Dust Management Workshop 2019
CMPA Secretariat reports on the successful Dust Management workshop recently held in Tullamarine for CMPA members.
The Dust Management Workshop was held on Thursday 23 May 2019 at the Quality Hotel Melbourne Airport Tullamarine commencing at 9:00 am and was attended by approximately 50 people with over 840 years of experience in the industry including quarry owners, associate suppliers, workforce members and regulators. Many thanks to our sponsor Sandvik Mining and Construction Australia who provided a very informative presentation on solutions to handling dust including controls, suppressions and extraction systems.
This extremely important workshop was held to assist members with their responsibilities when it comes to dust (including respirable crystalline silica) and to update the CMPA Dust Management Guideline in line with any proposed changes to legislation including Workplace Exposure Standards; and to incorporate a dust management plan template.
Ron Kerr, CMPA Honorary CEO provided an introduction to dust and a history behind CMPA’s involvement on this issue (see “From the Secretariat – Issue 105”).
David McKelvie from Safemix went through the current CMPA Dust Management Guideline with a focus on providing an understanding of:
- Community Perceptions of Quarry Dust at present providing examples of what is happening in other industries and what is being portrayed in the media
- Sources of Dust Generation in your Workplace arise from surface soil and is generated through the drilling, blasting and crushing of hard rock
- Hazards and Health Effects associated with Dust and Silica Dust include irritation, dermatitis, bronchitis, scleroderma and silicosis
- Measurement of Dust Concentrations with the current workplace exposure standard for RCSD being 0.1mg/m3 and being able to accurately monitor dust to the proposed new exposure standard
- Controlling Dust in alignment with the Hierarchy of Controls including the use of PPE as your last line of defense and an ongoing health surveillance regime including periodical medical examinations
- Use of the CMPA Dust Control Self-Assessment Checklist as the basis of their Workplace Dust Management Plan
The presentation concluded leaving the attendees and industry to consider two questions:
If SafeWork Australia (SWA) set a new exposure standard of 0.02mg/m3 will the extractive industry be able to control dust levels to meet that exposure standard?
If WorkSafe Victoria adopt the proposed exposure standard and PPE is required to meet the standard, what evidence will WorkSafe Victoria require from individual quarry operators to prove they have reduced the risk so far as is reasonably practicable?
Crystalline Silica: Health Effects, Controls and Regulations,
presented by Perdita Dickson, Senior Occupational Hygienist and Michael (Harry) Terry, Earth Resources Inspector for Worksafe Victoria.
The following is a summary of the presentation from Perdita Dickson.
Legislation
Duties under the OHS Act 2004:
- Absence of risk associated with use of substance Section 21(2)(b);
- Information, instruction and training to employees Section 21(2)(e);
- Monitor conditions at the workplace Section 22(1)(b);
- Duties of manufacturers Section 30 – carry out testing and examination as may be necessary (b)
Respirable Crystalline silica:
- Hazardous substance regulated under Hazardous Substances Part (4.1) of the OHS Regulations 2017
Hazardous Substances Regulations
- Eliminate/reduce risk as far as reasonably practicable – hierarchy of controls
- Ensure the Australian Exposure Standard (0.1 mg/m3 over an eight-hour period) is not exceeded. (WorkSafe Victoria recommends that employees are not exposed to levels above 0.05 mg/m3 as a TWA.)
- Health monitoring
- Exposure to silica (without considering any respiratory protection worn) is such that there is a reasonable likelihood of adverse health effects under the particular conditions of work. Note: there was some concern held by industry that this statement undermines the use of PPE.
- Air monitoring –undertaken by competent person (occupational hygienist)
- If there is uncertainty whether the exposure standard is or may be exceeded or
- Is required to determine if there is a risk to health.
Controls
Know what you’re exposed to:
- Understand what level of crystalline silica your material has in it;
- What tasks produce dust;
- Air monitoring –if uncertain.
