PREVENTATIVE MAINTENANCE
By: Brian Calovic
Quarry Manager Stawell Quarries
Earlier this year it was decided to fit Automatic greasing systems to the mobile plant at the quarry to reduce risk to operators by removing the need for manual greasing. By removing this task from the operator the risk of slips and falls, putting themselves in crush zones and exposure to conditions of dirt and grease is not necessary. The greasing systems also ensures an effective level of protection for the mobile plant.
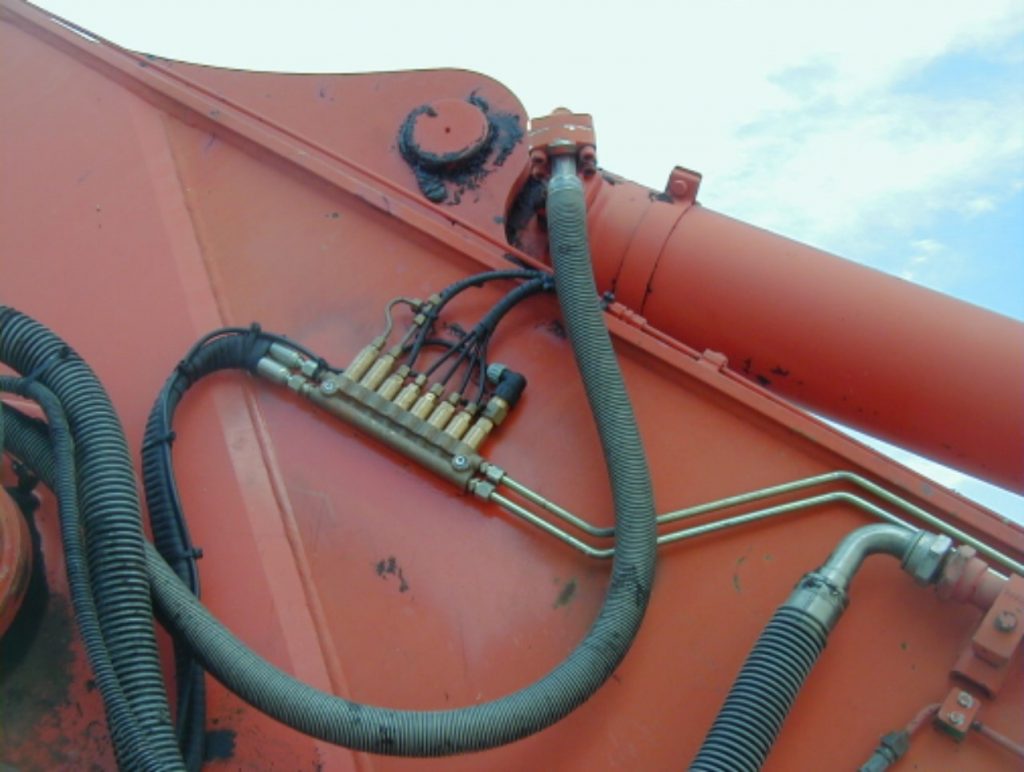
Grease is distributed through all points of the machine at pre determined intervals throughout the shift instead of once or twice at the beginning or end of each shift. By supplying smaller quantities of grease at more regular intervals the pins and bushes will never run dry. The amount of grease to each point is metered so that excess greasing does not occur avoiding damaging grit being attracted to grease points as well as no wastage of grease or grease droppings from the machines. The grease points remain covered with a layer of grease at all times reducing wear levels and accelerated wear once dirt and grit has found its way in.
The automatic greasing systems have been fitted to the sales loader and face excavator.
