Don’t Get Lost in the Fog – The Importance of Dust Containment
Tracey Wall (née Kinder) Communications Support Officer for Kinder Australia
Dust is a by-product for almost all quarrying and dry bulk material processing industries. Where there is disturbance there is dust – and given that the industry is focused on movement of material there are sure to be particles propelled into the surrounding environment if action is not taken to prevent it.
The consequences of poor containment of dust can be detrimental on every level – Whether it be risk to personal safety, the environment, and to the conveyor equipment itself. On top of this being a morality issue, there is a direct blow to the financial bottom-line as well.
They say that “money talks” so given that there can be legal ramifications for failure to keep workers safe on the site, it is in the employer’s best interest financially to keep dust at bay. A recent government announcement of health and safety legislation that ends employers’ ability to take out insurance against workers’ lung-injury can mean big penalties for sites that do not comply with sufficient dust reduction/containment.
Increasing the longevity of conveyor equipment and lessening of production downtime remains high priority when it comes to site KPIs.
The accumulation of dust and its build-up to machinery can result in clogs, jams, corrosion, and burial of important operating components. The resulting cost can be staggering – part replacement, hours sunk in maintenance, and site shutdown.
In order to supress dust – informed choices have to be made.
Let’s clear the air.
A common method is to install a Fogging System whereby water is expelled via a network of hoses and nozzles, binding to the dust particles to form a clump, sinking the material back down to join the flow. Whilst “cheap n cheerful” it can be seen as more of a band-aid approach, and not necessarily reliable. There is a risk of over-saturation of product which may tamper with material specification. Screens may experience blinding from dense/sticky material, and flow issues such as chute hang-up can occur. Once again, we see conveyor component longevity in jeopardy and those clean-up and downtime costs stacking up.
Identifying the areas where dust is most likely to escape is the key to understanding how to contain it. High impact load zones and poorly designed transfer points are notorious for the billowing of excessive airborne dust.
The Essential Air Seal has been developed by the team of field application engineers and specialists at Kinder Australia who were visiting dust affected sites and noticing the same productivity issues arise time and time again. With 35+ years’ experience in the industry they are no strangers to dust and the problems that occur from mismanagement. A complimenting collection of products was determined that together make-up the Essential Air Seal – It is a combination of innovative European technology as well as Kinder products that have been designed inhouse by engineers.
At the core of the Essential Air Seal is the AirScrape® and TailScrape – both unique to the industry. The AirScrape® acts as a side seal which suspends over the conveyor belt due to the arrangement of specialised lamellae. This, together with the movement of the material and belt result in a suction effect. Rather than contacting the conveyor belt, the ability to suspend over the top with zero contact has meant that there is no skirt friction and damage to the conveyor belt. The service life of the belt and conveyor components has been drastically extended.
Eliminating belt sag with correct support is vital to combat dust escape at transfer points. With frequent implementation of the AirScrape® it was noted that 1mm air gap is ideal for maximum suction.
Kinder’s own K-Sure® Belt Support System has been deemed best to provide consistent and stable support.
The Essential Seal’s final component is K-Containment® Seal which provides a physical polyurethane barrier and further enhances the dust seal, trapping any fine dust particles within the conveyor section.
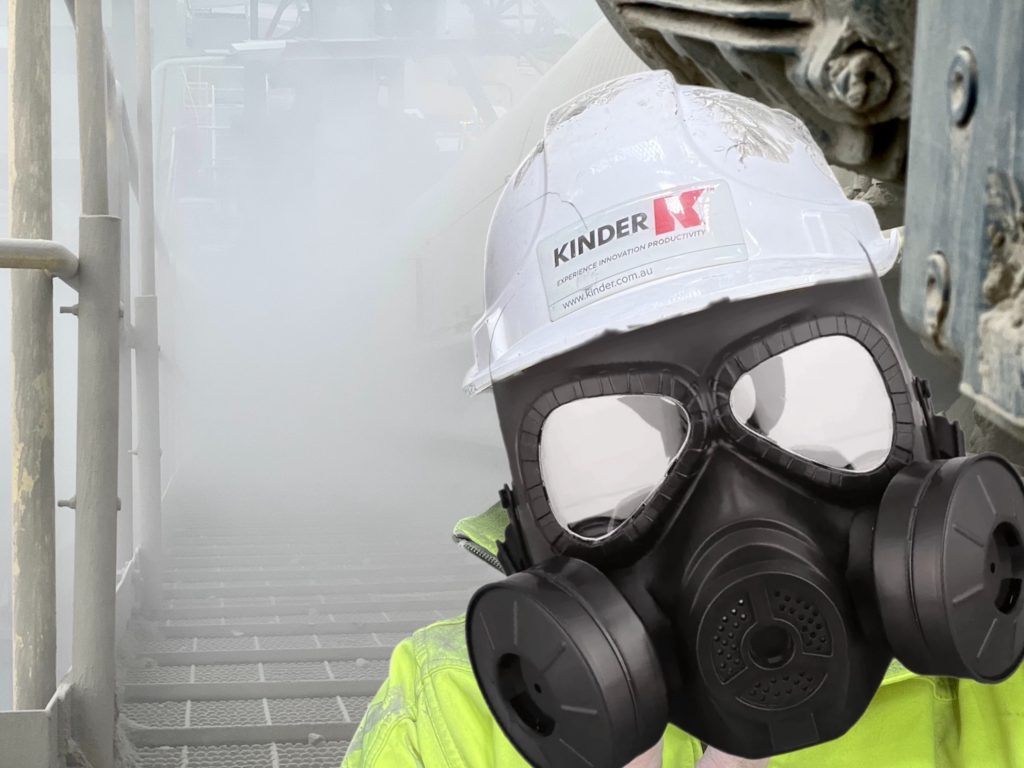
Poor control of airborne dust is a personal, environmental and financial risk – A liability that can potentially bring a site to its knees. Whether it be constant replacement of clogged up components, repeated maintenance to problem areas, productivity loss and site shutdown. In the worst-case it could be a dreaded lawsuit on your hands.
The true insurance is stopping dust at the source with a high-quality and reliable solution. Don’t get lost in the fog –
Contain the dust for a clean, productive and safe site.
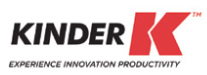
You must be logged in to post a comment Login