Control at the source:
- Enclose areas where dust is made and extract;
- Extract dust produced:
- Keep material wet;
- Isolate the person from the dust;
- Positive pressure within all cabins (operator and machinery);
- Filtered air entering cabins;
- Ensure windows and doors can’t be opened during use (ventilation systems must be well maintained);
- Maintenance on cabins (doors) Surfaces easy to wipe down;
- Boot cleaning or under floor extraction.
Clean up:
- Do no dry sweep;
- Do not blow down with compressed air;
- Use a portable HEPA filtered (Dust Class H) vacuum cleaner;
- Clean clothing with Dust Class H vacuum cleaner or ‘de-dusting booth’;
- Launder/disposable clothing –talk to laundering company first;
Respirators:
- Lowest control option:
- Right respirator for exposure level, tasks performed and your face;
- Training, maintenance and storage;
- Clean shaven;
- Fit testing – quantitative and qualitative.
Health monitoring
Health assessments should be conducted regularly, and by registered medical practitioners with experience in provision in occupational health services.
Further information can be found at; www.worksafe.vic.gov.au/crystalline-silica-health-assessments
Addressing Dust in Work Plans, Protocol for Environmental Management and Compliance and Enforcement, presented by Namiko Ranasinghe, Senior Environmental Scientist and Gerard Lynch, Inspector for Metro Regulatory Compliance for ERR.
Addressing Dust in Work Plans and Work Plan Variations
- Project design to address risks (can save money and avoid inconveniences)
- Objective for the risk – to eliminate or minimise, as far as reasonably practicable
- Compliance standards
- EPA Protocol for Environmental Management – Mining and Extractive Industries
- SEPP AQM – State Environment Protection Policy Air Quality Management
- EPA Guideline – Recommended Separation Distances for Industrial Residential Air Emissions
- Acceptance criteria – no nuisance, meeting standards
- Controls to address hazard – tabulate
- Details of controls being used
- Risk event being managed
- Performance measures (Simple, Measurable, Achievable, Relevant, Timely)
- Residual risk assessment – after the control measures have been applied
- Monitoring – method including regularity and any applicable guidance documents
- Reporting – effectiveness of controls, to whom, how often, how reports will be used
- References – relevant industry publications, CMPA Dust Management Guideline
Compliance and Enforcement under Mineral Resources Legislation
- EPA Guidelines
- New Focus of Earth Resources Regulation
- Powers under Mineral Resources Regulation
Assessment Criteria for Mining and Extractive Industries:
Respirable crystalline silica 3µg/m3 annual average Transformation to the Environment Protection Act and Regulatory Reform Program, presented by Elissa Newman-Sutherland for EPA.
A General environmental duty (preventative duty) has been incorporated into the Environment Protection Amendment Act 2018that will come into force on 1 July 2020
“A person who is engaging in an activity that may give rise to risks of harm to human health or the environment from pollution or waste must minimise those risks, so far as reasonably practicable.”
- Modelled on the OHS Act (established in Victoria since 1985)
- Minimise means to eliminate the risks (as far as reasonably practicable) and if not, reduce the risks.
To determine what is reasonably practicable consider:
- Likelihood
- The degree of harm
- What the person knew or should have known
- The availability and suitability of ways to eliminate or reduce those risks
- Costs of eliminating or reducing those risks.
Criminal liability for a person conducting a business
Serious criminal offence – maximum of approximately $1.6 million for a company.
There will be more articles on the General Environmental Duty in future issues of Sand & Stone.
The afternoon session started with a presentation from Andrew Lewis from Ektimo on ambient dust monitoring, OH&S sampling and analysis. He touched on the health impacts of dust in quarries and then focused on Protocols for Environmental Management (PEM) and the different types of monitoring.
As well as how to review the monitoring reports received, are you monitoring for management or compliance? There are different levels of monitoring depending on the size of your site and the volume of extracted material per year. The proposed changes to the Workplace Exposure Standard for RCS will require new methods of monitoring, possible with an increase to minimum sampled volume (time) or flow rate. Not plausible currently.