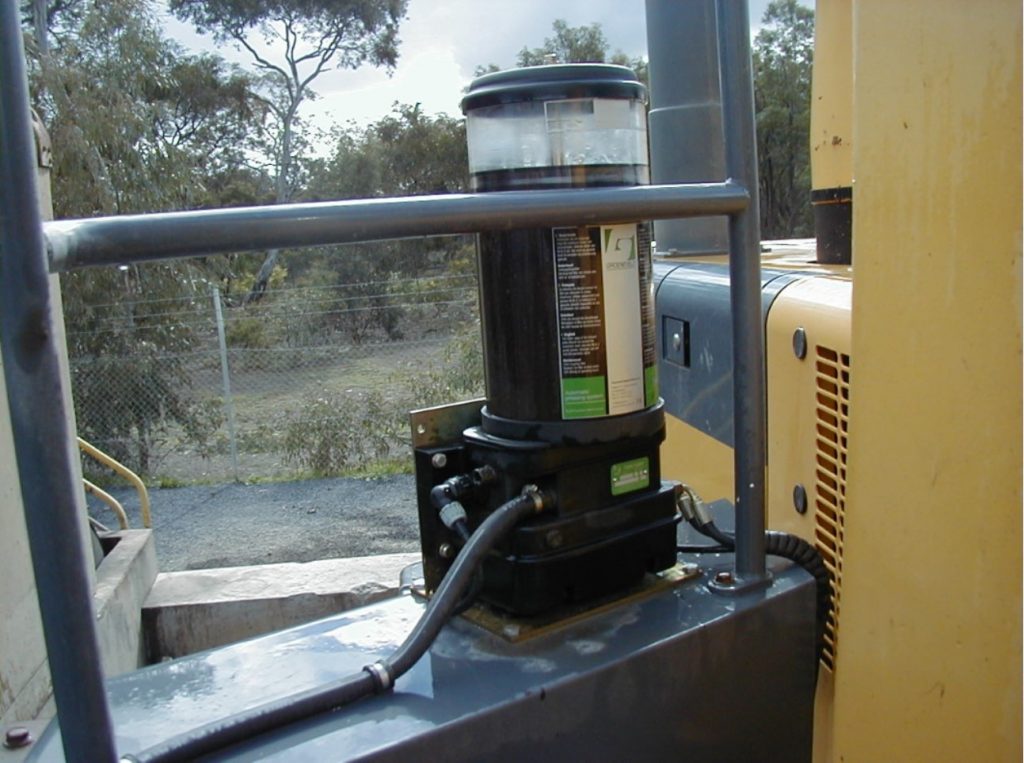
The Groeneveld automatic twin greasing system was the model chosen and fitted to the machines whilst in the Melbourne workshops for maintenance programs. The system consists of a grease pump with integrated control unit. Distribution blocks with metering units and a failure indicator lamp and mode switch with an integrated lamp.
All operations are performed automatically once the ignition is turned on and at pre defined intervals, supplying measured quantities of grease to all the points. The single reservoir last approximately 200 hours depending on the grease cycle selected by the operator being light, medium or heavy and is filled from the ground by a clip on connection to a grease pump and 205 litre drum of EP2 grade grease.
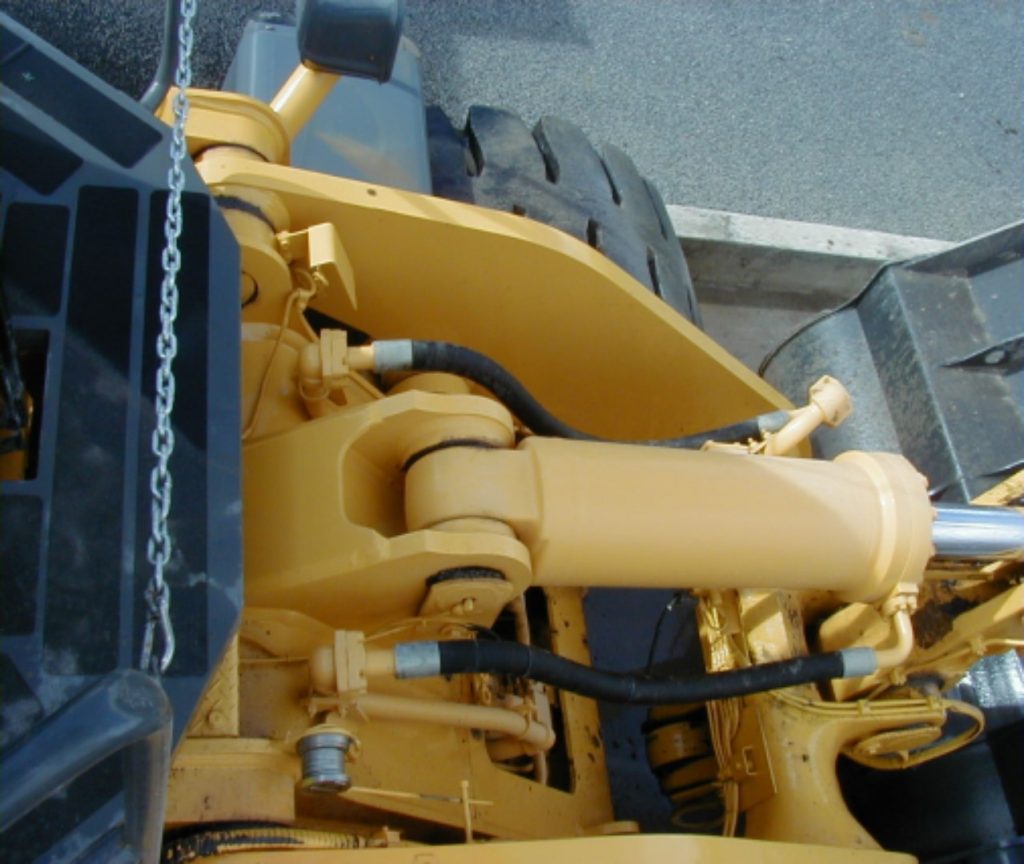
From the operators perspective the greasing units were received with some reservation. Because the operators could not see the amount of grease being metered to each point there was doubt that the units were working correctly. At the initial stages we found that the cavities around some of the grease points were slow to fill up because of the volume of grease they hold. This also led the operators to doubt that the system was working. A training session was run on site by Groeneveld to explain how the system worked and how we would know if it was not working. All the employees who attended the session were asked to provide a report to demonstrate their understanding of the grease system
