DMM Engineering
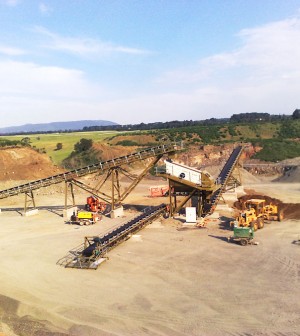
BRENDAN PYLE and GERARD VERMAZEN of DMM Engineering report on the growth of the business and its commitment to continuous improvement.
DMM Engineering has been operating since 1987, providing the sand and quarrying industries with a range of capabilities including, design, fabrication, machining and engineering maintenance services.
Gerard Vermazen, the founding Director has been with the company since its inception and has built the DMM Engineering business around a reputation of providing quality, cost effective services to all customers. Brendan Pyle joined the business as a Director and co-owner in 2012, to support the future growth and capabilities of the business.
On site robotic welding and line boring has become a key competency and the team at DMM Engineering have successfully performed this work throughout Australia, on a wide variety of both fixed equipment and mobile plant.
Services include the complete overhaul of large items of plant and machinery involving safety, engineering, mechanical, structural, hydraulic and cosmetic aspects of refurbishment.
The sand and quarry industry’s engineering and maintenance requirements range from simple pump repairs through to in-situ maintenance of a complete operating plant. DMM Engineering supports these field based projects with a full range of workshop based equipment and technical expertise.
The team’s technical and industry expertise is supported by specialised contract engineering skills, where required, which enables onsite assessments of:
- Crusher overhaul scoping and planning;
- Site fabrication and commissioning requirements;
- Brown field and green field site development assessments; and
- CAD based drafting of existing plant.
Their mobile team and equipment capabilities enable:
- Shutdown and site fabrication work;
- Full mobile welding of plant and equipment;
- Plant relocation and re-commissioning;
- Line boring;
- Milling;
- Flange facing;
- Key way cutting;
- Journal lathe;
- Rotary welding;
- Drilling and tapping; and
- Stud removal.
The team at DMM Engineering excels at the challenges of in-situ machining and has developed a wide range of innovative customer solutions in many facets of complex machining. They have developed the expertise to complete these tasks on-site because they clearly understand what down time means to customers and industry. This ability to work on heavy equipment while it is still in the fi eld, for example at the mine operating slope, delivers massive savings to operators by greatly reducing the down time of their equipment and their work force.
Solutions are often developed and pre-tested off site to minimise interruption to customers’ operations. DMM Engineering get trusted with the hard jobs.
With their commitment to continuous improvement DMM Engineering challenge themselves to seek innovative or better ways to solve a problem, be that in a cost, performance or time saving manner.
DMM Engineering’s unmatched expertise provides the complete balance of project deliverables. Supporting risk and safety assessment through to a customer satisfaction guarantee of treating root causes and not symptoms, meeting a client deadline and not leaving the site until the installation or serviced equipment is proven.
DMM Engineering are CMPA Associate Members, are an active participant in the industry and we want to support and learn from other Member businesses.
DMM Engineering’s commitment is “What we promise . . . is delivered.”
Customer Challenge:
The challenge was to safely decommission, dis-assemble and transport an existing plant from SA to Victoria.
Prior to re-installation, the plant had to be modifi ed and additional capabilities needed to be designed and fabricated in the DMM Engineering workshop in Gippsland. The plant then had to be erected and commissioned in the Macedon area.
DMM Engineering Innovative Solution:
Prior to plant decommissioning, detailed drafting of the plant layout was completed which enabled the proposed new modifications to be designed and fabricated.
Major transportation challenges had to be overcome with innovative approaches used to disassemble and pack, to enable cost effective relocation, which was key to the project’s viability.
The pre-planning and detailed scheduling of the complex tasks minimised plant downtime, another key factor in the viability of the relocation project.
Service Delivered:
The project management of the task involved 5 man-weeks of pre-planning by Gerard prior to scope of work commencing. The on-site team of eight staff worked 12 hour shifts over six weeks to complete the project.
Customer testimonial:
“The plant relocation, capability enhancement and commissioning of the revamped equipment was completed safely, on time, to budget and was managed by a single point of contact, DMM Engineering . . . what was promised . . . was delivered.”
You must be logged in to post a comment Login