New Loadrite X-Weigh Provides Right Solution
Galesafe Weighing’s installation of Loadrite®gear greatly improves efficiency and safety for both contractor and client, reports JIM & ROWENA CAIRNS.
GALESAFE Weighing Pty Ltd (Galesafe) is the Victorian distributor for the Loadrite® range of on board weighing systems. In late 2008, they were approached by C & K Cartwright Civil Contracting (Cartwright) to come up with a solution for tracking approximately 500,000 tonnes of material being loaded from a quarry in Wodonga, for part of the South Improvement Alliance (SIA) Melbourne – Sydney rail corridor upgrade project.
Cartwright’s were using a Hitachi 450 Z-Axis excavator to load road trucks and wanted to track the precise net load of each truck. This was not only for logistical reasons but also to maintain maximum payloads without risking potentially dangerous overloading.
In December 2008, a Loadrite® X-Weigh 2350™ system was fitted and calibrated by Galesafe at Cartwright’s workshop in Wodonga in readiness for the start of the project in January 2009.
Due to the flexibility afforded by Loadrite’s® proprietary Multi-Dimensional Compensation (MDC )™ weighing technology, the operator found he was able to operate his machine uninterrupted, and, at the touch of a button, was able to select the weighing position best suited to where he was digging at the time.
The system was initially fitted with a docket printer in the cabin of the excavator. Whilst such a printer was a very useful way to obtain a docket for each truck load of material, the time taken for the truck driver to exit the vehicle and walk over to the excavator to collect the docket, held up the excavator operator, the truck driver and the other trucks in the queue. This also created a potential safety hazard, with the drivers getting out of their vehicles within the quarry.
To address these concerns, a radio modem was set up to send the payload information to a remote docket printer approximately fifty metres from the loading area. When the truck was loaded, the driver proceeded to the printer to collect the docket, without having to exit the vehicle. This allowed the next truck to start loading immediately and, more importantly, removed the potential risk for any collisions between vehicles and pedestrians.
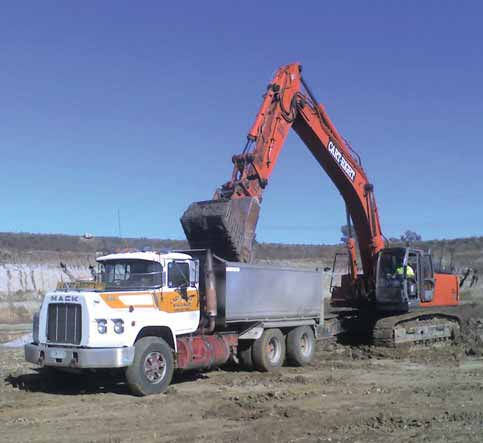
Th e X-Weigh 2350™ system is regularly checked for accuracy with loaded trucks being directed to a weighbridge. The Loadrite® dockets were well within +/- 1% of the weighbridge docket.
With the operation on full swing the benefits of the X-Weigh 2350™ system were being further realised. The Loadrite® Material Management System (MMS) was installed on an off-site computer. The information from the Loadrite® X-Weigh 2350™ on site is transferred to the off-site computer, some kilometres from the site, via a cellular modem, at intervals which were determined by Cartwright’s. The data is then viewed in a spreadsheet and converted quickly and easily into reports, either pre-formatted or customised.
With all this information at hand, Cartwright’s are able to track the utilisation of their excavator including cycle times of trucks, fuel burn per tonne loaded, and workload hours as opposed to engine hours.
The project client, SIA, is able to receive accurate payload information and is able to track the progress of the project Managing Director of Cartwright’s, Craig Cartwright, has since ordered a second Loadrite® X-Weigh 2350™ for a Cat 345C excavator.
He said “We were so impressed with the X-Weigh, modems and MMS on the Hitachi excavator, and the amount of time and paperwork it saved us, that it was an easy decision to immediately purchase a second X-Weigh for our Cat excavator”.
This project has shown how the Loadrite® X-Weigh 2350™ system for excavators, along with the wireless data capability and MMS, can greatly improve both efficiency and safety for both contractor and client.
You must be logged in to post a comment Login