) or feed rate change. The ability to choke feed the crusher is not always automatic or practical for the operator to maintain and may remain an accepted function of the plant. Whatever the case a decision going forward can be made.
b. Does the line have any cracks? Cast manganese steel has a shallow surface oxidised layer (≈ 1mm deep) following the severe heat treatment process and will often show small cracks usually visible after die penetrant crack inspection prior to use. These cracks, if not worn away, may become visible after liner use but will not extend into the ductile liner body. This is usually evident on the recesses in the fitting face of jaw crusher liners and are not a concern. Deeper cracks that are present should be investigated to determine the cause. This may require assistance from the supplier to determine the cause taking into account the many factors that may be responsible. For the Quarry Manager fitment is the main concern and this is relevant for cone and jaw crusher liners. If the liner is allowed to flex it will eventually through work harden and fail through fatigue. Tramp metal entering the crusher feed can be another source for failure. Do not accept this as the cause of failure too quickly as a good quality manganese will tolerate a lot of punishment before failure occurs. For the supplier fitment may also be an issue if the liner was not machined correctly. Excluding the fitment, machining and operation issues material becomes the next point of focus and a metallurgical examination may be the best way to obtain the possible cause. A 25mm minimum size sample cut from the liner using an angle grinder (to avoid heat input that will change the microstructure) is usually sufficient for testing.
c. Did you obtain the full life expectancy of the wear liner? A 70% consumption rate is a good starting point for cone liners and any deviation from this is worth a review. The removal of wear material from areas where it is not required and adding it to areas where it is should be considered particularly for high liner consumption applications. Your liner supplier should be able to assist with this request.
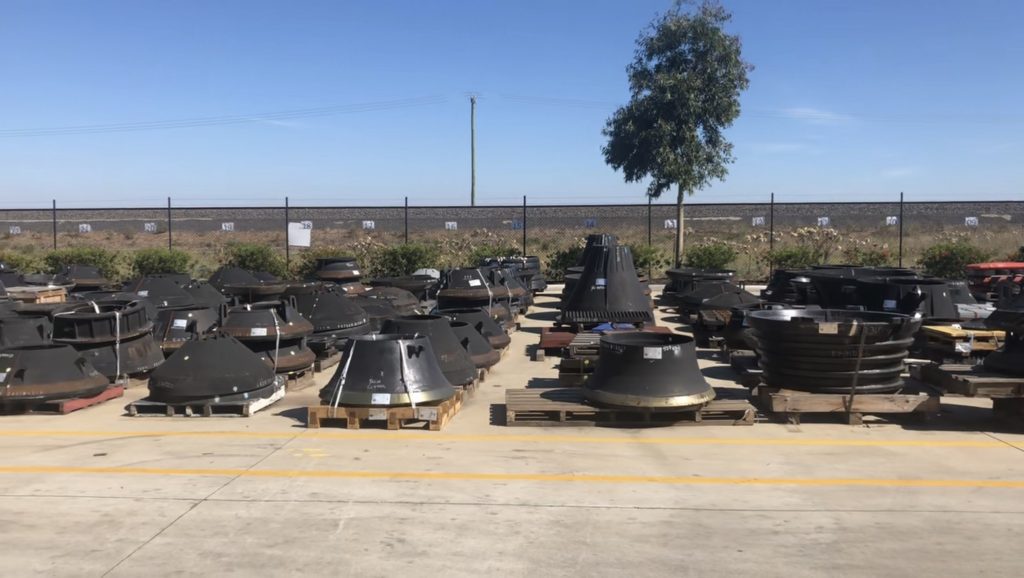
d. Look for unexplained depressions in the liner wear surface. This may not be a wear concentration area, but the result of internal casting shrinkage exposed once the surface material is worn away.
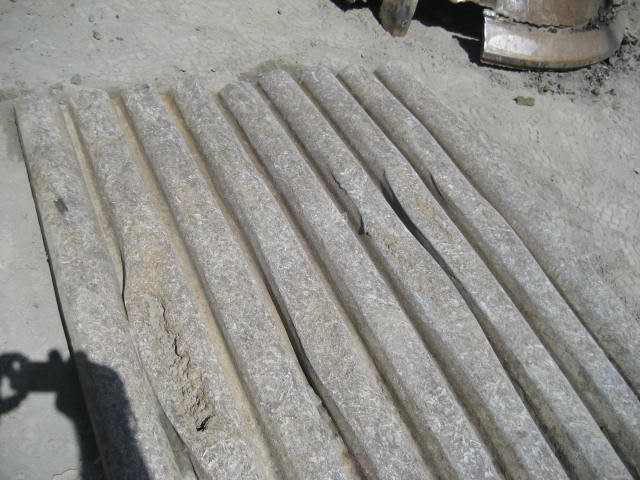
e. Manganese steel has >7% liquid to solid shrinkage that must be replaced by the controlled introduction of replacement feed metal during the casting process. The foundry can make significant manufacturing cost savings at the expense of the end user if this is not included.
There are many points to be considered when planning maintenance for your plant but in most cases the performance of the crusher (‘s) stands out front when it comes to product consistency, output and cost per tonne. The quarry manager must use all available resources, internal and from suppliers, to achieve the best outcome.
