IMPROVING MAINTENANCE, DECREASING DOWNTIME
Mark Pitham, Groeneveld Australia
When we talk about maintenance and the associated costs, we look for the most reliable service provider and the most opportune time to carry out that maintenance so as to minimise the effect on the bottom line of our operation, no matter which industry we are in.
So with the above in mind it is not unusual to hear of systems and processes, as well as advancements in technology, being implemented every day to ensure that items of plant within our operations continue to contribute to the bottom line and not erode it.
One of these advancements isn’t all that new but is certainly contributing to increasing many company’s bottom line results.
This is the Automatic Greasing System or (AGS).
The lubrication of moving load bearing components in our industry is a necessary function that requires regular attention to pr event component failure and ultimately loss of revenue.
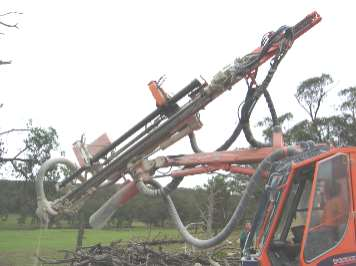
SO WHY DO WE GREASE?
Greasing is used to prevent wear and tear by, avoiding metallic contact, sealing against water and dirt, and protecting against corrosion.
WHY WOULD WE USE AGS?
Without manual interference the required quantity of grease is automatically delivered at the right interval to the required points. The machine is greased whilst it is in operation, frequently and with controlled, metered, small quantities of grease.
WHAT ARE THE ADVANTAGES OF AGS?
AGS guarantees that there is always the right quantity of fresh grease at the grease points.
Greasing during operation results in better distribution of the grease over the bearing surface and the small quantities combined with the short intervals results in optimum protection against dirt and moisture.
AGS reduces downtime, increases productivity and lowers repair and overhaul costs as well as safety and environmental hazards.
The reduction of downtime is realised through the machine being greased in operation and with fewer delays waiting for parts and repairs.
The reduction of safety hazards is realised through the elimination of the need for personnel to reach or climb to grease points in hazardous areas. AGS reduces the impact on the environment through the reduction of grease consumption and the reduction of the use of heavy metals and chlorides.
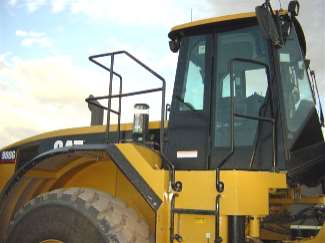
SO AGS YIELDS RESULTS IN THE FOLLOWING WAYS
Productivity gains head up the list, having front line machinery performing to maximum production outputs for longer periods of time make significant positive returns for the owner.
Longer machine life and higher residual value due to better mechanical condition and more comfort to the service department.
The operator is no longer involved in the actual daily maintenance, but more so in an inspection and reporting role, resulting in better overall planning of the maintenance schedule.
CASE STUDY: MAWSON’S QUARRIES
Recently Mawson’s Quarries purchased a new Sandvick Tamrock 800-2 drill rig for its drilling operations based in Glenrowan. With some 58 grease points in awkward locations requiring daily greasing, the decision to employ an AGS rather than requiring the operator to grease the machine was as they say, a “no brainer”.
Deploying the drill from its duties back to the safety of the compound or vehicle park and then maneuvering the boom and drill head to access all the points, presented not only down time issues, but also OH&S issues.
Mawson’s first trialed Automatic Greasing on their Cat 966G face loader operating out of Lake Boga. Roy Webb, Mawson’s Snr. General Manager for Quarries, says the issues of downtime and safety were what got Mawson’s thinking about the benefits of an automatic greasing system. Initial calculations showed they would recoup the cost of the investment over the life of the machine.
The reality was that within approximately 12 months the system had paid for itself. Automatic greasing has replaced a daily downtime of 20 minutes that equated to an annual production loss of around 10,000 tonnes!
The other aspects that now ensure that all machinery entering the Mawson fleet is fitted with automatic greasing is, not only the guarantee that the lubricant is reaching the entire bearing surface during operation resulting in better component life, but also benefits in OH and S requirements.
Roy points to experiences with their CAT 980 loader where to grease the bucket tilt ram ends, it required the operator to stand on the top of the bucket and virtually grease the points one handed whilst trying to hold on for balance with the other hand. The operator now is not placing himself or the company at risk from infringing safety regulations.
With these advantages realised, even the road transport aspect of the Mawson fleet is having automatic greasing fitted. A new Mack truck and quad dog trailer have also recently been fitted with a Groeneveld automatic greasing system.
Please call Groeneveld Australia on 1800 640 560 for further information
You must be logged in to post a comment Login