Conduct Blending Plant Operations
SEAN KINDER, Document Development Officer for the CMPA reports on the next Reference Manual – Conduct Blending Plant Operations.
THE newest addition to the CMPA library currently in development is the Conduct Blending Plant Operations reference manual. This new book elaborates and applies the concepts studied. Over the past few months many suppliers, quarry personal and educators have been contacted on the subject of blending and development of the manual and the course is now almost complete.
Blending is a very broad process and each site has its own technique, however, generally each plant contains a pugmill, chutes, feeders and conveyors as a means of handling materials, variations of storage bins, hoppers and silos and a collection of monitoring devices including software, moisture monitors and belt-weighers.
Generally the blending process may include: the addition of water to crushed rock, recombining split aggregate and water to crushed rock, cement treat and reconfiguration of the product to suit customer needs.
The Conduct Blending reference manual aims to give new users or employees a broad and generic understanding of how to operate the plant.
Throughout blending and batching plants on a quarry site, various hazards associated with moving parts (conveyors and pugmill), electrical circuitry (resulting in fires or electrocution) and slips, trips and falls, have been identified.
Confined spaces and working at heights should also be considered when accessing the pugmill and any storage spaces. Techniques on how to identify these hazards and measures of control are detailed in the Work Safely reference manual.
Capital equipment is discussed at length, with inclusions of maintenance, basic problem troubleshooting and tips on getting maximum possible usage.
These days, little mixing is done by loader. This process is more commonly achieved with use of bins, feeders as well as a pugmill.
With a scarcity of time and the need for more consistent, precise and accurate ratios; pugmills evenly add materials, stops segregation and provides thorough mixing.
Conveyors are the most frequently used method of transporting material throughout the blending plant. Several different types of conveyors have been researched as well as the generic rubber belting including: pneumatic conveyors, eliminating the use of conveyor rollers, pumping air to the underside of the conveyor belt, allowing it to slide over a smooth surface and screw conveyors and feeders.
These are used in transporting materials which ‘may be negatively affected’ if exposed to elements (cement), by being sealed within a cylinder and being moved via a spiral blade surrounding a shaft.
According to John Rist (Conundrum Holdings), ‘rotary valves, containing a variable speed drive, may be installed underneath the cement silo and used to control the feed rate of cement into the aggregate’.
Developments in technology have brought a range of monitoring devices used to aid the operators of the blending plant, the most commonly used are belt scales, which measure material flow rates and total weight, ensuring correct proportions are sent to the pugmill.
Various moisture monitoring devices, ‘using microwaves and aids in quality control, minimising the need for sample collection and laboratory tests’, mentioned by Trevor Powell of Ultra Dynamics, are now being implemented.
Terry Hickey and Brenden DeGraaff (Gordyn & Palmer Pty Ltd) explain that ‘expansions in automation, with a combination of belt weighers and probes, now allow quarries to remotely program their blending plants (consistently adjusting percentages of different aggregate size, moisture content and cement additives) and determining where it should be discharged. This is achieved by calculating the asset’s position with the variables of belt speed, length and time’.
Systems now provide comprehensive reporting which includes materials usages, total production tonnages and downtime’s. The system can also be supplied with a web interface for alarming diagnostics and reporting from smartphone, tablet or PC.
Setup, start-up and operating procedures of the blending plant are variable from site to site. Some factors which affect these may include degree of automation in the plant, age of machinery and production requirements. However there are some important things which should be checked regardless of these factors. Among enquiries of several people, checklists of Boral, Northern Quarries and Scope Engineering Services Pty Ltd have been collaborated and combined and the following is consistent throughout.
The pugmill should be inspected before and cleaned after use, as material may harden over time and become more difficult to remove. This also may decrease life of capital equipment and wear components.
It is essential that the operator check for blockages, areas of spillage, that water spray nozzles are functioning and anything else which may impair productivity. For safety purposes inspections must be done of the overall plant and guarding. This includes structural supports of the bins, hoppers and silos, searches for potential foreign material which could contaminate the asset and undermine the foundations.
