SAFETY UPDATE (Issue 18)
FATAL GRINDER ACCIDENT AT QUARRY
Incident
A welder was carrying out maintenance on a quarry excavator bucket. He was using an angle grinder to prepare surfaces for welding when the disk disintegrated.
Circumstances
The hand-held angle grinder was fitted with a 230 mm diameter cutting-off wheel and when it disintegrated, fragments penetrated the victim’s chest and abdomen. He was rushed to hospital by rescue helicopter but died the same day.
Investigation
This is continuing but initial inspections show that the grinding machine and cutting disk were not compatible—and the grinder was not fitted with a guard.
Recommendation
Grinding machines and abrasive wheels should always be used in accordance with the manufacturer’s instructions.
In particular:
- Always ensure the maximum speed (the no load rpm) marked on the abrasive wheel is greater than the rated speed of the grinder.
- Do not use grinding wheels that are larger than the maximum recommended size,or worn down wheels from other grinders.
- Never use grinding wheel power tools without the wheel guard attached to the tool and positioned for maximum safety.
- Store and handle abrasive wheels with care and inspect them for chips or cracks before installing. Do not use any wheel that may be damaged.
- Refer to Australian Standard 1788 – Abrasive Wheels for more detail.
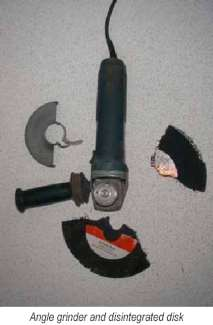
Safety Soapbox – Absolute Shocker
This issue’s Absolute Shocker was discovered by a WorkSafe inspector on a farm shed construction site in Victoria’s north. A Prohibition Notice was promptly issued.
As a method of gaining access to the 7 metre-high roof, it is certainly novel! It involves climbing an unsecured ladder, climbing up the face of the homemade work platform, and then leaping to the roof – a roof without a
stick of perimeter guard railing.
The tractor’s hydraulics automatically lower once its motor is switched off; a safety feature so that raised loads won’t be left hanging. These geniuses simply left the motor running without an operator at the helm.
We are pleased to report that, on his return visit to the site, the inspector found that the scaffold access tower had been erected and full perimeter roof guarding had been installed from an elevating work platform.
Now that wasn’t too hard, was it?? And now the tractor can be put back into service, doing what it was designed for, and not what is should never have been used for.
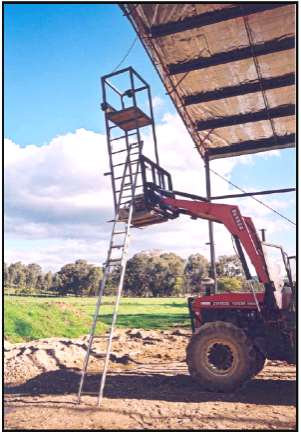
PRIMARY HOPPER—FALL FATALITY
Accident
A quarry worker was fatally injured when he fell 2.2 metres into an almost empty primary feed hopper of a crushing plant.
Circumstances
The worker had reversed his truck up to the primary hopper in order to discharge a load of quarried material.
He then walked to the rear of his truck, before falling into the hopper. In order to discharge the load, it was not necessary to leave the truck. It is unknown why the driver did so.
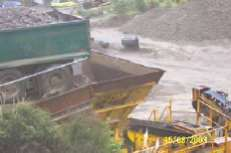
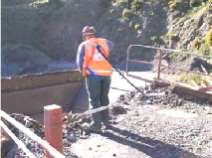
Investigation
The investigation disclosed that:
- Nothing prevented workers falling into the hopper while standing close to it, using a rod to free materials that were stuck or jammed on the sides of the hopper. This condition was common, particularly when the quarried material was wet, and
- While guardrails existed at the sides of the vehicle approach to the hopper, a dedicated observation area did not exist, should such an area be required for viewing into the primary hopper.
