Kinder – Eraser™ Primary Belt Cleaning
Failing to clean your conveyor belts can lead to a sticky situation.
Material carryback occurs when bulk material adheres to the conveyor belt and is not completely discharged at the transfer point or the intended destination. Instead, some portion of the material sticks to the belt and is carried back along the return side of the conveyor.
The follow-on effects can lead to a variety of production inefficiencies:
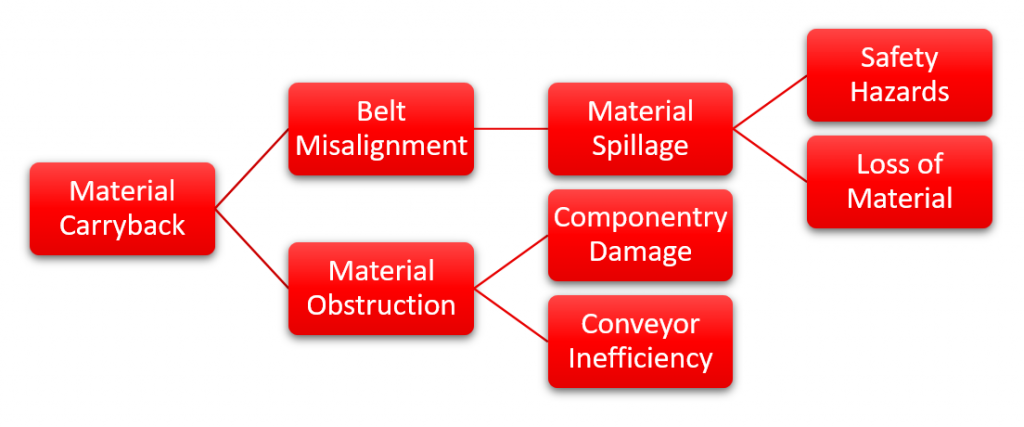
The resulting clean-up of material spillage is unproductive and costly. Sourcing the personnel to do the manual shoveling is becoming more of a difficult feat.
Kinder Australia provides the solution to effectively remove material carryback and solve these issues before they even arise.
The Eraser™ Primary Conveyor Belt Cleaner is an industrial grade primary series type conveyor belt cleaner built around an industry exclusive polyurethane tensioning system. The unique Safe Torque™ ratchet enables easy adjustment of the reliable, spring free Perma-Torque™ urethane tensioning system.
The Eraser™ is a corrosion resistant, fully sealed, dust proof tension conveyor belt cleaner mounted within a heavy-duty galvanised pipe on a sturdy steel mainframe. The quick release and durable engineered polyurethane blade is available in various hardness durometers to suit your particular primary belt cleaning application.
Key Benefits:
• The Perma-Torque™ tensioner provides uniform cleaning pressure and superior cleaning performance.
• Compact mounting footprint only protrudes 127 mm from mounting structure.
• Single pin blade attachment means quick and simple blade change out with less downtime.
• Proven effective cleaning performance with a 184 mm tall Raptor blade.
• The industry’s most rugged mainframe and blade design on a standard size system.
• No rusted springs, hoses, cables, shocks or mud packed components to deal with.
• Brightly coloured safety yellow end caps seal the Safe-Torque™ ratchet from dust & water contamination.
• A wide variety of configurations as well as complete stainless-steel systems are available.
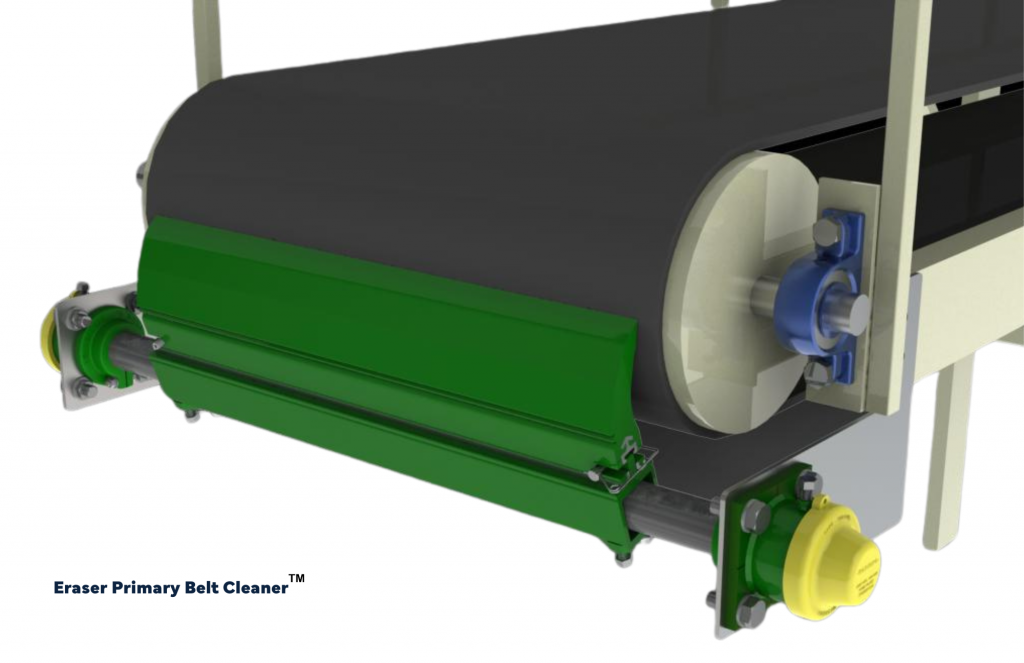
Case Study
Quarry in Victoria with a machine production capacity of 60 tonnes per hour, conveying asphalt, sand and cement.
