Personal Protective Equipment (PPE) requirements
GAVIN MOREIRA, Member Services Manager from the CMPA provides an extract from CMPA’s “Worksafely Reference Manual” and “RCSD Management Guideline” on PPE requirements.
Personal Protective Equipment (PPE) must be utilised in situations where other methods of controlling hazards cannot be used or require support. PPE is regarded as the last line of defence, and as such is listed as the lowest order of Control in the Hierarchy of Controls, a legislative requirement.
The following PPE must be worn where directed on site:
• Eye protection
• Gloves
• Hard hats
• Hearing protection
• High visibility clothing
• Overalls, shirts, winter jackets and wet weather gear
• Respirators and dust masks
• Safety footwear
• Welding shields, aprons and boot spats
Clothing
Overalls should be worn whilst working in RCSD environments and then removed so RCSD is not carried into the operator cabin, lunchroom, office, car or home:
• Remove overalls while you are still wearing a respirator;
• Use dust booth where available;
• Do not shake out dusty overalls;
• Do not take dusty overalls home;
• Arrange contract supply and cleaning;
• Place in the bin provided for cleaning;
• Replace on a daily basis.
Gloves
Only use gloves suited to the work being carried out. If using chemicals or hazardous substances consult the SDS for the correct type of gloves.
• Riggers gloves worn when carrying out maintenance tasks;
• Rubber gloves worn whenever handling cement dust or wet concrete to prevent dermatitis.
Hearing Protection
Not all hearing protectors are suitable in all instances; the correct class of protector must be used for different noise levels. The employer should provide the correct hearing protection for the level of noise present.
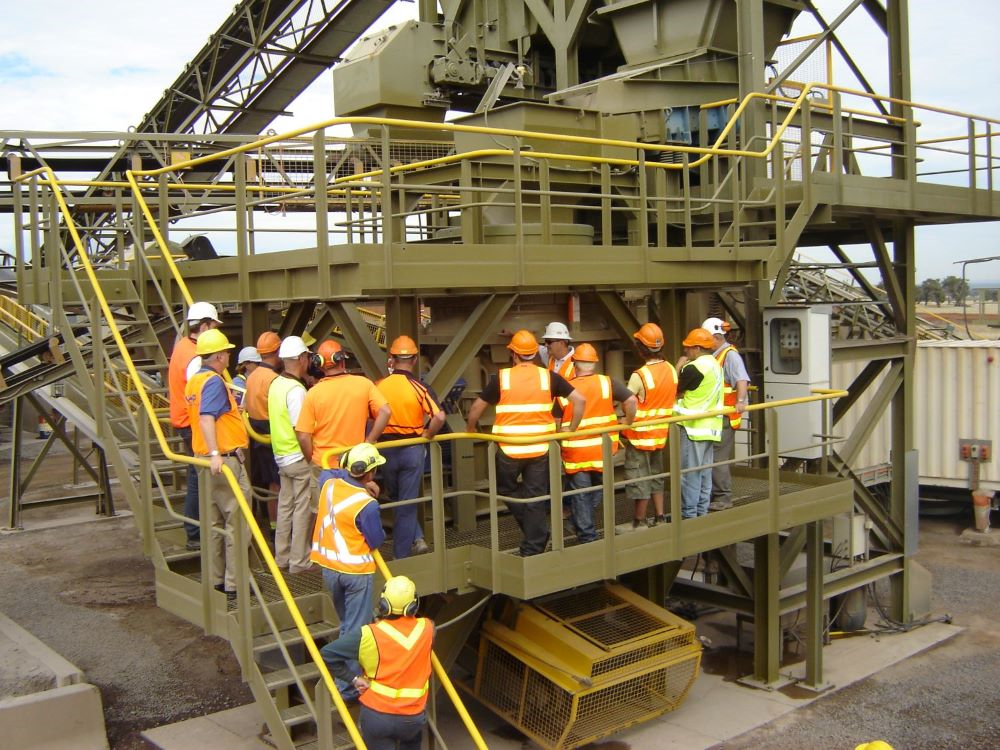
Work Boots & Shoes:
• Work boots worn outside in RCSD environments should not be worn in mobile equipment, internal workstations and office or amenities
• Slip on shoes should be provided for this purpose. Wrap around Safety Glasses and Sealed Goggles:
• Wrap around safety glasses worn at all times while in the vicinity of the processing plant;
• Sealed googles worn when working in areas where airborne dust is visible and in enclosed areas such as screens;
• Eye protection equipment must be appropriate for the task;
• Best practice quarries mandate use across whole of site excluding administration and amenities areas.
