Fuel saving alternatives for crushing and screening
JASON MACDONALD, Product Manager – Crushing & Screening for Onetrak has summarised some useful fuel saving alternatives for your crushing and screening operation (Associate member of the CMPA since 2008).
With ever increasing costs of production in the crushing and screening industry, any possible savings can lead to a big increase in profitability. Is the current diesel price eating into your bottom line and forcing you into the red? Are you aware of some of the options that are available? Diesel/Hydraulic, Diesel/Electric, Electric/Hydraulic and Full Electric? Each has its own advantages and disadvantages.
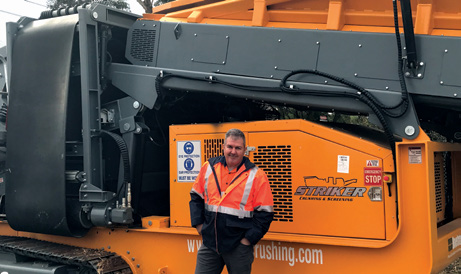
During the early 2000’s most jaw and cone crushers were;
- Diesel/Hydraulic hydrostatic system that drove the crusher by means of a hydraulic pump. This did offer the benefit of being able to reverse the jaw if it became blocked or when dealing with sticky material. This resulted in the engine running at nearly full load all day, even when the crusher box was empty. They also required large hydraulic tanks of up to 1400 litres. The use of load sensing pumps and direct drive configurations results in achieving approximately a 25-30% fuel saving. Hydraulic motors are usually lighter and smaller than their electric counterparts and don’t require a licensed electrician to remove or work on them – especially in remote areas. Hydraulic motors are often more expensive than an electric and with the oil required, need filters, pumps and regular servicing and generate heat that needs to be cooled.
- Diesel/Electric has been around for a while but started to become more common on tracked equipment from 2010 onwards. It offers the advantage of faster speeds, programmable speeds and stop positions for greater accuracy. If your application requires a lot more force, then a substantially heavier and larger electric motor will be required.
- Electric/Hydraulic is similar to Diesel Hydraulic but is a cheaper operational option as it can be run from a Genset or Mains Power and this reduces the servicing issues resulting from running a diesel engine, particularly in dusty conditions. A blown hose can result in contamination of the product being processed or the environment around the equipment.
- Full Electric will sometimes have a small diesel engine on board to allow the unit to track on site and load or unload from a float and then connect to mains power or genset to achieve greater savings. This can also mean that multiple units can be plugged into one genset or the grid resulting in multiple reductions in servicing costs.
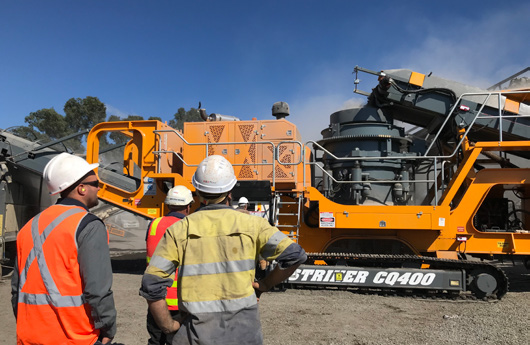
The electric units require a qualified 3 phase electrician to work on them which can be an issue when you are out of the main cities, while the hydraulic versions can be repaired by the hose doctor that is in nearly every town or close by to service earthmoving equipment.
With a hybrid drive system, it is possible to achieve approx. 50% savings on energy costs, cost of ownership and maintenance costs while a full electric system can provide savings of approx. 70%. This can also provide significant improvement to supply chain logistics if the large amounts of diesel don’t need to be transported to a remote location.
In a traditional fixed plant quarry application one of the biggest costs is the load and haul cycle from the quarry face to the fixed plant – especially if it is an uphill run or a long distance. Typically, these costs increase over a quarries life as the hole gets deeper and potentially further away from the fixed plant. Crushing at the face results in lower transport costs, faster cycle times with no oversize being hauled.
If possible and depending on the sites layout there is also the possibility to load the sales trucks at the mobile crushing plant area, thereby gaining further cost savings.
As quarrying, mining and earthmoving operations introduce a variety of hybrid excavators, dozers, loaders, graders and dump trucks, the hybrid crusher and screen are also helping to make inroads into cost reductions.
Stockpiling with conveyors also offers significant savings over wheel loaders – no wages, greatly reduced fuel burn, less capital outlay and much larger stockpiles in a smaller area – less segregation of product and higher levels of safety than driving a loader up and down a stockpile.
Additional benefits include safer working environments for equipment and employees and increased “brownie points” for reduction of the environmental footprint of the organisation with reduced emissions/greenhouse gases. A good corporate citizen.
Striker Crushers have utilised load sensing pumps for a long time and offer the E-Trac option of Full Electric, Electric/Hydraulic and Diesel/Electric along with Plug and Play to allow all equipment to communicate to maximise performance.
If you would like to discuss your application and talk to a product specialist contact Onetrak on 1300 727 520.
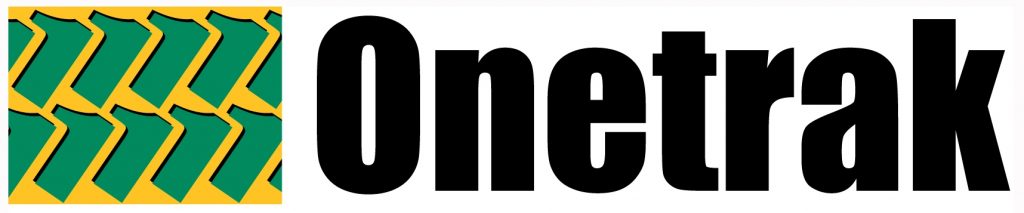
You must be logged in to post a comment Login