Dust Control Breakthrough: Flexco
Enclosed Skirting System Enhances Worker Safety and Production at Cement Plant.
Mining and processing minerals operations can generate large amounts of dust as it is processed into a marketable commodity, potentially exposing workers to elevated levels of airborne dust. In particular, cement plants are notoriously known for producing high levels of dust due to the fine nature of the conveyed material. Inhalation of cement dust is a paramount issue for operations as it leads to a variety of respiratory and cardiovascular health issues.
One of Australia’s largest producers of clinker and limestone was experiencing excess dust at their transfer chute. When the conveyed material hits the belt from the transfer chute, it causes the dust to rebound off the belt and into the atmosphere, generating significant quantities of respirable dust and spillage in the walkways that put their staff’s safety at risk when conducting tasks at the conveyor and surrounding area. The site was currently using a rubber curtain at the end of the transfer chute, but it was unable to sufficiently contain or suppress the airborne dust. As a result, to minimise safety hazards, the site was left with no choice but to barricade the area and impose no entry while in operation.
The cement plant called an authorised Flexco distributor to assess the area and recommend suitable solutions for dust and spillage containment.
The distributor and their Flexco Territory Manager assessed the area and proposed a 2.4-metre-long enclosed skirting system custom-engineered to fit the existing chute and the 800mm wide conveyor belt. The enclosed skirting system included custom wear liners to provide increased skirt liner life, dust curtains to control the airflow and keep dust levels low, and Flexco’s proprietary polyurethane skirting offering 3-4 times more wear life than rubber skirting.
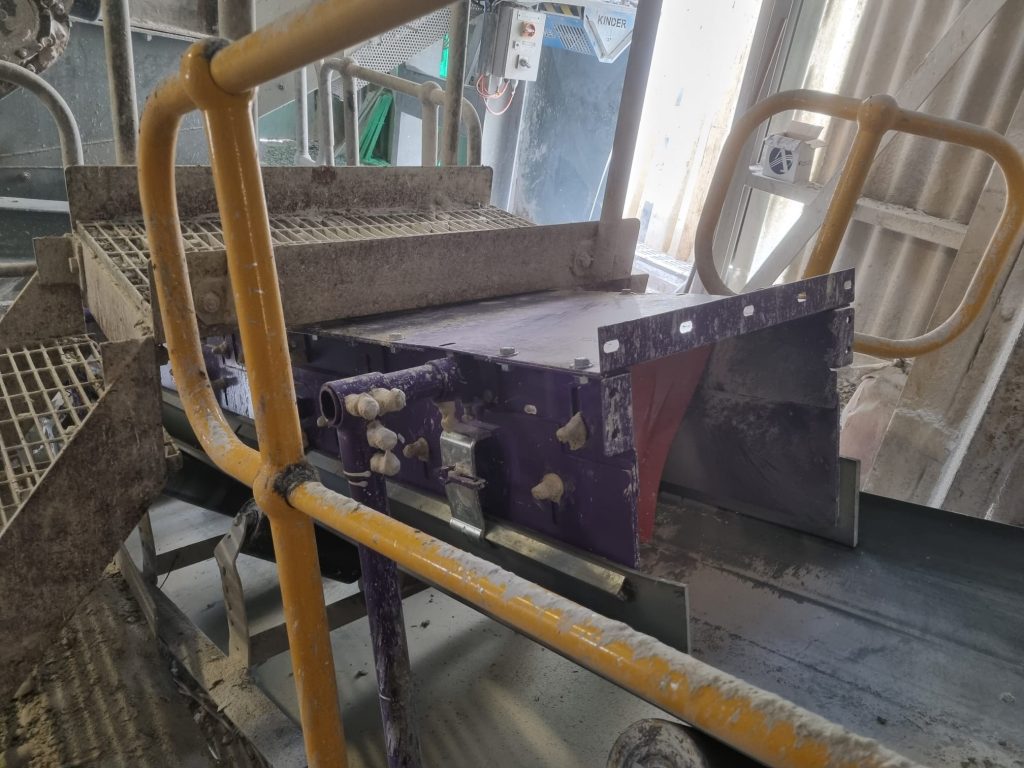
manufactured by Flexco.
The site saw an immediate reduction in dust and spillage in the walkways once the enclosed skirting system was installed. Nearly all the airborne dust has been eliminated to the extent that the area has been deemed safe for workers to enter without a dusk mask while in operation. Additionally, minimal maintenance and cleaning duties are required. Previously, the site spent $5,000 per month on external contractors and a vacuum truck to clean the area. This process would not only cost the site time, labour resources and money, but it would halt production for 25 hours per month. This meant the site was losing $60,000 on external maintenance costs and 300 hours of lost production per year.
Flexco’s custom enclosed skirting system has eliminated these costs for the operation, with no maintenance or clean-up required since it has been installed 3 months ago.
With the substantial improvements in safety, maintenance requirements, and dust containment, the cement plant plans to install an additional custom-enclosed skirting system for another conveyor.
