Manufacturing in Australia
ELLAINA MACKAY, National Marketing Executive for Flexco Australia, reports on manufacturing in Australia (Associate member of the CMPA since 2015).
Thirty years ago, while expanding their product line to incorporate a range of belt conveyor products to support their legendary range of mechanical belt fasteners, the board of directors at Flexco made the decision to break into the Australian market.
Flexco Australia took on the mighty task of producing Flex-Lag® Pulley Lagging and later, tungsten carbide tips, to support global Flexco operations. In 2020, we mark 26 years of Australian manufacturing.
Flexco pours polyurethane cleaner blades at its Grand Rapids, Mich. USA location, however tungsten carbide tips are better suited to the Australian market, where vulcanisation is the favoured method for joining belts.
Flexco Australia’s manufacturing facility allows quality to be closely monitored to ensure only the best product is delivered to our customers. For more than 30 years, Flexco has been purchasing the same tungsten carbide. “While there are definitely cheaper alternatives, we won’t ever compromise on the quality of our product,” says Flexco Australia Managing Director Mark Colbourn. The important thing to look for in a quality tungsten carbide product is the correct composite of carbide granules and binder metals.
“Our carbides have the optimum balance of profiling to the belt quickly, without being too aggressive on the belt and damaging the belt cover,” says Flexco Australia Quality Assurance Manager Soroosh Mirzaee when describing the quality of tungsten carbide used.
The Flexco team of engineers has conducted numerous, extensive testing – both in the lab and the out in the field – to ensure that the carbide used is the best available. Mirzaee also conducts batch spectrometric and dimensional testing of all carbides that Flexco receives into its Sydney manufacturing facility to ensure that we acquire the exact same quality of
carbide every time.
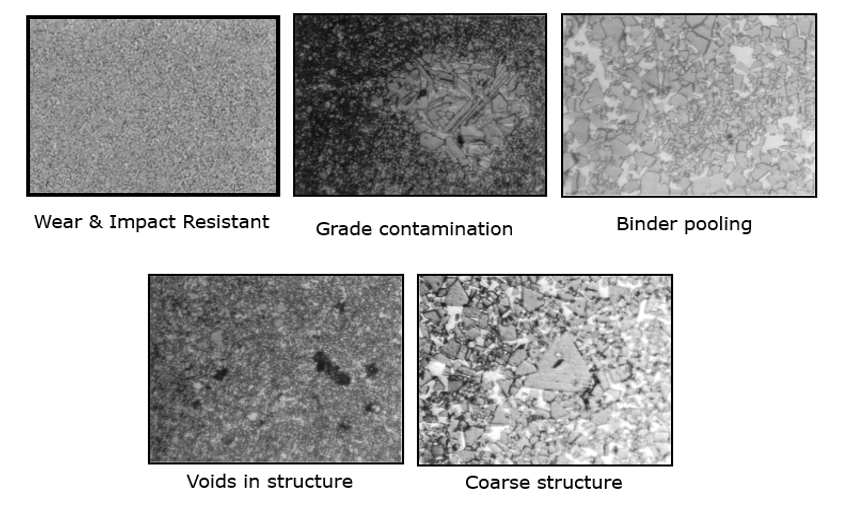
Mirzaee also regularly conducts comparative tests with other similar products in the market to ensure our carbide is consistently the best available.
The manufacturing process at our Sydney facility is also closely monitored to ensure consistency and maximum efficiency. We have developed an optimum brazing process over the years that ensures a high-quality bond between the carbide and the body, while achieving the required manufacturing tolerances.
Local manufacturing also allows Flexco to keep up with market demands and develop new products quite easily. Over the past few years, the Flexco team has researched, engineered, and manufactured a complete range of extra-life tips (15mm) and extra-extra life tips (25mm), as well as a corrosion-resistant variety for abrasive applications such as iron ore or gold.
The extra life tips were made so that Flexco could continue using the same quality grade of tungsten which quickly profiles to the belt, but also have a product which kept up with the faster belts and increased time between shutdowns that is now becoming integral to mine productivity.
“That’s why we have continued to manufacture in Australia; there are obviously cheaper options to outsource, but we believe that having the flexibility to manufacture exactly what our customer’s need for their specific environment is integral to our success as a company,” Colbourn notes. “While we know that our product is by far the best quality available in the market, we know that constant research and development is the key to staying relevant in an everchanging mining industry.”
Colbourn states that other value adding resources such as quick lead times for urgent orders such as breakdowns or emergencies is integral to the company’s success. As well as being able to react quickly to market needs and providing an unwavering quality policy backed by local manufacturing, expertise and extensive field support is what gives our customers the confidence in Flexco.