Respirators and Dust Masks
Use the correct respirators or dust masks for the conditions. If you are unsure which mask is required for an application, contact the local distributor who should be able to assist. For instance, disposable dust masks can be used in most dusty conditions, but where particles are very fine or where fumes or vapours are present, a respirator with the correct particulate or organic vapour filter may be more appropriate. These filters have an arrow to indicate the side which should be closest to the face.
In certain conditions, an Air Fed Respirator Hood/Helmet with safety shield may be more suitable. Specific training is required to use this equipment.
The CMPA recommends a P2 Dust Mask with a return air outlet valve as a minimum standard. Prior to use, it is important to check the face piece for cleanliness and damage and ensure it fits. When using a P2 Dust Mask, always ensure a positive fit by carrying out a quick positive/negative pressure test.
• Adjust strap and nose clip to suit;
• Completely cover the mask with both hands and inhale sharply. The respirator should sink onto your face and should be tested prior to each use;
• If you feel a stream of air around the edges (particularly at the bridge of the nose) then you have a poor seal;
• Adjust strap and nose clip and re-test;
Once finished, ensure disposable respirators are appropriately disposed of in a container that prevents dust from re-entering the environment. If reusable masks are in use, ensure they are cleaned and stored accordingly to the instructions.
Storage and care of PPE:
• PPE must be stored correctly so that it does not become damaged, worn or contaminated;
• Disposable dust masks will be stocked in appropriate storage cabinets around the work site;
• PAPR should be stored in the site’s safety equipment cabinet and cleaned after every use.
Further information on CMPA publications can be found at
https://cmpavic.asn.au/publications/
or by contacting 03 5781 0655 or [email protected].
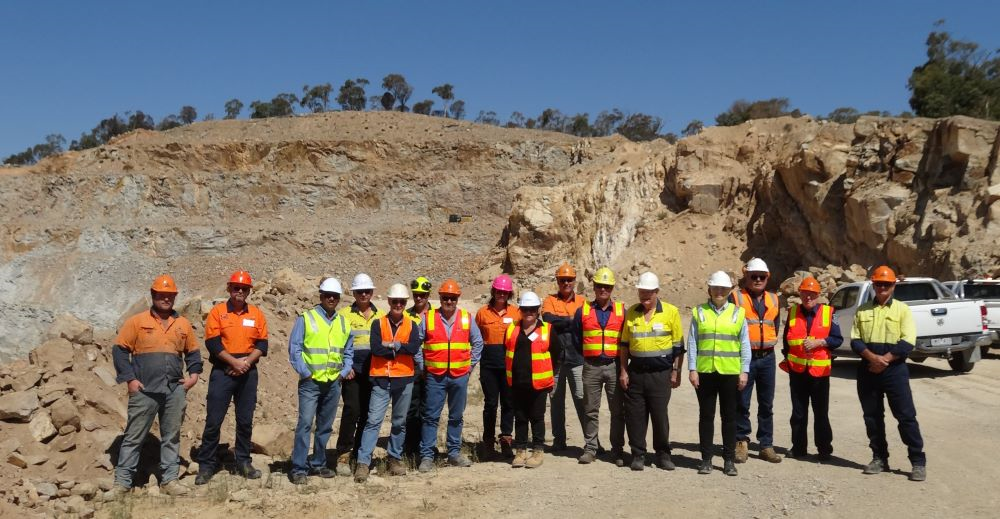
You must be logged in to post a comment Login