NEW Dozer Checklist
GAVIN MOREIRA, Member Services Manager of the CMPA, reports on the NEW Dozer Checklist.
The Secretariat, in consultation with Associate and Voting Members, has developed a NEW Dozer checklist for the industry, at the request of a CMPA Voting Member.
The function of the “Dozer Operator’s Pre-Start and End Day Safety Checklist” {1348} is to ensure that:
- All employees operating mobile plant conduct safety and maintenance checks on the equipment
- The equipment is in a safe and acceptable working order before commencing or finishing work
- The equipment is monitored during operation
- There is a record of inspection and a document path for initiating issues and recording any mechanical or safety concerns
Purpose
This checklist is to be used as a preventative measure to ensure that all required areas of mobile plant are checked before, during and at the end of production. The “Dozer Operator’s Pre-Start and End Day Safety Checklist” {1348} active pad is to remain with the machine so that all operators have access to its history.
Procedure
The “Dozer Operator’s Pre-Start and End Day Safety Checklist” {1348} is published as an independent pad containing 50 checklists and 10 “Issue Resolution Forms” {1325}. The Checklist consists of three sections:
- Pre-Start Checks
- Monitoring During Process
- End of Production checks
Instructions on how to use this checklist are following. The instructions for use of the “Issue Resolution Form” {1325} are supplied separately.
Pad assignment
Each item of mobile plant is assigned its own pad of the “Dozer Operator’s Pre-Start and End Day Safety Checklist” {1348} from Head Office. For additional copies of either the checklist or Issue Resolution Forms, talk to your Site Manager who will contact the CMPA.
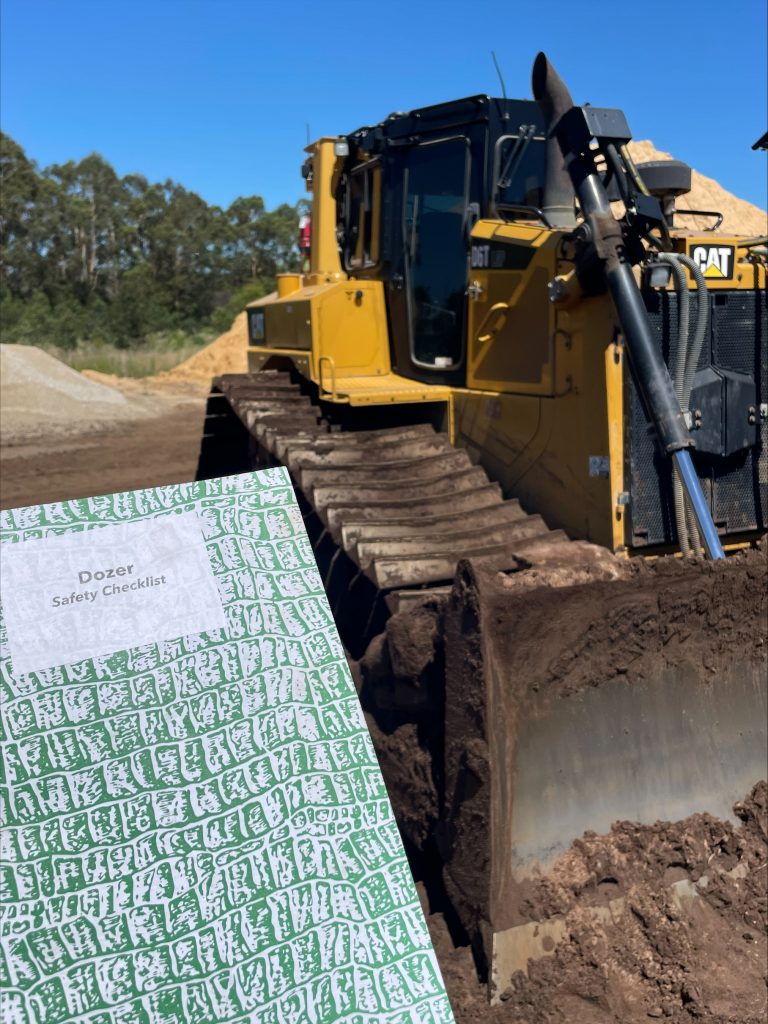
When to complete
Use a separate column for each shift or operator switch. All mobile plants are to be inspected in accordance with the checklist before, during and at the end of each shift in addition to those checks listed in the operator’s manual and company procedures. If the operator is to change during a shift, the checklist should remain with the item of mobile plant so that the next operator is able to ensure that all safety checks have been completed before commencing their shift.
