LUBRICATION & ITS RELATIONSHIP TO MAINTENANCE, PRODUCTION & PROFITS
Barry Taylor, ILM Services
Lubrication and its importance to production and maintenance levels is often ignored, and in some cases even discarded.
As simple as lubrication may seem, it is actually one of the most important issues to be addressed when considering plant performance or production rates. Its effects on maintenance levels are so dramatic that it is now becoming an industry format and basis upon which maintenance routines revolve.
They are three major factors that contribute directly to the profitability level of a manufacturing or processing plant. These factors are as shown below and are in their order of importance.
Lubrication (effects maintenance)
Maintenance (effects production)
Production (effect profits)
These three factors act very similarly to a fire i.e. Fuel, Heat and Oxygen, if one of these is not an equal contributor, the fire will burn poorly. The same can be said to the level of profit/revenue a plant can produce.
The level of importance that lubrication has on plant performance is so dramatic that when large organisations construct manufacturing or processing facilities; the very first thing they develop is documented procedural routines for the lubrication requirements of that plant.
The lubrication schedules and the level of which they are developed and executed directly effects the level of maintenance required to keep the plant operational. If we discard or reduce the level of lubrication activity, the level of maintenance increases dramatically and production suffers.
Over the last 16 years of ILM’s interaction with manufacturing and processing industries, it has seen more than its fair share of poorly developed lubrication schedules resulting in abnormal and premature equipment failure. So many times we see maintenance personnel running around repairing equipment so that production can continue, without even understanding why it failed in the first place.
The systems that they are operating under have generally discarded the use of lubrication or its schedules as a preventative maintenance tool, and maintenance is often being performed under a reactive regime i.e. fix it when it fails and fix it quick. Generally this type of regime is a result of the plant owner/maintenance manager’s inability to look outside the square.
Without sounding too critical of these people, such maintenance regimes are generally a cultural issue and have developed over many years, we understand why this is; it comes from the phase “Working in your business and not on your business”.
The daily requirements of production generally override the ability for one to view things from a different angle, putting emphasis on such issues as maintenance problems and the ability to fix them quickly.
Eventually you find yourself spending more time fixing things quickly rather than driving programs that stop them from breaking down in the first place, and so the downward spiral in efficiency starts and the tail chasing begins.
DOING THINGS SMARTER SAVES $$$$$$$$
If you believe in and understand what you have just read, then it is the first step to not only improving your plants efficiency, but making your life a whole lot easier. If ILM was to make the statement that 70% of all CMPA Members (i.e. Process Operators or Plant Owners) could achieve an annual increase in production of 20%, and a dramatic decrease in maintenance costs, what would you think?
Whilst some readers by now may think ILM is being somewhat impertinent, the facts remain true, and more importantly the process to implement the most basic lubrication schedules that would dramatically effect production are much easier than you think.
DOCUMENTING REQUIREMENTS
Whilst there are many variances to a Lubrication Schedule as dictated to by the site and its environment, the first step is to document the most basic lubrication requirements and implement them into daily operations.
The lubrication schedule is a live document and is updated as plant and equipment change, or if other routines such as Oil Analysis, Vibration Analysis, Maintenance Inspection, Plant Inspections or Safety Inspection are required on a regular basis, the old saying “If you want it done correctly do it yourself,” is WRONG. We say, “If you want it done correctly, make sure it’s documented”.
The most common reason that lubrication, or in fact any activity does not get done correctly, is because it is not documented or put into a schedule. Leaving lubrication to guess work will always result in mismanagement of the activity.
WHY DOCUMENT LUBRICATION PROCEDURES?
McDonalds do not expect their staff to automatically know how to cook fries, nor do they leave the running of their business in inexperienced hands such as the 15 year old kids servicing you; they have a written hand book that explains exactly how to do things so it is done correctly every time. Just hoping that your staff perform well without documented procedures is a big gamble.
