Monitoring Plant & Equipment’s Condition
PETER VUCINIC, from Computerised Bearing Analysis (Aust.) Pty Ltd reports in a series of articles on the various technologies used in order to determine equipment condition.
I would like to impart some of my experiences over the past 25 years in the condition monitoring field, that I hope will enable you to gain a better understanding of condition monitoring and how it can benefit plant and ultimately your businesses bottom line. I will be discussing various techniques over a number of issues that will assist you in saving hard earned dollars from disappearing into unnecessary repairs and downtime.
Everyone from management to operators should be able to comprehend the methods involved, processes and what we are trying to achieve working together. There is no need to thoroughly understand each individual method in totality.
Although this may seem like a daunting topic and that sometimes we say the “I’m too busy and don’t have time to add another check to my plants operation.” Hopefully I will be able to change your mind?
You will undoubtedly be doing condition monitoring each and every day without you even realizing that you are doing it! Not convinced? If you arrived at work today in a vehicle, and it didn’t stop on the way, or the engine didn’t self destruct on you, then you did some condition monitoring. You would have checked the fuel gauge and made sure there weren’t any red lights blinking at you on the dash. Condition monitoring done! Congratulations you have passed the entry exam to Condition Monitoring (CM)!
It is only the complexity of the CM technique that will change. Th e basic fundamentals of checking equipment to ensure it is fit for use will not alter.
WHAT IS CM?
It is used to measure the health of a machine by routine monitoring and analysis. CM uses various technologies in order to determine equipment condition, and potentially predict failure. Some of the common technologies that you’re most likely to see at your site are:
- Vibration Measurement and Analysis
- Infrared Thermography
- Oil Analysis and Tribology
- Ultrasonic’s
- Motor Current Analysis
Faults will develop within plant regardless of even the most thorough scheduled maintenance with oft en-undetected faults leading to unexpected failures. CM allows us to minimize our exposure to risk of unexpected failure and consequential downtime.
WHY DO WE NEED CM?
After we get past the obvious answer; ‘to stop things breaking down when we least expect it’, there are many more real and tangible benefits. But the biggest impact on your business will be that CM puts you in control, allowing you to be pro-active in preventing breakdowns, helping you avoid unplanned shut downs and allows you to optimize maintenance resources.
Company management will embrace CM because it allows asset effectiveness. From the company perspective, they simply need to extract maximum profits from minimum investment in plant. There is no downside to implementing CM as it is a mutually beneficial arrangement between the company and plant operations.
The other factor that has ‘crept’ its way into all fascist industry today, but more so in the extractive minerals industry is insurance. This has seen the escalation and need for sites to conduct risk assessments on plant and equipment every 2 years to establish what actions the client is taking to ensure they are limiting their exposure to any and all financial loss in relation to equipment failure and interruption to production.
How do we achieve plant operational improvement using CM technologies?
- By improving equipment reliability through the effective prediction (and then avoidance) of equipment failures
- By minimizing downtime through the integrated planning and scheduling of repairs indicated by various techniques.
- By maximizing items life by avoiding the conditions that reduce their life (eg by ensuring ongoing precision alignment, minimal lubricant contamination etc.)
EXAMPLE OF USING CM
‘How does that relate to my plant?’ I here you say. I hope to demonstrate how you can utilize many of the CM methods on your equipment to give you a tangible benefit. Humans are very basic in nature and a basic concept is ‘if it doesn’t benefit me, why on earth would I do it?’ We’ve all said it at some stage.
I hope to show the ‘benefits’ in the following example that uses two of the CM methods available to us (vibration & infrared thermography) used in conjunction to complement each other to enable us to ‘build a better picture’ of the machines true operating condition.
I chose this example to begin with, as it contains one that you are most likely more familiar with. However, you may not be familiar with my application. Evaluating and diagnosing primary jaw crushers and its bearing operating condition is a core part of my business. I’m a firm believer in using whatever I have in my ‘tool box’ to assist me in doing this. By not limiting yourself to the ‘accepted’ methods to assess machine condition, a much better ‘operating picture’ of the machine can be achieved.
How we benefit from combining techniques:
- Actual machine current operating condition certainty of diagnosis increase
- A holistic view of the machine health and a good understanding of ‘what is occurring’ are gained
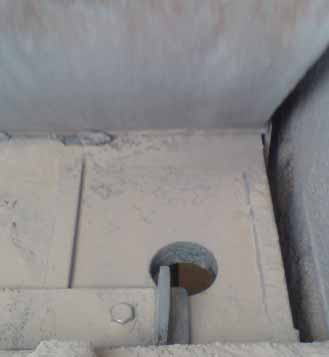
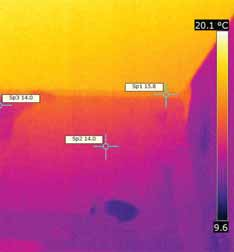
Infrared Thermography
Most people in our industry now are familiar with infrared thermography and accept this technology readily. You may already have some conducted at your site for switch boards/circuit breakers etc.
My example looks specifically at the operation of one of the key components of the primary jaw crusher and how this can be detrimental to the overall operation and long term health of the machine. This example
highlights the importance of:
- Proper toggle, swing jaw and toggle block alignment
- Ensuring toggle and toggle seats are in serviceable condition/rocking correctly
- Correct toggle spring tension/adjustment
I deliberately used infrared thermography as an easy way to ‘paint’ a picture, showing that the primary jaw was not operating as ‘smoothly’ as it should and that there was a problem in the toggle operation.
Vibration
To reinforce the initial thermal images, vibration measurements were collected on the main frame bearings to ascertain the severity problem and to gather data for future comparison etc. This issue was seen as ‘high’ energy levels on the right hand side, main frame bearing, with greater than ‘normal’ mechanical forces were being transferred to the main frame bearing.
These unnecessary higher forces, if allowed to continue for extended periods of operation, have real potential to reduce rolling element bearing life. If lack of lubrication or insufficient lubrication is added to this mix, it will undoubtedly spell disaster for the bearings.
High energy and/or unnecessary impacting forces acting on crusher main frame bearings can have detrimental physical effects such as:
- Reducing the quality of lubrication to the bearing and/or bearing components
- Artificially raise bearing temperatures through mechanical overloading
- Increase the likelihood of metal to metal contact of bearing surfaces which can lead to premature bearing failure
Pictures are universal, there is no need to have any technical knowledge to decipher a picture. Explaining vibration theory and concepts such as acceleration, impact levels and its consequences, did not seem the easiest way for me to convey the problem.
The above photographs will enable anyone in the plant to easily understand the effect of an improperly aligned, worn, maladjusted toggle and seat. With the simple concept in mind that ‘cool is good’ and ‘hot is bad’, we all naturally make the connection between heat and stress, so when you look at the photographs, I think your mind naturally and easily makes these conclusions.
As can be clearly seen, toggle and seat shows mechanical forces/pressure being exerted predominantly on the right hand side. This is represented by the ‘warmer’ orange in the infrared image.
For more information Peter Vucinic can be contacted on (03) 5441 2348.
You must be logged in to post a comment Login