Operator Training – Investing in your business
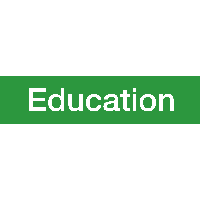
ROSS KELLY, Business Manager for William Adams Institute of Training reports on the benefits to your business for Operator Training.
If I may just start by asking a few questions for you to ponder:
- Do you operate mobile plant at your operation?
- What is the real cost if it is not running efficiently or worse, is down?
- What are the costs of damage or an accident?
- What are the long term costs of accelerated wear to components?
- Do you have a structured training plan in place for Operators?
- If so is it linked to career and salary progression?
Choices
In relation to training programs you have two main paths you may choose to follow:
1. Accredited
a. You may elect to have your staff complete a certificate lll or lV qualification
b. You may focus on a particular skill such as a unit of competency
2. Non Accredited
a. Perhaps informal peer to peer passing on techniques
b. Employee internal Trainer/ Assessor site program
c. External provided Operator training
Each has its pros and cons depending on what outcomes you are looking for, your budget and manpower constraints. Some will mean having your staff off site for a period of time, others (if not government funded) can be expensive.
You need to ask yourself will what I am doing provide meaningful outcomes, even a Return On Investment or is it just ticking a box and hopefully covering a liability hole.
Outcomes
Meaningful, well planned training can provide beneficial outcomes in many ways, some intangible and some tangible.
Safety Related
- Prevention of injury during mounting/ dismounting plant
- Site traffic management improvements and awareness
- Avoidance of accidents (collisions, roll overs)
- Haul road condition awareness
Operating Costs
- Reduced fuel consumption
- Extended tyre life (worn out vs damage and thrown out)
- Increased component life
- Reduced/ eliminate general machine damage
Productivity
- Improved cycle times
- Attention to loading zone management
These benefits and many more are achievable but it needs to be owned by the site management and passed down through the workforce to become part of the site philosophy and work ethic.
Getting Focussed
If you know what you want out of training, have specific issues to address or want training to become an integral part of your site operations do not feel locked into off the shelf packages which may or may not provide for your needs. You can shop around; form a partnership with a training organisation (or two) that may specialise in the area you wish to address.
An example of this was created when the CMPA and Conundrum Holdings were looking for an alternative to certificate courses for their Operators. Discussions were held with other training providers and William Adams Institute (industry training group) and a specific skills focussed training program was born.
These may contain four to six nationally accredited units which focus on a particular job such as Haul Truck Operator for example. The practical operation unit is delivered by an industry expert combining the required accreditation content plus industry best practice items. These can be customised to suit a site or company to incorporate site or company procedures. These can also be built into the natural career progression of Operators and linked to wage structures. Never underestimate the power a good training culture has on employee morale, providing a feeling of being valued by their employer.
Training should be looked at as an investment not an expense, if it is discussed and planned as any good investment should be to make sure it will provide benefit for the investor.
For further information contact:
Ross Kelly, Business Manager
William Adams Institute of Training
(03) 9566 0978 – [email protected]
You must be logged in to post a comment Login