CDE SmartTech is allowing Quarries to maximise uptime
“The CDE SmartTech system will benefit quarries in Victoria, with some existing CMPA Members looking to go live with it in the coming months. It really suits small/medium sized quarries as it gives them great operational insights and it has safety and maintenance checks embedded without them having to go and buy, build or subscribe to a big software package, it is all built in to the plant and supported by us, the OEM.”
CDE, a leader in wet processing solutions, has commissioned a 200tph sand wash plant for Walker Quarries Pty Ltd which embraces the very latest in digital technology. Walker Quarries Pty Ltd makes aggregates and manufactured sand from its greenfield site near Wallerawang in New South Wales.
Problem
One of the big issues for the site was water scarcity and space available for settling ponds. Settling ponds used to recycle water can often encounter significant operational and logistical challenges as well as the possibility of highvalue fines becoming lost and trapped.
As such, maximising water recovery which became an integral part of the design, as well as increasing plant capacity to boost productivity. Sensors on the plant continuously stream real-time, in-depth performance data and insights on the plant’s health, accessible 24/7, from anywhere in the world.
Solution
The 200tph plant comprises of CDE’s M-Series M4500 modular wash plant, an AggMax TM scrubbing and classification system, an AquaCycle TM high rate thickener, and a filter press sludge dewatering system.
CDE’s M-Series M4500 modular wash plant integrates feeding, screening, washing and stockpiling on a single chassis with ability to deliver consistently graded products.
The EvoWash sand wash plant built into the M4500 includes an Infinity Detwatering screen which distributes power evenly across the full screening area to ensure maximum transfer of energy to material for unrivalled dewatering performance, and is complemented by the AggMax which combines scrubbing, organics removal, sizing, stockpiling, fines recovery and filtrates removal on a compact chassis.
The AquaCycle is a high-rate thickener, recycling up to 90% of the process water for immediate re-use in the system, assisting Walker Quarries to maximise water recovery and eliminate settling ponds.
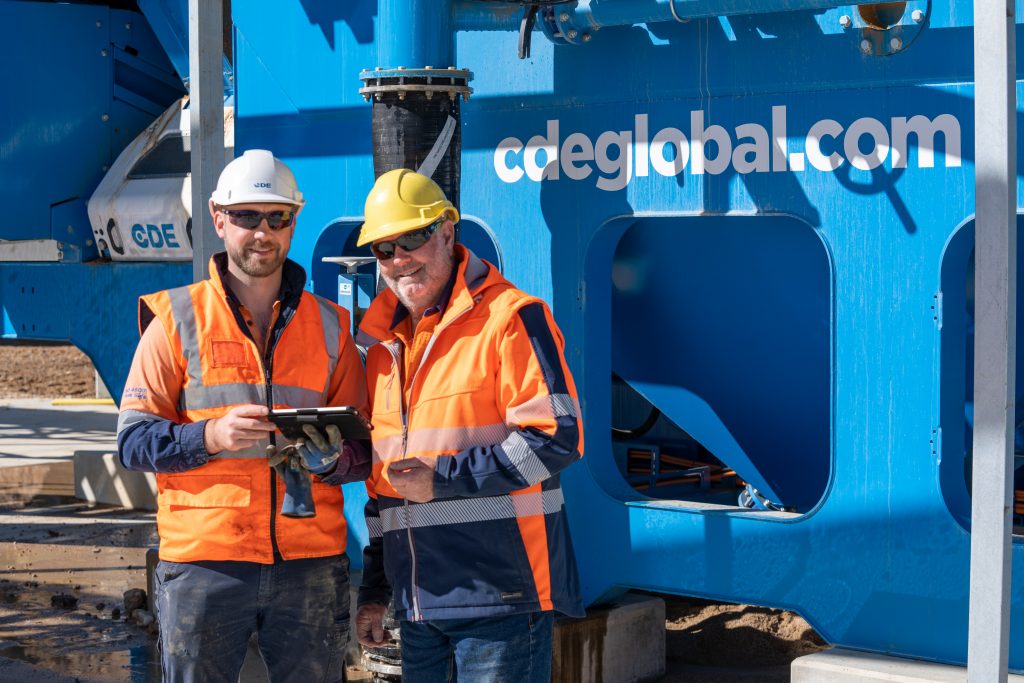
The final stage in the water recovery and tailings management system is a Overhead Beam Filter Press. Significant amounts of testing went into selecting the press installed and it has performed flawlessly and contributed to further reducing the plants water consumption and also making a dry filter cake which in itself is now a sellable byproduct.