Oil levels, gearboxes and generators should be regularly checked, to make sure they are correctly functioning and free of leaks. Wear components like paddle tips and bin liners should be inspected for damage and functionality assessed before operation. Once site and plant checks have been completed, the operator can proceed with setting belt speeds and water requirements for the desired ratio.
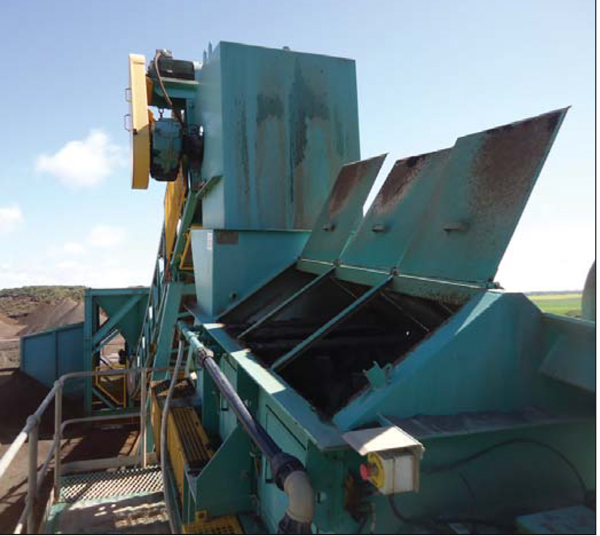
At the conclusion of the shift or when the blending plant is no longer being used, a similar procedure as the setup/start-up should be undertaken as any damage may be noted and fixed accordingly.
Samples of inspection and checklists are available to be modeled in the reference manual. Not only does this manual develop equipment knowledge of blending, it also shows methods to increase overall plant and quarry production and efficiency. The procedures and checklists mentioned above were developed to reduce start and downtime’s.
For example, if the pugmill is clean and free of any material from the previous days’ use, there will be ‘reduced chances of contamination and an increase in overall production’, according to Ryan Eldridge (DE Quarry Solutions).
Throughout operation, it is essential for good communication be exercised, as this optimises plant productivity. A broad description of this occurs between the bin-sales loader, laboratory and blending plant operators.
- Bin-Sales loader operator supplying required quantity and quality material to blending plant via bins, pits, bunkers, hoppers etc.
- Laboratory communicating with blending plant to outline the required material that is to be produced and to the required specifications.
- Loader driver communicating with blending plant as to the material that is to be distributed to customer.
- Laboratory testing the material to ensure that adjustments are made to ensure quality is maintained and within specifications of the customer.
Customer requirements will affect the way the blending plant is set. The blending plant will need to be set to suit these requirements to ensure the material is workable and meets industry standards and cost effective pricing. VicRoads broadly defines crushed rock classes on their website (Class 1 through Class 4).
The final product is either conveyed into bins ready for dispatch or
into stockpile. Over time, possible segregation may occur according to Ryan Eldridge, which means the rock sizes separate within the stockpile. There are various ways of reducing segregation including: using luffing conveyors and radial stackers, reducing the discharge fall height, having good quality product – ensuring correct product ratios, grades, moisture content and bindings are added, and that ‘the loader continuously turns the load corners’.
Contamination of the product may result in a poor quality product being received by the customer. Impacts of this occurring may result in possibilities of contractors asking for a discounted price or returning the product for re-processing at the quarry’s expense.
Contamination occurs if foreign material is detected within the final product including oversized material and excess water. To reduce the risk of this event occurring, it is essential that the bucket of the loader, truck carting material and storage areas be free of any impurities (including dirt, clay, mud and other sized aggregate) before use and that moisture levels are monitored regularly, especially in extreme weather conditions. NATA accredited testing and visual inspections must be completed regularly on samples in these environments.
Conduct Blending courses and reference manuals are a part of the extractive industries training packages, with topics including conduct crushing, conveying and screening. Following this will be development on training material of Conduct Sand Plant Operations and the servicing of crushers, screens, conveyors, bins and hoppers.
To obtain an order form to purchase the Conduct Blending Manual or any other CMPA Publications contact the Secretariat on 03 5781 0655 or at [email protected]
You must be logged in to post a comment Login