EFFECTIVELY RUN SCREENS
Are your screens running effectively? Below is an extract from the CMPA’s “Conduct Screening Operations Reference Manual” providing some handy hints on how to effectively operate various screens.
THE following checks should be conducted several times during a shift to ensure screens are not over or under loaded.
Use your senses of hearing and smell to confirm screens (bearings) are not overheating or if there are loose bolts or cracked members.
Ensure feed material is evenly distributed across the width of the screen.
Ensure screen mounting springs are not bottomed out due to overloading of the screen, fatigue or broken springs.
Check screen operation for overloading which is indicated by cantering (where the screen tends to float rather than vibrate).
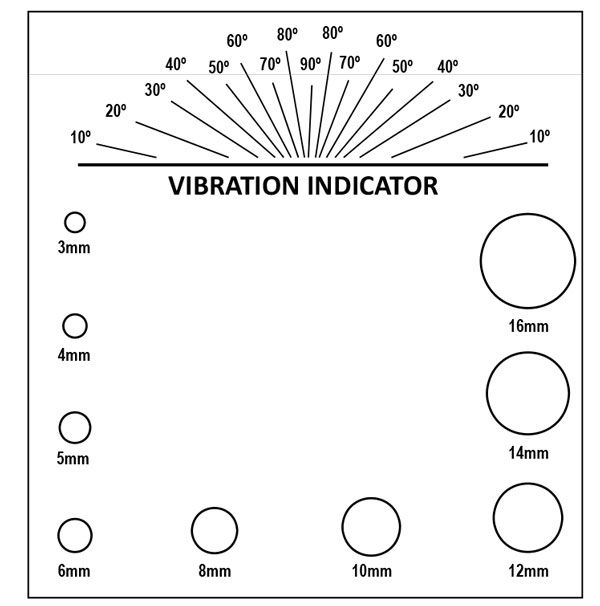
Vibration Indicator
Ensure pivot motor base is free to move (used with v-belt drive).
Inspect for pegging, blinding or obstruction of the screen media.
Ensure the screen body and peripheral attachments are not touching any area of the support structure.
If spray bars are fitted in a washing application, ensure the correct flow of water is available and the spray nozzles are clear.
INCLINED AND HORIZONTAL SCREENS
Check for screening media flapping caused by incorrect screen cloth or mat tension which can cause failure of the media or damage to the screen.
Visually check bed depth of the material discharging off the end of the screen (depth should not be greater than three to four times the aperture size, e.g. if the mesh aperture is 25mm then bed depth should be less than 75mm – 100mm).
Ensure motion of the screen is consistent at the top and bottom of the side plates on both sides of the screen.
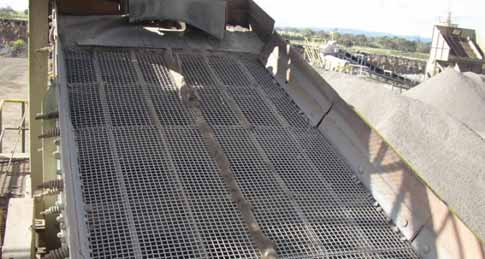
CIRCULAR MOTION SCREENS
The throw of a circular motion inclined vibrating screen can be checked by marking a point on the side plate, as close to the mechanism as possible, the circular vibration motion will form the point into a circle, the diameter is the screen throw.
If the screen is operating correctly the motion at the four corners will be elliptical pointing away from the mechanism, any variation to this indicates the screen is not operating correctly.
A variation could be caused by uneven support spring heights, different thicknesses of counterweights on either side of the screen, or spillage on the support structure or chutes.
Screen manufacturers will provide a vibration (throw) indicator card that has a number of circles with diameters, representing the various throws; the card is magnetic and placed on the side plate near the mechanism, when the screen is stopped.
When the screen is running, the motion is the diameter of the circle that forms a central dot on the card, only one circle will form the dot.
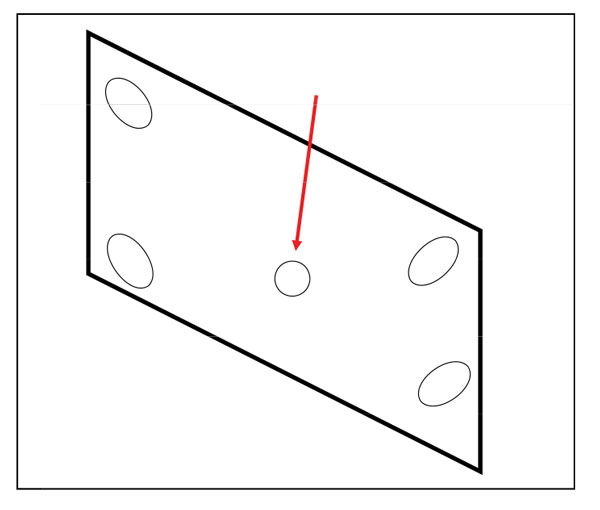
Plates of the Screen
LINEAR MOTION SCREENS
The throw of a linear motion screen can be checked using the same card. The indicator card is put on the screen in a horizontal position and the throw is indicated by the appearance of two circles just touching each other, the throw is the diameter of this circle.
You can check the angle of attack (the angle the screen vibrates in a straight line) at the top of the card, lines radiate out from the horizontal at various angles, only one of these lines will be solid when the screen is running, this is the angle of attack.
The same problems can occur with a linear motion screen as with a circular motion screen.
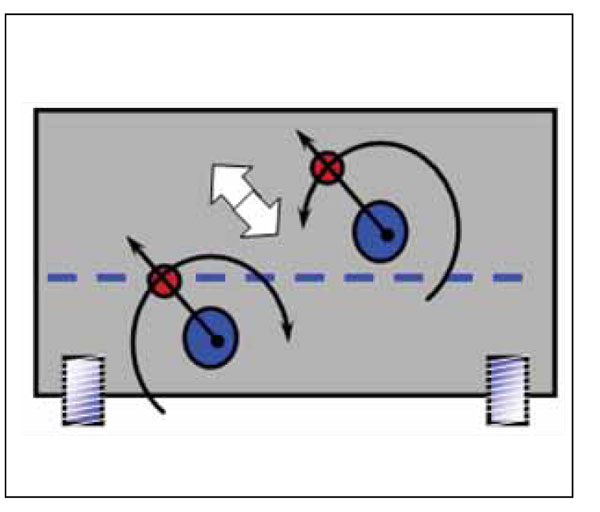
seen on Side Plates of the screen
GRIZZLY SCREEN
Check screening media (grizzly bars) condition. Damage or loose bars should be reported to your Supervisor as this may cause failure of the structure.
TROMMEL SCREEN
Ensure brushes (if fitted) are working effectively Ensure product is removed from under screen before it comes into contact with screening mechanism.
You must be logged in to post a comment Login