CDE’s SmartTech plant management app, enables the firm to understand their plants performance, as well as allowing the team to make informed decisions to increase productivity, improve operational efficiency and maximse up-time. Through the app, you can also schedule maintenance and easily order parts.
Result
With CDEs technology, Walker Quarries is producing two sands; 0-3mm and 3-5mm, as well as six aggregate products; 5-8mm, 8-75mm, 10-14mm, 14 20mm, 20-75m and +75mm oversize, to be used in the local construction industry.
Walker Quarries is now able to produce two sands simultaneously and seamlessly with no need to switch out screens, resulting in increased uptime.
Wayne Chapman, Quarry Manager for Walker Quarries commented: “We’re delighted with the success of the entire project, from the initial discussions, right through to the installation and aftersales care, the entire team at CDE has included us every step of the way and completely exceeded our expectations.
“The benefits of the increased productivity and outputs are already evident in our operation, and we really look forward to seeing where this partnership can take us.”
By analysing data from the plant, our experienced engineers identify trends that enable CDE CustomCare and our customers to provide proactive maintenance and optimise the plant, maximising productivity, and plant availability. Through the app, customers can create and assign checklists, record repairs, share photographs, log issues, and generate reports. This ensures maintenance is carried out in the right way and at the right time.
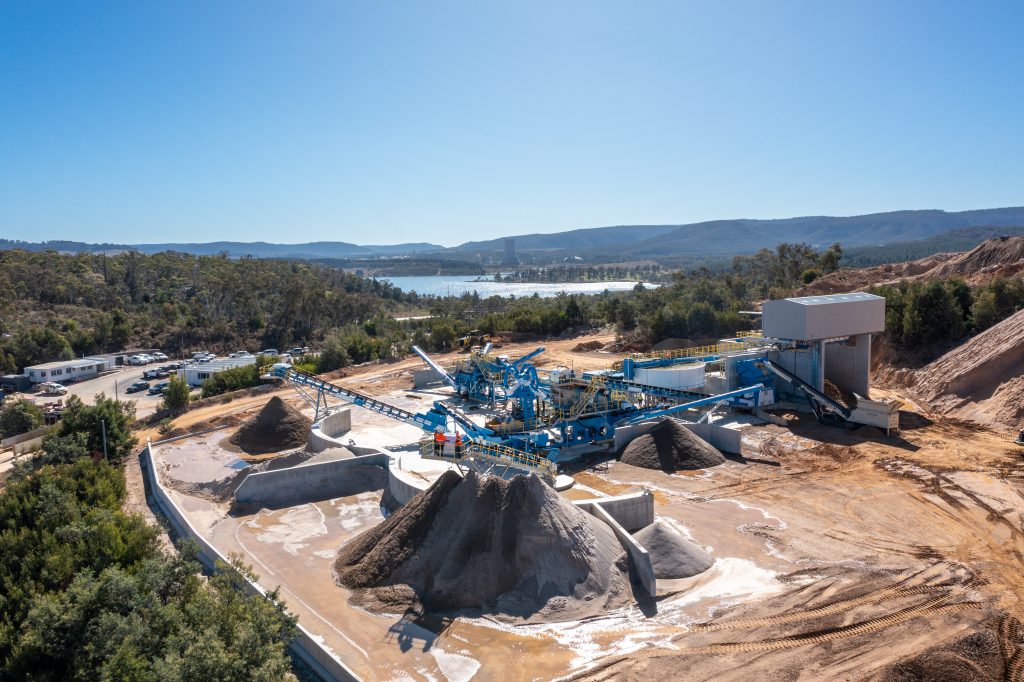
Daniel Webber, CDE’s General Manager for Australasia, said: “We believe we’ve succeeded in achieving one of the firm’s main goals in maximising water retention with our technology and CDE SmartTech. This project has been a huge success, and one that we’re very proud of as a pioneer in the industry.”