Ken Minch from ESS presented on dealing with dust looking at:
- Containment (low ongoing costs) – looking at air movement, velocity and how to control it using skirt boards and sealing boxes
- Suppression (minimal ongoing costs) – using quick-fit mist sprays and foam
- Collection (highest ongoing costs) – using bag houses and point specific insertables
A practical presentation from Michael Smith of Amare Safety and Stuart Oppawski of Safety Equipment Australia looked at PPE that can be used on the quarry site. A focus was placed on breathing protection and the different types of respirators and power assisted filters and masks.
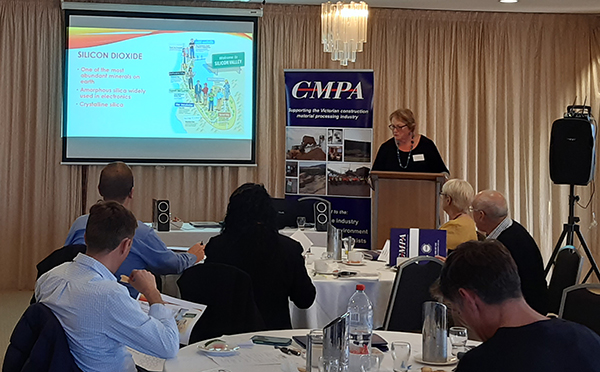
The final presentation was from Dr Amanda Sillcock an Occupational Physician at Monash University discussing Health Monitoring and Respirable Crystalline Silica.
There are three types of silicosis: acute; accelerated and chronic.
Accelerated silicosis has had a lot of publicity recently:
- Historically rare in Australia;
- Caused by inhalation of very large amounts of fine crystalline silica particles;
- Occurs with 3-10 years exposure;
- Very aggressive form of the disease;
- Associated with the increasing use of composite stone for kitchen, bathroom and laundry benchtops;
- Also found in Turkey when sandblasting jeans to give the distressed look.
Medical monitoring:
- Demographic data
- Medical history
- General
- Respiratory questionnaire
- Chest x-ray read by a qualified radiologist ILO B reader (only 17 currently in Australia)
- Baseline at start of employment
- Every 5-10 years depending on exposure
- Assessed according to current ILO criteria
- CT scan
- Diagnostic procedure
- Not currently recommended for general screening BUT
- Should be considered if working with composite stone
Further assistance from CMPA with respirable crystalline silica dust management may be found in the current CMPA Dust Management Guideline March 2016 and:
- CMPA pre employment health assessment proforma;
- CMPA periodic health assessment proforma;
- CMPA exit employment health assessment proforma;
- CMPA instructions for medical practitioners.
Note that the above documents will be amended by relevant specialists when Safe Work Australia have released their Workplace Exposure Standard review.
Thanks again to our sponsor Sandvik Mining and Construction Australia and to all presenters for their time and efforts.
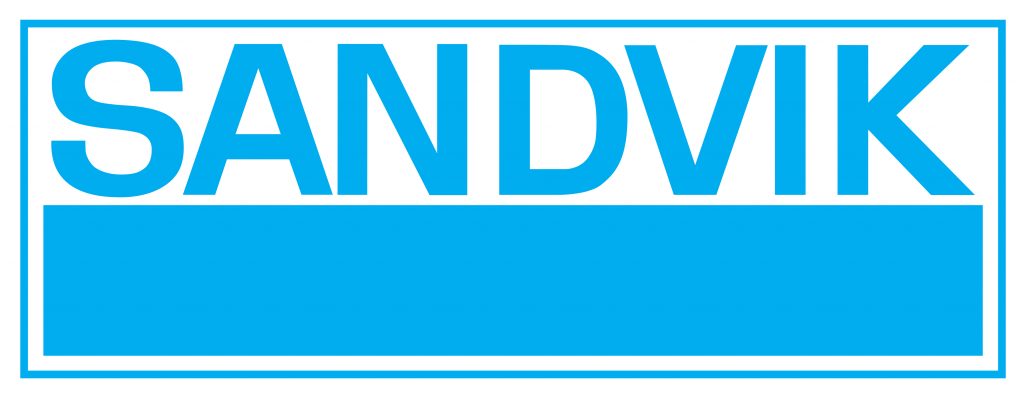
You must be logged in to post a comment Login