Attachments = Assets or Liabilities?
ADRIAN MASON, Director of eiengineering Pty Ltd reports on the benefits of well designed attachments.
YOU decide to purchase a new excavator and look at all the various makes and models and select one due to a certain set of criteria you find important such as: power, the way it operates or feels, build quality, servicing, fuel economy, cost of parts, availability of parts, etc., etc., etc.
So, you take delivery of your new machine in all its glory, then go and get the rusted old excavator bucket you’ve had for the past 10 years and put it on. In a couple of days you realise you’re not digging any more efficiently, nor have you gained any more power, it’s not digging any quicker, and you’re not getting any better fuel economy than your old machine!
The problem may not be with the machine, but with the attachments you have been using.
The truth is that most excavator buckets out there are no better at digging than a plow! Every bit of material that goes into those poorly designed excavator buckets is actually forced in by sheer power, using large quantities of power and fuel.
In reality, there are only three parts of any excavator digging bucket that should ever touch the digging material – the teeth, the lip and the side cutting edges. Any other part of the bucket that touches the material is just bad bucket design, sucking up extra power from the machine and using more fuel! This only costs the contractor more money and in this day and age when many of the dealers are pushing greater fuel economies, it is important to know that no matter how economical the machine is, if the bucket is not designed to dig efficiently, the customer will not experience the full benefits of the machine technology – and it’s costing you money out of your pocket
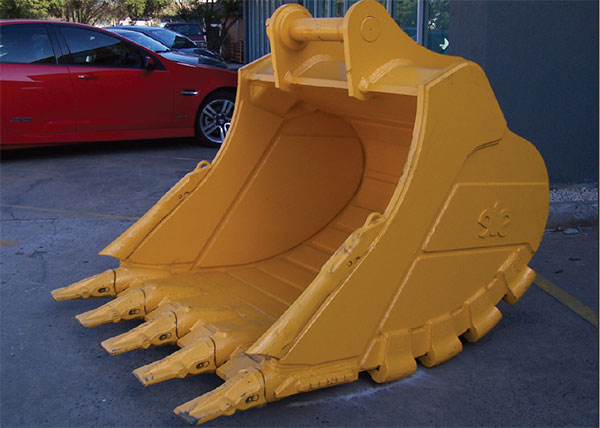
No different to a car and aerodynamics, the excavator bucket needs to have “earth dynamics”, so it flows through the ground easily and efficiently, minimising bucket drag – saving you money!
A well-designed excavator digging bucket should be able to return its cost within the first year of operation, making it an asset to your company – not an expense.
When looking for excavator buckets, it is important to consider the bucket design and shape overall:
- The bucket should be the correct shape for most efficient and economical digging performance
- It should have the least pin to point measurement possible, to achieve maximum power at the bucket teeth
- It should be tapered bottom to top and front to back for more streamlined, easier bucket flow
- The cutting edge should protrude the sides of the bucket enough to ensure good bucket clearance from the digging material
- Bucket teeth should be built into the bucket side wall to increase bucket strength
- Teeth should always be splayed to maximise clearance efficiency
- Bucket hangers should be long around the back plate to ensure maximum power and less bucket flex and fatigue
- The bucket should be manufactured from materials that offer robust service and long life.
- The bucket should not be too heavy, otherwise you are just using more fuel to move steel around and get less material capacity
- Bucket teeth should fit well so that there is no strain on the retaining pin.
- Bucket pins should be retained by bolts so they are easily replaced or turned when worn.
Bofors, a Swedish Steel company that has been around since the 17th century, and having at one stage been owned by Alfred Nobel, benefactor of the Nobel prize, has had a number of patents such as gunpowder, anti-aircraft artillery and the Howitzer machine gun.
In the 1970s, Bofors went about designing more efficient excavator buckets and wheel loader buckets. Much like a car in a wind tunnel, the bucket was designed to be streamlined as it passed through the substrate in the natural arc of the excavator arm.
Out of this research, the eleven major points discussed above were established and the double radius back-plate design of the eiengineering bucket was born. There are some manufacturers who use this bucket design today, but because of the technical aspect required to design and increased costs to manufacture, they are usually deemed expensive in the market place.
Eiengineering have been able to find a way to produce the Bofors designed bucket so that the excavator market can experience all the benefi ts of this brilliant and economical design at an affordable price.
Eiengineering design and manufacture excavator buckets that dig more efficiently, dig easier and dig more economically, so you can keep your money where it belongs – in your pocket!
The buckets are manufactured from Bisalloy which is three times stronger and more abrasive resistant than mild steel. Most buckets manufactured in Australia and especially China and India, are manufactured from mild steel which makes them quite weak and inadequate.
Some manufacturers compensate their lack of design expertise with larger steel plate sizes and bigger welds. This makes them strong so that they last a long time, but are very heavy – costing more fuel just to move the bucket around and still don’t dig efficiently – really just prolonging your financial pain!
Eiengineering will offer you excavator buckets designed to dig efficiently and economically and manufactured from robust materials at a price that offers great value for money.
For more information contact eiengineering Pty Ltd on 1300 852 820 or visit the website www.eiengineering.com.au
You must be logged in to post a comment Login