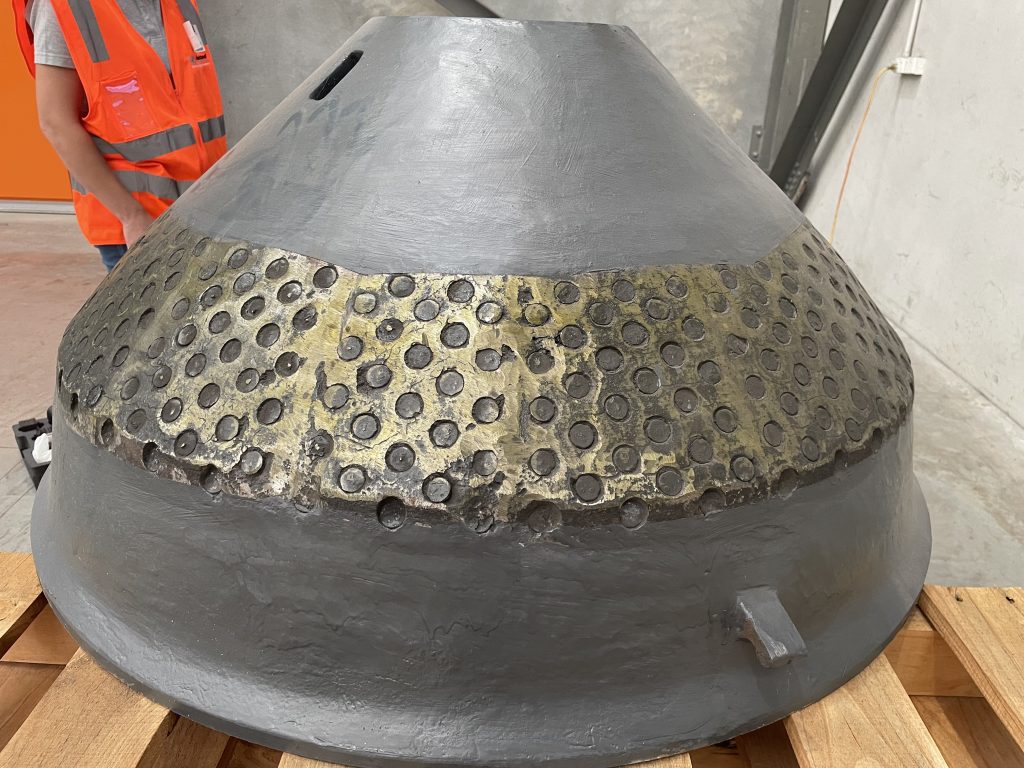
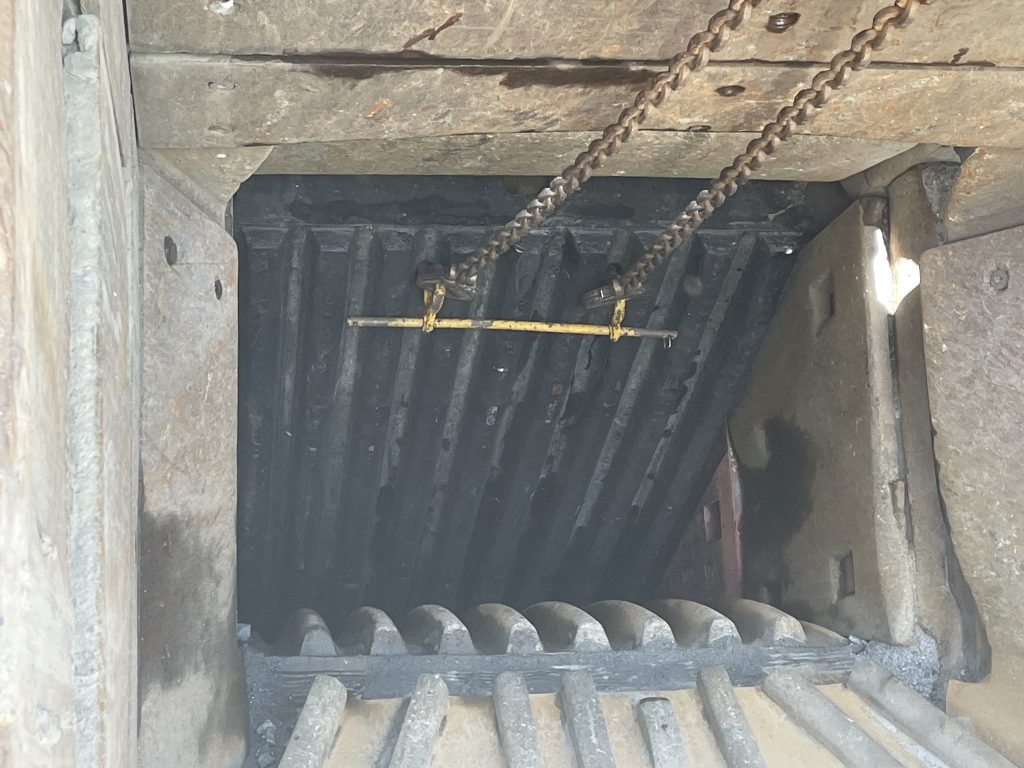
Manasafe lifting equipment)
Amsted Global (previously Crushing Equipment) has been a proud member of the CMPA for 21 years. Ongoing membership into the CMPA has ensured Amsted Global stays abreast of important topics and challenges facing the industry and has provided the business with a multitude of networking opportunities through workshops, webinars and other social events.

You must be logged in to post a comment Login