New rig marks out new drill and blast benchmark for quarrying
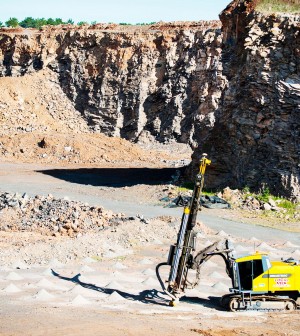
TOM ROSS, Business Line Manager, Surface Drilling Equipment from Atlas Copco Mining and Rock Excavation Australia reports on the growth and improvements to Local Mix Quarries in Anakie.
When family-owned concrete and quarry company Local Mix wanted to increase productivity at its Anakie hard rock quarry operation, it knew its plans relied on finding the right drill rig. After just a few months on site, the new Atlas Copco SmartROC T45 is increasing drilling efficiencies and reducing overall operating costs. Local Mix has been quarrying a basalt deposit outside of Geelong since 1993, supplying 500,000 tonne of crushed rock and road base material to the construction industry annually.
Since the mid 1990s, the company’s second-hand drill rig had been central to the company’s commitment to perform its own drilling, rather than using contractors. But when the company acknowledged the rig did not have capacity to meet its goal of increased productivity, Quarry General Manager Steven Richardson sought the best rig on the market to support his plans.
“I visited the Bauma show in Germany in 2013. It was there that we first saw the Atlas Copco T45. My first impression was that it appeared to be more advanced than others on show so we went away and did our research and found that the T45 outclassed its competitors in terms of technology, fuel savings, automation, precision and agility,” said Richardson.
“On returning to Australia, my quarry manager Mat Teesdale and I visited Mt Magnet, Western Australia with Atlas Copco to see the T45-10 (fixed boom). We were impressed with the results and saw that the flexible boom could give us the versatility required for the ground conditions we encounter”.
The decision to purchase a T45 soon after has proven a prudent investment, Teesdale praising the rig’s fuel consumption, productivity and drill efficiency.
“Since arriving on site, the T45 is consuming an average of 13.77 litres of fuel per hour, which is impressive enough, but even more so when compared to our old rig which was running at approximately x15.37 litres/hour, with increases to air of 4 bar & 115 l/s and an extra 9 kW for the rock drill” said Teesdale.
Trials of the rig, carried out in different terrains and climates worldwide, have all delivered outstanding results. In Australia it has been the same story. The SmartROC T45 impressed loyal users of the previously known ROCF9C by demonstrating a fuel consumption of less than 20 litres/hour, proving it lives up to its claim to increase profits from the very first day of drilling.
“The consumption we’re achieving is partly due to the rock we’re drilling, which is not excessively hard, but it is variable which can cause wear and tear on consumables when drill force is not matched to ground requirements. This is another reason we bought the T45 – it gives the operator exceptional control over the flush air produced so the machine produces only what is required. As a result we’ve been able to greatly extend the life of drill rods. The original drill rods are still on the machine, and after 8500 metres they show little sign of wear” said Teesdale.
The rig can be equipped with the hole navigation system (HNS), which makes accurate setup and collaring extremely easy. According to Teesdale, the HNS ensures the T45 is unmatched for its high level of automation which maximises drill efficiencies. Many aspects of the operative process, such as aligning the feed and the actual drilling, are automatic, which not only gives continuous, satisfactory results but also exceptional precision. The system is loaded with the drill pattern which can allow tramming to the optimal position from which to drill multiple holes at the required depth and angle, with the whole process driven and documented by the rig’s ROC Manager Program which provides detailed information for accurate decision making. Bore tracking of blasts has
seen accuracy between 85-100%.
This machine has also had a 3G modem installed rather than the usual base station system to access the GPS coordinates. This provides the flexibility to move to different sites while retaining all the features of HNS.
On site, the SmartROC T45 is also removing inefficiencies associated with traditional drilling mark out. It eliminates the need for tape measure marking of holes and its inherent inaccuracies, automatically and accurately collars holes, and assesses and drills blast holes at angles and depths which will deliver superior blast fragmentation. All this has added up to markouts being completed in 25% of the time taken previously, unprecedented blast fragmentation and greatly reduced operating costs. Drilling metres per engine hour have increased 23.7% due to vastly improved set up time, greater flushing air capacity and rock drill penetration.
Since taking delivery of the rig, Richardson has been pleased ith the time and cost savings which are promising a strong return on his investment.
“Our productivity has risen steeply since the T45 arrived. We’re not just reducing the cost of rock drilling, but have reduced the overall rock excavation cost. In addition we’re working faster than our needs so we’re now expanding our operations by doing contract drilling for others using the T45. The extra revenue was not factored into our purchase decision so it’s a great bonus on top of the exceptional results on our site.”
Richardson says the smooth transition of his team to the new machine was largely thanks to an attentive customer support team at Atlas Copco, which has shown commitment to his quarry’s success through their exceptional service.
“Our T45 was commissioned in March this year and, although it is the most advanced rig on the market, our operators and maintenance team have transitioned seamlessly to using it after the Atlas Copco crew spent a week on site training our team. At all times they have been responsive and available and truly committed to ensuring we get the most out of our new machine.”
Richardson also said that despite the rig’s sophistication, it is actually easier for maintenance crews as, with fewer components, there is less which can go wrong, so it is proving easier and less expensive to maintain than previous rigs.
“The T45 has fast proven it’s a rig we can rely on to deliver consistently accurate results, day after day. The only down side, if you can call it that, is our operator is not feeling as challenged now as the machine does everything for him!”
A great working relationship has formed between Associate Member Atlas Copco who have been active CMPA members since 2008 and Voting Member Local Mix Quarries since CMPA inception in 2000.
60 Seconds with a voting member . . .
What is your name? Mat Teesdale.
Who do you work for? Local Mix Quarries.
How many years have you worked for this business? 4 Years.
How many years have you been involved in the Industry? 19 Years.
What is your role? Quarry Manager – Anakie.
What does your job involve? Day to day Management of the site.
What is the best part of your job? Being involved in the extractive industry.
You must be logged in to post a comment Login