Monitoring your Electricity Supply
JAMES LANGLANDS, Concrete Plant Manager from Conundrum Holdings reports on the importance of owners and quarry managers monitoring their electricity supply.
AS operators of fixed plant and equipment on various production sites, we are all aware that at some point in time the items used for processing product will involve the use of electricity – especially electric motors. Some plants rely totally on a generator on-site for power supply, others involve the use of electricity supplied by a provider from the grid and some involve a combination of both.
While it is important to monitor the electricity supply quality from a generator to avoid things like spikes and bad supply quality, those of us who use grid supplied electricity should now be thinking about monitoring a few extra things such as ‘Power Factors’ so that we are utilising the available power properly and not inadvertently breaching a contract with electricity suppliers. For users of large amounts of electricity in their production it is more cost effective to have an arrangement with a service provider called a ‘Supply Contract’ that sets out certain rules that both parties need to follow in order to have access to the wholesale electricity pool – (as opposed to paying a normal commercial power bill).
SUPPLY CONTRACT
When entering into a supply contract we need to understand that the provider will require information from us for many things, such as:
- How much maximum load the plant draws and for what periods of time it will use this?
- Where is the most power used in the system and how many electric motors contribute to this – the latter causing ‘Power Factor’ issues?
WHAT IS A ‘POWER FACTOR’?
Well in basic terms, whenever electric motors and other ‘Inductive’ loads such as welders and large scale fluorescent lighting are used they all create inductive loads on the supply system. The nature of inductive loads requires a magnetic field to operate, and thus causes a circumstance where the current in the electricity falls out-of-phase with the voltage – sometimes know as ‘Lag’. What this does is cause a situation of inefficiency within the supply system and therefore puts extra load on the supply – for example, if our power requirement by basic calculation is 500Kw and large inductive loads are present, then the electricity company may need to supply say 520KVAr to the point of supply on your site just to keep up. Th is in-efficiency is known as ‘Power Factor’ and occurs wherever there are large inductive loads present.
POWER SUPPLIERS
Suppliers of power have long batt led this issue, as it means that they have to actually supply more power to your site than is actually needed due to the power factor being inefficient – it also means that their infrastructure needs to be bigger in order to cope. An electrical system that is 100% efficient has a power factor of 1.0 (known as Unity) and a system that is say 80% efficient has a power correction factor of 0.8 and so on.
The Electrical Supply Regulations stipulate that private enterprise must maintain high power factors, around 0.9 before the supply company will seek compensation or penalties for the inefficiencies caused by your plant – they are paying to have extra power pushed up the line to you that you shouldn’t really need.
POWER FACTOR CORRECTION
Power Factor Correction (PFC) should be done on-site as close to the source as possible, by using commercially (available units from several brand names) that are connected into the electrical system that use a series of capacitors/inductors to automatically compensate for power factor inefficiencies. Specialists in electrical installations can help with assessing individual sites’ requirements.
If this is not done then companies may be left exposed to harsh penalties imposed by the supplier oft en discovered by notice of a supply contract breach.
EFFICIENT USE OF POWER
Just as importantly it also means that as consumers we are efficiently using the available power and can therefore maximise the use of plant & equipment on-site. By knowing we can efficiently use a calculated and corrected value of power supplied to us we can set real values within the supply contract that should mean we don’t fall into a situation where the agreed peak power usage is exceeded – a very costly circumstance. It also means that we have real values to use during negotiation of rates with a supplier.
In new plant design individual PFC units located at the source (motors) can ultimately reduce the associated cable size and infrastructure and thus may reduce the overall capital outlay for the project depending on the size of the application.
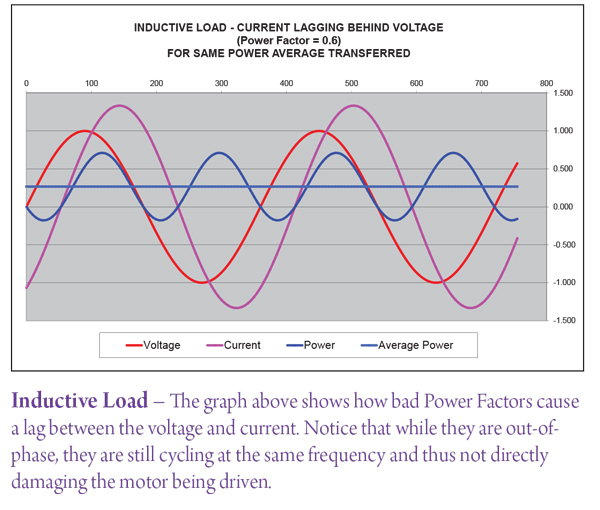
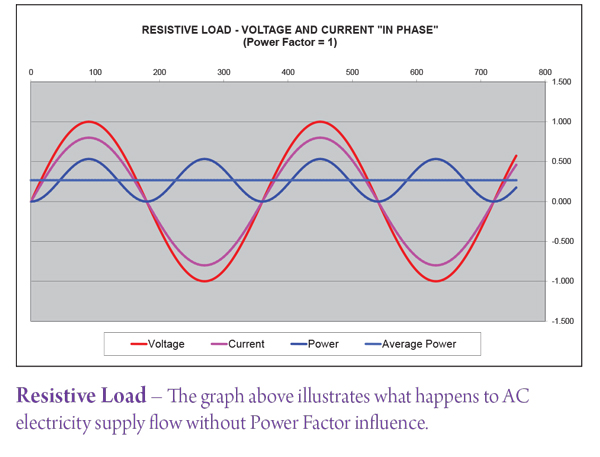
Other important things to monitor in relation to power supply are the quality of incoming power – so that you are getting exactly what you are paying for and know that if there is a blackout, whether the issue is on-site or not. For those with a Programmable Logic Controller (PLC) controlled plant it is also possible to monitor and log the on-site usage of power within the plant, track the history of this and collect the data so that trends can be ascertained by specialists.
Analysis of this data can then be used to determine peak usage figures, times and durations so that through the PLC load shedding can occur where possible again to avoid breaching a supply contract or in some circumstances (depending on your supply contract) save money by not using power during a peak usage period.
Some supply contracts can even forecast peak usage “Events” in advance that production planning times can be managed around to avoid paying a higher usage rate while the Event takes place.
It is worth giving the time to consider having the mains electricity on your site monitored by a qualified person and look at what options are available to you. At the very least, your site’s power factor should be looked at and if deemed appropriate have a correction unit installed so that you are not in breach of the regulations.
You must be logged in to post a comment Login