CMPA QUARRY DRILLING WORKSHOP ‘04
Groups were organised to brainstorm the different areas of drilling operations. People were split up from their comfort zones of people they were familiar with, and put into groups from different backgrounds, levels of expertise and knowledge. Input from this different range of people resulted in a wider perspective and greater contributions. This created better procedures, and a better range of equipment, understanding, and skill levels.
People are seeing that they are being given the chance to have their say and make a contribution. As well as making changes to the way things are done, we are changing the mentality of people, and thinking outside of the square.
John Mitas’ comments highlighted that all people on all levels must be involved, if we are to successfully change workplace habits and methods. Employers, employees, contractors, suppliers and the community all have gains to be made from achieving our goals in OH&S compliance…
On Friday 26th March, 2004 I attended a CMPA workshop at Komatsu, Campbellfield on drilling in quarries. The workshop was organised so that on arrival people were greeted and put into groups to discuss the different aspects of drilling, with a broad range of knowledge and experiences. People from each company were split up to help spread the brainstorming concept throughout the groups, rather than having all of the same minds together.
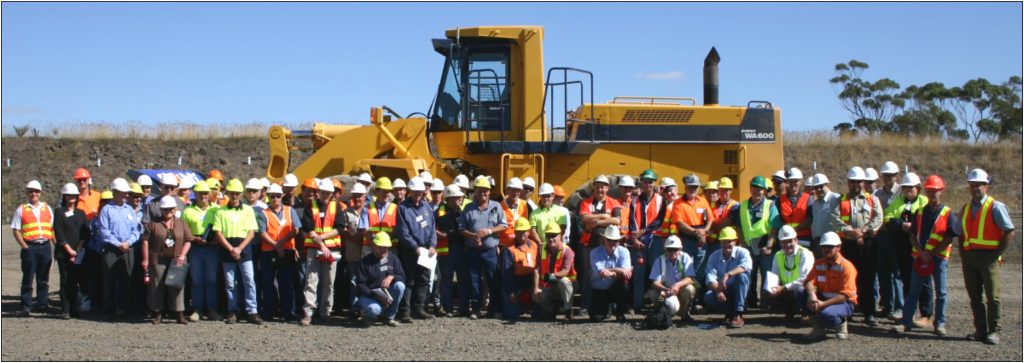
The workshop started with an introduction from Grant Phillips. We observed a minutes silence for lost colleagues as a show of respect. This also helped people to understand why they were there, and what they needed to achieve.
Jane Sims then gave an induction to the Komatsu site, and an overview of what we hoped the outcomes of the day would be.
John Mitas, Chief Inspector of mines, was next to take the stand, with a powerpoint presentation on Victorian legislation, obligations under the OH&S act, and duties of employers and employees. John’s presentation was straight from the slides, and did not vary from the guide notes as written. There was some question time at the end, although this was hurried to keep to the time frame allowed. Some questions were raised on guards, and what could be considered acceptable as far as using tools to remove them.
It surprises me that people are still more prepared to argue what is enough, instead of saying what more can we do to protect ourselves? Why is it that often the people that are being protected are the ones that put up the most resistance?
We discussed how the drill rig is covered in the regulations under ‘plant’ and how a proactive approach must be adopted to ensure safe practises at all times. Risk Assessments must involve all people concerned or exposed to the potential risk for best results. Risk Assessments should not be done by single people, being management or hands on operators. Focusing on equipment pre-purchase gives us the power to demand issues are addressed by manufacturers before supply or commissioning.
The group that I was a part of discussed tramming, loading, and transport of drill rigs. A quick Risk Assessment was done by our group, led by Craig James, with some of the issues to be addressed pre-purchase:
- Risk Assessment
- Operator control and visibility
- Training, both classroom and practical
- Commissioning, familiarisation and induction
- Competency based training
- Remote operator loading
- Written procedure for loading, transport and tramming
Hayden Carter, Department of Primary Industries OH&S Industry Coordinator, was next to present to us as a group. His session discussed what hazards are, and how we can identify, assess and control them. We discussed why it makes sense to manage risks and that we are obliged to put in place controls for hazards and to monitor and maintain these controls. People seem to get the message to a point, but still do not understand the importance of documentation.
We discussed how a control hierarchy works. We looked at some slides of work places with a forklift, a conveyor, bottles of unknown liquids, a loader crush point and an electrical cabinet. We also spoke about what the hazards were, and the controls that should be used.
Next we loaded onto the buses and went to Northern Quarries for a practical look at some drill rigs and the areas each group had been assigned. As groups we discussed and observed the drill performing what we had been asked to look at, and then discussed how it could be done better. Our group found loading and unloading the rig to be the highest level of risk. We discussed the need for a spotter to guide the rig on and off the float, the training and procedure documents required, competent operators, and the way in which operators dismount the rig once on the float. I also questioned why it cannot be done by remote control so the operator is not at risk, as in some mining equipment where the operator can stand away from their machine and operate from a handset remote.
The Northern Quarries site was excellent and left no one unimpressed by how well the site was presented.
The afternoon session continued on with Hayden and Jane conducting class room group exercises on identifying potential hazards and controls used.
Each group identified hazards and controls that could be used in their area of discussion. The hazards and controls were put into lists and presented by the leader of each group.
It felt as if we were at a larger weekly toolbox meeting, where everyone can sit in as an equal group and openly discuss making things better. I would recommend more of these workshops in different areas and offer congratulations to the CMPA and all involved who have made it possible.
Brian Calovic
Drill rig pre start & end day safety checklist
Following the completion of the Drilling Workshop, the Secretariat has been sorting the hazards and risks that were identified on the day into a meaningful and useful set of documents.
The first of three documents to be released will be the “Drill Rig Operator’s Pre Start and End Day Safety Checklist”. The remaining two documents, being “Checklist for Drilling Rig Operations” and “Quarry Driller’s Blast Hole Report”, will be released once the risks identified at the workshop are fully incorporated into them, and the documents have been reviewed by the DPI and CMPA members.
The purpose of this first document is to initiate a document trail for tasks carried out on the drill rig on a daily basis and to remind the operator what they need to inspect. The document will be made available to all CMPA members for around $20.
You must be logged in to post a comment Login