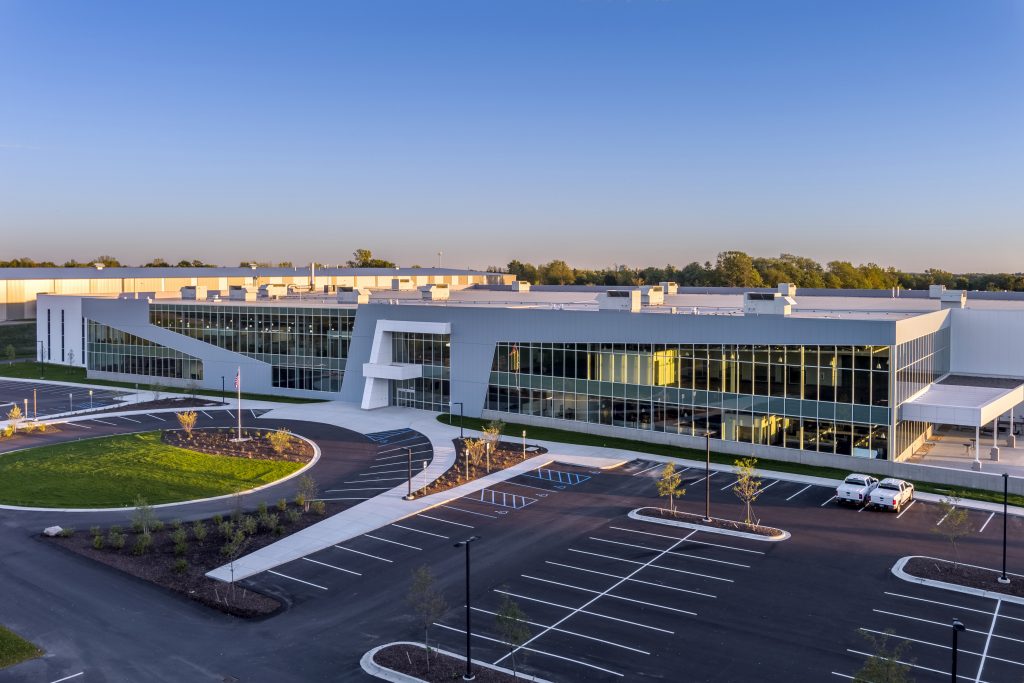
state-of-the-art HQ manufacturing facility in Walker, Michigan.
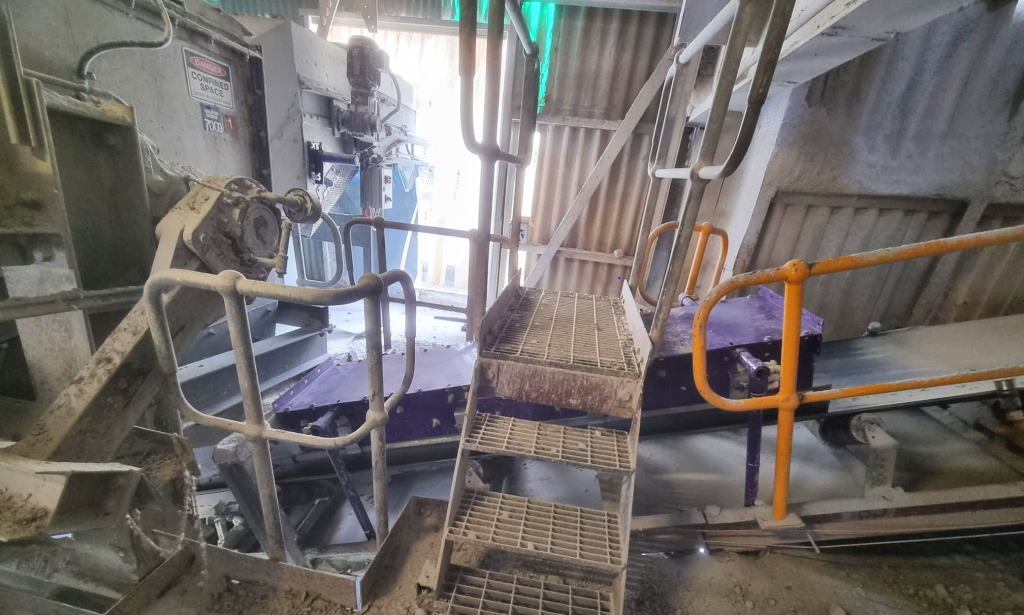
and spillage in the walkways.
Flexco is proud to partner with an industry-leading organisation that is actively representing the material processing industry. Flexco joined CMPA in 2015 to strengthen its relationships with members in Victoria’s Earth Resources industry and to better understand industry pain points.
Since 1907, Flexco has been manufacturing and designing belt conveyor components and equipment that maximise uptime, productivity, and safety. We constantly drive technology and design by partnering with industry bodies like CMPA to better understand our customer’s industries and respond to their changing needs.
If your site is experiencing similar problems or to learn more about Flexco’s dust containment solutions, contact [email protected]
or call 02 8818 2000.
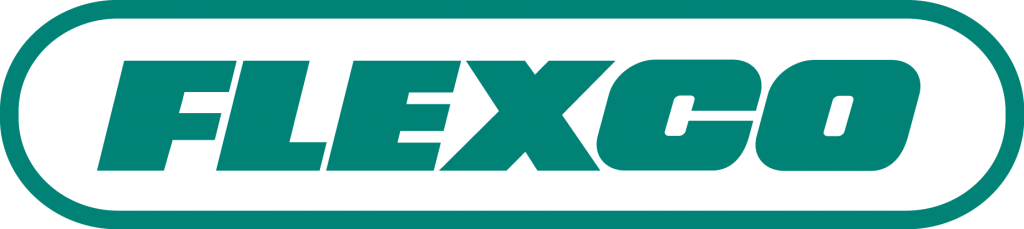
You must be logged in to post a comment Login