Remedial work occurred for both of these conditions, resulting in the use of:
- A securely anchored static line to which a safety harness is attached, to minimise the harm that could occur should a person fall. For ease of accessibility, the static line and harness are kept in a securely locked weatherproof cabinet a few metres from the primary hopper.
- An observation walkway with top and mid guardrail protection and an end return platform was erected to the driver’s side of the approach to the primary hopper.
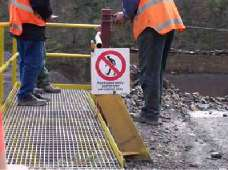
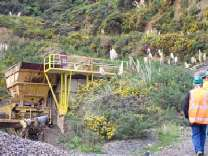
Recommendations
The investigation reinforced the fact that a person can fall a short distance and sustain serious (in this case fatal) injury.
As part of their hazard identification, those who operate quarries, mines and other workplaces, need to identify hazards, including exposure to falls, and take all practicable steps to ensure people are not harmed from that exposure.
While not always possible, isolation (use of guardrails, barriers, or gates) is the preferred method of fall prevention, rather than minimisation through the use of safety harnesses.
Another way to prevent exposure to a fall is to ‘design out’ that exposure. That is, carrying out the task in a different way so a person is not exposed to a fall.
FATALITY REPORTS
WOODYARD WORKER KILLED—TAS
A man was killed after he was crushed between a front-end loader and a truck in a southern Tasmanian woodyard.
The 35-year-old man was pinned between the front-end loader and the front of a Mack truck. Ambulance officers attended but the man died at the scene.
MINING FATALITY—WA (1)
A 57-year-old prospector was involved in an accident on a small mine that he was working with his brother on 24/10/04. He sustained injuries from which he later died in hospital.
He had travelled up a small shaft in a kibble and reached the surface. While attempting to dismount from the kibble he fell some 7-10 metres down the shaft. He was rushed to hospital by his brother, however he lapsed into a coma from which he did not recover.
MINING FATALITY—WA (2)
The body of the mining superintendent at a decline access underground mine in the WA Goldfields has been found underground in suspicious circumstances. Explosives appear to have been involved.
The body was located on 8/10/04 at a stockpile in the decline by a shift boss. No one else was present and there were no witnesses. There was no work currently being undertaken in this area of the mine, there consequently appears to be no chance that a stray production or secondary blast had been involved. The deceased suffered massive trauma to the head.
MINING FATALITY—QLD
On 22/10/04 a female visitor to a small open cut gypsum mine site 150km south west of Winton was fatally injured when run over by a front end loader. The loader operator had completed loading one side of his truck and when he reversed around the truck to load the other side, he noticed the visitor lying injured on the ground.
INADEQUATE ISOLATION & TAGGING PROCEDURE LED TO DEATH OF A WORKER – NSW
An employee of a labour hire employee was killed at a NSW workplace when he was drawn into an uncovered conveyor. The worker was clearing blockages in a conveyor, which involved isolating the power and removing the cover. The worker then sat on top of the conveyor to watch two co-workers clear another conveyor. However, the conveyor he was sitting on was unexpectedly activated, drawing the worker in and killing him.
Although the conveyor was initially isolated, and workers were required to stand back and shout “all clear” prior to restarting the conveyor, there was no system for a head count to ensure everyone was clear of the machinery, or a lock out system where all involved had to remove their own locks prior to the system being started again.
LANDFILL ACCIDENT – USA
The Polk County Sheriff’s Office has identified a construction worker found buried in sand at the Polk County Landfill in Gentilly.
Sheriff Mark Letexier said Wednesday that Bryce Bosh, 41, was found dead late in the afternoon. Bosh was an employee of Zavoral Construction Company.
Landfill manager Dan Wilson said Bosh was a machine operator, and apparently was behind a truckload of sand when it somehow was dumped on him. Wilson said the driver of the truck left without realising what had happened.