These records form the basis of the plant maintenance procedures and will be subject to random inspection.
Identifying the equipment
When commencing a new checklist, it is necessary to complete the operator’s name and a Unit ID.
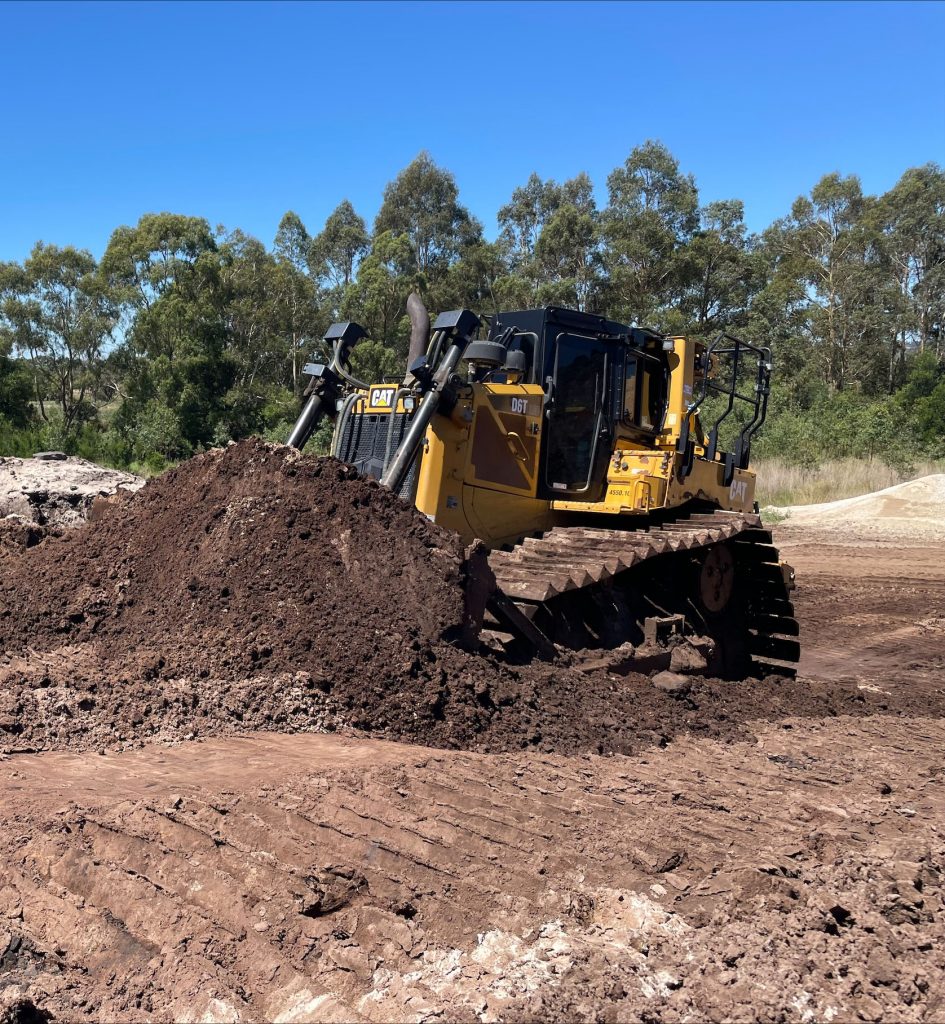
Filling in the form
To complete the form, fill in the boxes with a tick () if the requirements have been met, not applicable (n/a) if the requirements are not relevant to the item of plant, or a cross () if the requirements have not been met in accordance with company policies or procedures.
In the case of the requirements not being met, it is imperative that work is IMMEDIATELY stopped, the nominated person (i.e., Site Manager) is contacted and an “Issue Resolution Form” {1325} is raised.
Confirmation of completion
The Operator must initial the checklist and present it to the Site Manager to be signed at the end of each shift. The operator should then store the checklist in the employee workstation or lunchroom. Depending on company policy, the Manager’s initial may only be required at the end of each week (rather than on a daily basis).
Archiving
The Site Manager is to archive the white copy of the checklist while the yellow copy remains in the pad for the item of mobile plant’s records.
Thank you to Komatsu Australia and William Adams for suppling information on the dozers and to SafeMix, Allstone Quarry, Batesford Quarry, Burdett Sands and Matthews Quarry for reviewing the documents.
The Dozer Checklist can be purchased online via the CMPA
website https://cmpa.com.au/
You must be logged in to post a comment Login