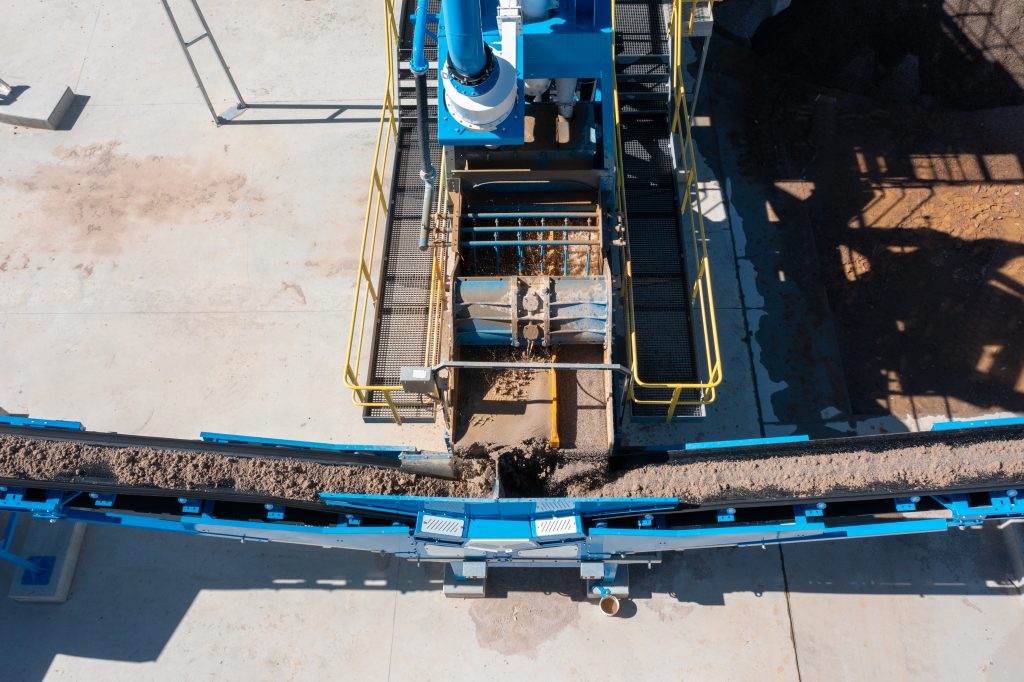
CDE has been an active associate member of the CMPA since 2017. From then, the company has had a transformational impact in the region delivering a significant number of small to large-scale projects across Australia and state of Vistoria. CDE joined the CMPA to forge closer relationships within the local market and to champion more efficient and
sustainable practices with cutting edge technologies.
With common values grounded in innovation, excellence and sustainability, CDE are regular contributors on topics such as challenges facing the market, materials processing innovations and future opportunities within the sectors of sand and gravel, tailings, water management and waste recycling.
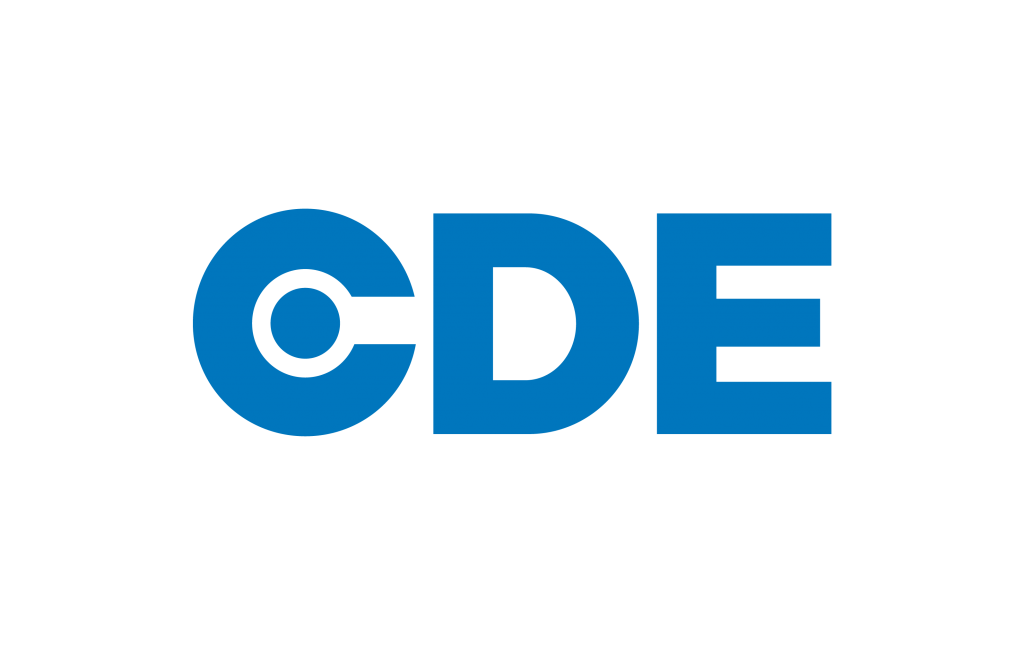
You must be logged in to post a comment Login