INCIDENT REPORTS
BURNS INJURY WHILST WORKING IN TANK #6/2004
A maintenance worker suffered serious burns when sparks from the angle grinder he was using in a vertical, open process tank,caused a fire. The worker was wearing a synthetic shirt under a woolen jersey. It appears that his shirt caught fire. Investigations have revealed that the atmosphere in the tank had become enriched with oxygen from an oxygen addition line. The line had not been correctly isolated, and a non-return valve in the line had also been incorrectly fitted.
TRUCK DRIVER STRUCK BY FALLING WINCH #4/2004
A truck driver was struck on the side of the head by a falling electric winch as he attempted to remove jammed rocks in a grizzly at the primary crusher. There were no major injuries sustained as a result of the incident.
An electrical winch was attached to an overhead gantry at the primary crusher. The truck driver positioned the electric winch so that the hook at the end of the wire rope could be located underneath a jammed rock. The truck driver then turned on the electric winch resulting insignificant upward force being applied to the hook. At this time the electric winch detached from the overhead gantry and fell into the primary crusher, glancing the operator’s head as it went by.
EXCAVATOR BRINGS DOWN OVERHEAD POWER LINES
An excavator came into contact with overhead powerlines in a quarry, pulling down three high voltage lines. The excavator operator was not injured nor was any damage caused to plant.
An excavator and truck were being utilised to clean out a shallow quarry drain, which runs through a power line easement. After completing the first section of the drain the excavator was then re-positioned to enable the second part of the drain to be cleaned out. On the first sweep of the excavators arm, contact was made with the three power lines, these broke and fell to the ground.
DPI SIGNIFICANT INCIDENT—1
On 16/9/04 two contractor owned and operated road registered trucks came together in a stockpile area. The loaded truck was leaving the stockpile area, while the empty one was arriving. The accident was low speed impact resulting in slight injury to one driver (bump on head, no broken skin, no seat belt) and bent chassis on one truck. Incident being investigated.
DPI SIGNIFICANT INDICENT—2
On 24/9/04 a dump truck rollover occurred after loading. The rollover occurred after the truck failed to turn up the haul road and continued straight into a pile of rock. The driver was injured and taken to hospital. Currently being investigated.
DPI SIGNIFICANT INCIDENT—3
On 30/9/04 there was a report of a fire in an underground haulage vehicle, which was believed to have been started by an electrical f a u l t . Currently under investigation, emergency evacuation procedure taken.
DPI SIGNIFICANT INCIDENT—4
On 18/10/04 a CAT IT machine had contacted a wall of decline (possible run away). No injuries were sustained, however the machine was damaged. Currently under investigation.
DPI SIGNIFICANT INCIDENT—5
On 22/10/04 a stacker collided with a dozer. There was damage to equipment, however no injuries were sustained.
DPI SIGNIFICANT INCIDENT—6
A person visiting a quarry on 22/10/04 approached an excavator and was hit on the head by the boom. The person was knocked unconscious and taken to hospital with injuries to the scalp and ear, being released 6 days later. Under investigation.
DPI SIGNIFICANT INCIDENT—7
On 29/10/04 explosives were found outside a magazine. Currently under investigation with Victoria Police.
CHANGES TO EMERGENCY EXIT SIGNS
Supplied by “OAMPS—Workers’ Compensation Occupational Health & Safety Newsletter”
Please be aware that under proposed changes to Australian Standard AS/NZS2293.1 – Emergency evacuation lighting for buildings—system design, installation and operation, and AS/NZS 2293.3 -Emergency evacuation lighting for buildings – Emergency luminaries and exit signs, the word ‘Exit’ will lo longer be used to indicate emergency exits, but will be replaced with a graphic design of a man running through a door.
There are a number of other proposed changes in the drafts, including:
- Revising the viewing distances for exit signs
- Restricting the use of arrows in exit signs; and
- Proposing that exit signs should not be permitted to be used as emergency egress luminaries.
You must be logged in to post a comment Login