Energy Management – Simply Vital Going Forward
TERRY HICKEY, Managing Director of Gordyn & Palmer Pty Ltd provides a report on automated energy management.
WITH the cost of electricity ever increasing even before the carbon tax, Automated Control Systems including energy management are vital for today’s business.
Understanding complex supply contracts and their limitations are equally a demanding challenge to plant managers. However, keeping the plant “under control” ensures the plant never exceeds its contract amount and maximises the power efficiency for each stage of the process.
The right infrastructure to monitor, control and report is vital to allow managers to operate with the set knowledge of the real cost of the goods produced.
Investment in any capital must have clear evidence of payback within a reasonable time. Unfortunately many decisions on infrastructure expenditure have not always been able to be measured to show return. Monitoring power usage and automatic controlling of plant equipment is a sure way of seeing return on investment and controlling spiraling power costs.
Energy management begins at the supply retailer’s meter where, depending on the contract amount, the maximum demand is set. Exceeding the contract maximum demand will certainly mean significant increase in electricity costs for the full term of the remaining contract. Automation can ensure the contract amount is never breached and having the added benefit of reporting the real electrical costs of production.
Automated Energy Management
Crushing is the largest consumer of power in a quarry. Minimizing power consumption and improving power factor by using advanced control techniques can save significant costs.
Raw material quality is determined by its hardness, stickiness and water content. As such, quality variations can vary and the crusher, therefore, needs to be able to adapt its speed accordingly, while providing accurate crushing to ensure correct particle size.
Crusher motors are typically rated at hundreds of kilowatts, starting needs to be smooth to minimize mechanical stresses and eliminate high starting currents. All main motors including crushers and critical Key Performance Indicator (KPI) parts of plant are fitted with sensors, and the signal connected to the System to monitor, trend and control the power usage of the equipment.
The demand on electricity supply used to power the crusher and other motors will vary depending on the required particle size: the smaller the particle the more electricity is used in crushing it. Variations will also depend on mechanical setup, CSS, raw material density, clay and moisture content, etc.
Some of the methods and techniques used in advanced control:
- Automated staggered start-ups reduces peak demand on electricity supply
- Running crushers at full load maximizes throughput and makes the most efficient use of installed power (using advanced crusher feeder controls to achieve this)
- Using soft starters for minimizing mechanical and electrical stresses and power demand
- Using variable speed drives to optimize crushers speed and crushing efficiency, as well as quality of crushed rock. This technology provides better power factor and again results in energy savings.
- Using power factor correction to reduce electrical power demand and electrical power losses.
- Automatic optimised plant operation providing constant yield.
- Accurate direct loading systems minimising the need for loader movements and ensuring optimised truck utilisation.
- A power management system constantly monitors energy consumption intervals and ensures that the peak demand for that period stays under the contract demand.
Once the demand gets close to the contract amount, the system automatically reduces power demand through load shedding of non – critical plant.
Alex Fraser Clayton and Laverton sites have been utilising methods 1 -7 since 2009, whilst Hanson – Wollert have a had a power management system for over ten years. It is based on continuous real time energy readings off the meter. The system is based on a Programmable Logic Controller (PLC) interface and incorporated into the plant control system.
The system widely used in manufacturing sector can now efficiently be installed in all process plants. Today’s systems also provide full reporting and diagnostics including individual and overall performance of key equipment and can be fully supported throughout Australia.
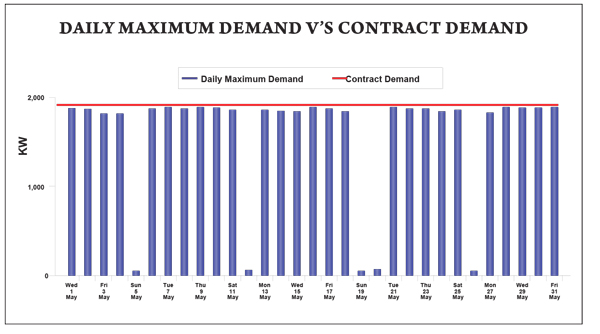
Gordyn & Palmer Pty Ltd has provided quality electrical and industrial automation to the quarry and material handling industry since 1978 and continues to lead the way in development of custom systems.
Gordyn & Palmer has been a long term associate member of the CMPA. We’re proud to be associated with this association and will continue to work closely with members to develop smarter, more productive and safer ways of doing business.
Further information contact Terry Hickey on (03)9703 2477 or www.gordynpalmer.com.au
You must be logged in to post a comment Login