Challenge
Ineffective belt cleaners. Elimination of material carryback issues. Excessive material spillage and cleaning up costs.
Priding itself as a family orientated company with the emphasis of safety at the heart of its operations, Kinder’s Victorian based customer for over twenty years has been at the forefront in the supply of asphalt and road base aggregate materials.
For many years, the production plant implemented a very old primary belt cleaning system. Normal wear and tear resulted in weakened tension and pressure on the conveyor belt. The uneven pressure significantly reduced the overall cleaning effectiveness of the belt cleaning system which required rectification.
Carry back and accumulation of conveyed materials on the conveyor belt return side was also a major concern as this raised issues of excessive material spillage, production downtime required to conduct manual cleaning and escalated safety hazards associated with material spillage.
Solution
Kinder Australia’s team of highly technical, field application specialists conducted a comprehensive review of the operations existing conveyor system.
The review addressed key areas of belt cleaning and included the recommendation of a solution to improve operational productivity and minimise safety hazards on site.
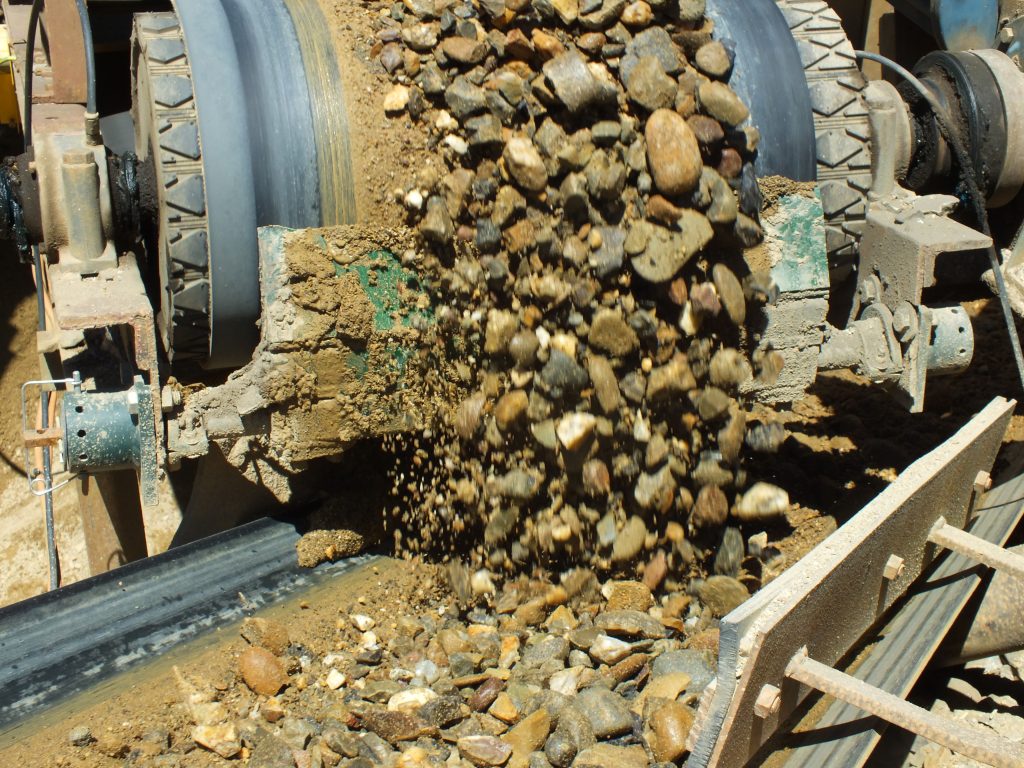
The small diameter of the head pulley was identified as a key factor in recommending Kinder Australia’s Micro Eraser™ Primary Belt Cleaning solution. Lightweight, durable and high strength, this compact primary belt system delivers a highly powerful and proven cleaning performance. The single pin blade attachment means quick and simple blade change out
with minimal production down time and no rusty bolts made the installation process timely and efficient.
Results
“Micro Eraser™ continues to deliver excellent ‘faultless’ belt cleaning performance, well beyond our expectations.”
Elimination of material spillage, clean up costs and time. Customers’ product expectations exceeded. Improved productivity and profitability.
After numerous months of constant use, Micro Eraser™ continues to deliver excellent ‘faultless’ belt cleaning performance, well beyond our expectations.
This Micro Eraser™ Primary installation successfully tackles carry back issues, which in turn has assisted in keeping belts running true, materials material spillage has also been eliminated and safety hazards are well under control.
Maintenance teams were also pleased to report blade wear on the Micro Eraser™ is virtually non-existent and no additional belt cleaner tensioning adjustments were needed since installation, further demonstrating the power, endurance and effectiveness of the mighty Micro Eraser™ Primary Belt Cleaning System.
You must be logged in to post a comment Login