Example: To prove the point, go up to a couple of grease nipples in a high up or isolated spot on your plant, bust them off with a hammer, then ask for the plant to be lubricated. Whilst some of you may get notified that you have a couple of broken grease nipples, I can guarantee that most of you won’t, and to add insult to injury you will be led to believe that the plant was lubricated correctly. Its not that your employee is lazy or a liar, it’s more likely that you have just given him the opportunity to work that way.
Question: How many times have you asked your self “Where can I find good help”?
Answer: Good workers are created and not found; they come from a well documented system that does not require them to read the employers mind on how he wants things done.
Without bashing employees too much, as we all know most work extremely hard. The lubrication schedule not only ensures that the right product or routine is being applied to the equipment, it also monitors your employee’s activities and work ethics, something we occasionally take for granted. In extreme cases the schedule is also recognised as a legal document for employees work duties, and can be used as the basis for dismissal if not followed correctly.
ENVIRONMENTAL EFFECTS
Owing to varying environments and understanding that all sites are different, the requirements for lubrication from site to site will alter somewhat, and in some cases even vary enough to require abnormal lubrication practices of which the manufacturers of the components may not have envisaged.
Example: Loy Yang Mine in Latrobe Valley uses a very basic and inexpensive grease to lubricate the bogie wheels of their dredgers and stackers, and rarely have any failures, whilst over at Yallourn Mine (15kms as the crow fly’s) they find it necessary to use a more expensive Moly grease on the same equipment to stop failures.
As you can see, every site varies slightly and requires different attention regarding lubrication. The importance of a well documented and executed lubrication schedule as part of daily operation is as important as making sure your excavator or dump truck has fuel in it, the difference being is that your excavator will stop when it runs out of fuel, your plant on the other hand will just prematurely ware out.
Using lubrication as the format to maintenance routines will result in less maintenance costs, higher production and ultimately more profits, not to mention make your life a lot easier, guaranteed.
The documentation of the lubrication requirements of a plant is relatively simple, but with exception to product requirements as per the environment, can become quite time consuming. This is where the knowledge of lubrication, application and mechanical aptitude becomes very important, and the need to understand exactly what can be achieved through the different methods is equally essential.
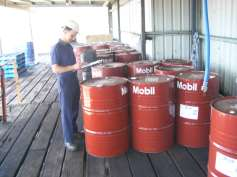
ILM’s experience and knowledge of lubrication has seen our company develop many schedules that have resulted in extraordinary improvement in production and resource allocation. Schedules for such organisations as Loy Yang Power, Yallourn Energy, Mobil Refinery, International Power, Coca Cola just to name a few, even Mathews Quarries here in Latrobe Valley are seeing the benefits of implementing the procedures.
Understanding what ILM did for large organisations, the smaller companies such as the CMPA Member, Matthews Quarries benefited from the same type of system, but on a much smaller scale. ILM offered a change to the way they were doing things. At first they believed the proposed changes wouldn’t make much difference, however after some encouragement decided to give it a go.
The first step was to perform an on site audit to collect and document the changes that would improve their plant efficiency and production. The changes included:
- Development of a lubrication schedule, documenting all lubrication points and the activities to be performed .
- Changes to the plant such as ensuring all gearboxes had breathers on them.
- Changes to the plant so that it was lubricated whilst it was running.
- Schedule to take 20 oil samples from gearboxes per month and analyse to determine oil condition for replacement or to determine component condition to catch it before a break down.
Mathews used to stop production every Wednesday for lubrication, now they no longer need to. This led to another problem, now that the plant was running all week the operators were too busy to perform the lubrication schedule. ILM’s solution was to supply a technician one day a week to perform the routine lubrication, explaining that the technician would be far quicker and more efficient that one of the Mathews employees.
By ceasing Wednesday outages, the benefit Mathews now receive culminates to a potential increase in production, including a reduction in maintenance costs of an uncalculated amount, and a lot of pressure taken off the Quarry Manager’s shoulders.
If any CMPA Members would like to discuss any of the above issues on the procedures of developing lubrication schedules, it would give me great pleasure in speaking with you. Talk is free and phone calls are cheap, but correct information is priceless.
Barry Taylor
Business Development Manager
ILM Services P/L
You must be logged in to post a comment Login