From a management perspective the elimination of the operator having to carry out the daily task of greasing plant has removed a potential high risk area of operator safety, machine maintenance as well as environmental issues of grease containment at the grease points and storage and use of extra grease. Service bays and equipment is left cleaner with no need for manual greasing.
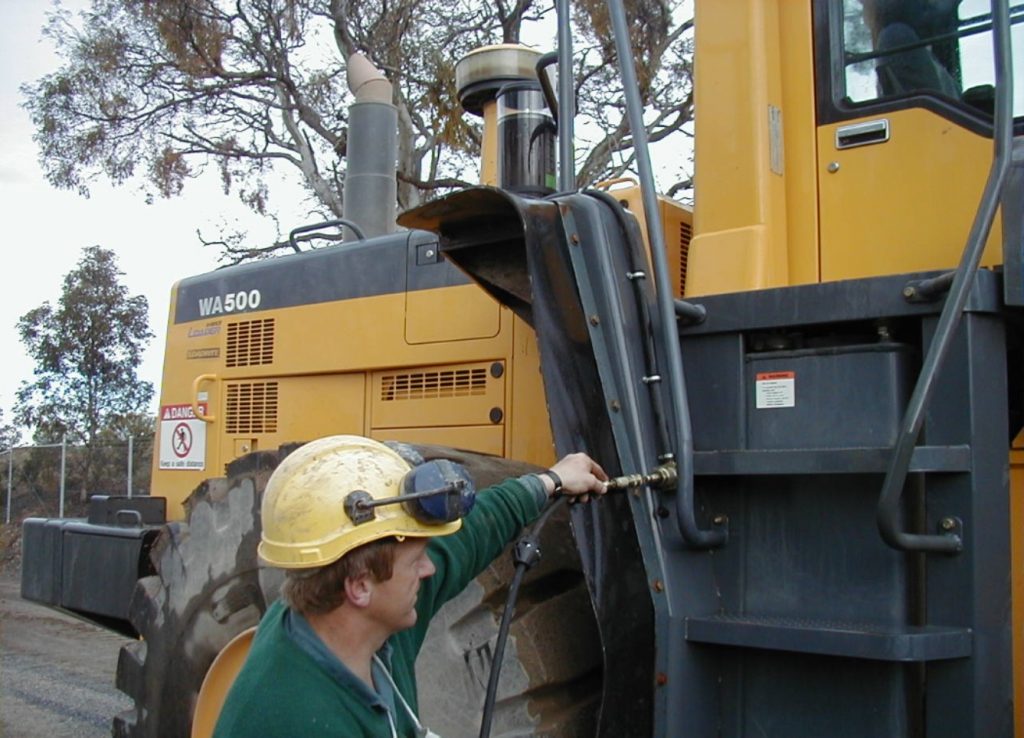
The possibility of operators failing to carry out daily greasing of plant resulting in costly down time for avoidable maintenance is removed. Pins and bushes will have a greater life expectancy and mobile plant will be kept in better condition over longer periods of time. The capitol cost of the grease units will surely be out weighed by the gains in the life of the machine pins and bushes as well as better conditions for the operators of the mobile plant. Relying on operators to keep the correct amount of grease at grease points is no longer a concern. More time can now be spent on daily checks and maintaining the mobile plant to meet with company standards.
You must be logged in to post a comment Login