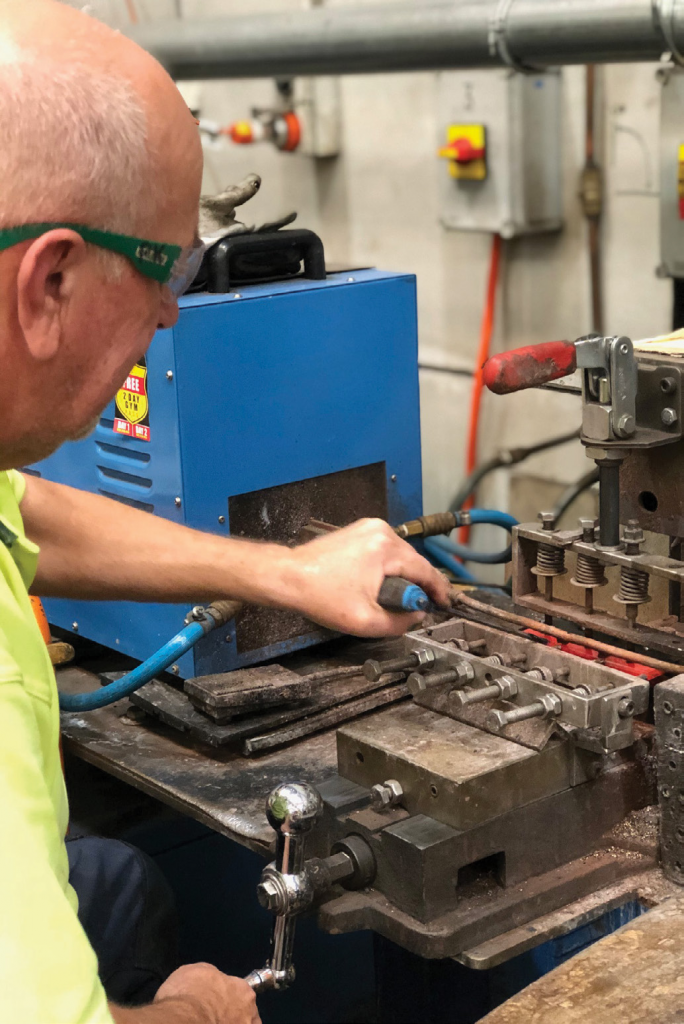
Flexco has been the originator of amazing results with recent innovations such as extra-extra life 25mm tips. Before the launch of our tungsten tip innovation – a large iron ore conglomerate was purchasing 15mm tips every 12 weeks, equating to about five sets per year, per conveyor. With the integration of the new 25mm tips, the site only needs to purchase two sets of 25mm tips per year. That is a 20% cost reduction on just one conveyor.
The site also saved the time it took to replace existing tips during shutdowns. This saves about an hour for each cleaner on the belt. With some conveyors having in excess of four cleaners, this amounts to approximately eight hours per conveyor, per year – time that can be better allocated to other productivity boosting projects on site.
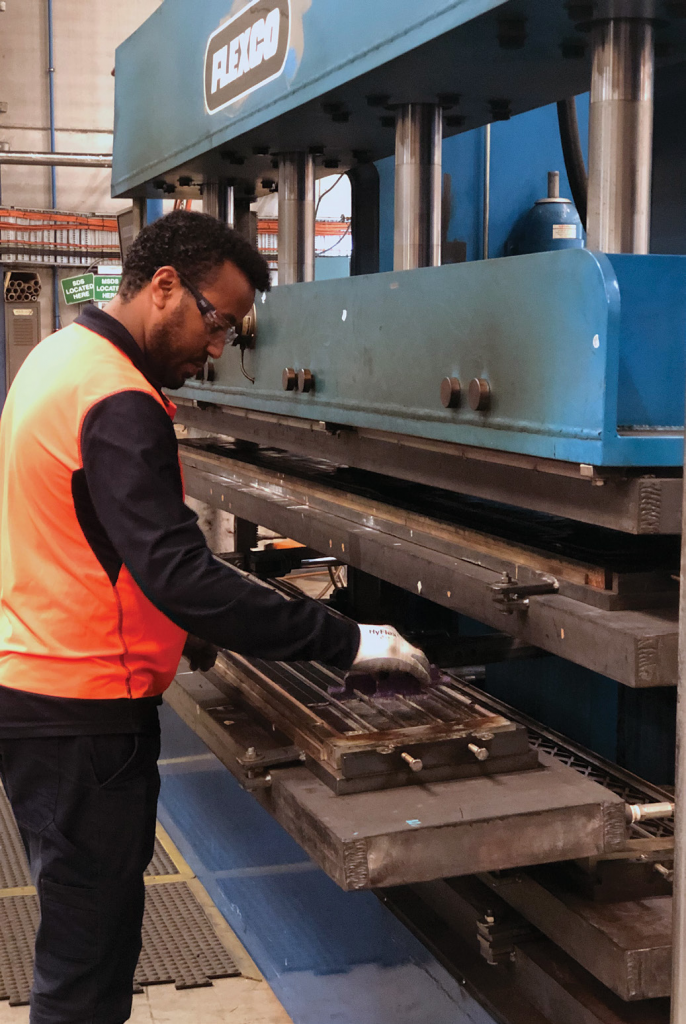
Due to the outstanding trial results – the iron ore site has specified the 25mm tungsten tips for all cleaners on conveyors as part of the 10/20 week shut down strategies.
To find out more about the Flexco range of tungsten carbide tips, contact [email protected]
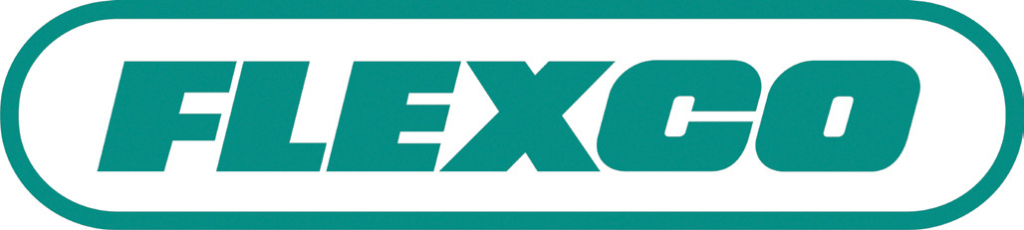
You must be logged in to post a comment Login