Production of a Concave & Mantle
SEAN KINDER, Document Development Officer CMPA reports on the production of a Concave and Mantle from new Associate Members – Davies Baird Pty Ltd.
Introduction, overview and importance of steel
Davies Baird Pty Ltd in Melbourne is a sand-casting steel foundry, who have been operating and casting since 1883. Various products to a maximum weight of 5000kg, such as: pumps and valves, turbine runners and rail track work in a wide range of materials including duplex and super duplex, to a number of national and international customers. Vast numbers of capital and inventory assets purchased are made of some combination of steel alloys, which have been manufactured in a local or international foundry. It is beneficial to understand how these are produced, as poor quality product may be traced back to an individual process within the foundry. Analysed and tested chemical properties of the steel may be comparable, but physical properties may demonstrate different results.
This article describes the six production stages of the Davies Baird steel foundry process, for producing manganese wear parts. (concave and mantle for a cone crusher). The stages of producing a manganese wear part are: design, mould construction, melting and pouring the metal, heat treatment, dressing and testing. Manganese steel is known as a work-hardening material, which gets harder under more impact and hammering, is produced like the majority of metal castings by the sand-casting method.
Design Stage
Use of computer technology, programmed with a multiple of complex calculations involving material properties, allows for a more accurate finished product. Using soft ware specifically designed for molten metal flows and properties Davies Baird simulates the pour and flow of the metal into the mould to determine whether any shrinkage or cracking will occurred or voids may develop. The soft ware allows engineers to import the drawing from a CAD program, fit required vents and feeders, and locate where the metal flow should be directed to enter the mould, resulting in a quality product.
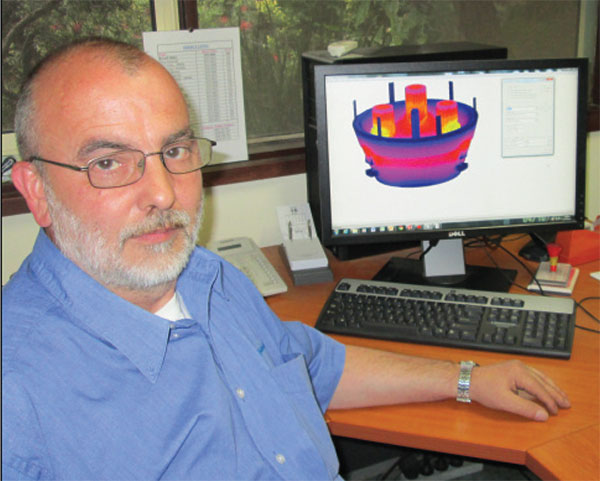
Pattern and Building the Mould
A timber template of the finished product, inclusive of feeders, vents, risers and the runner bar, is prepared. These allow the molten metal to fi ll the whole of the mould and minimise any potential for shrinkage, leading to cracking or formation of voids. When the pattern and mould are designed and produced, they are made with slightly larger dimensions, known as contraction rules, allowing for shrinkage, during the solidification. This replica is placed in a hollow box, which is filled with a combination of (66%) recycled sand (previously used moulds, broken down in a rotary reclamation drum) and (33%) new silica sand, and Chromite.
Chromite, mined and imported from South Africa, has a low quantity of silica. Due to this phenomenon, it has a relatively higher thermal conductivity compared to the silica sand, and is used to concentrate heat dissipation throughout sections the mould and act as a chilling agent during the pour and solidification of the casting. The sand has a phenolic and catalyst binder mixed in, allowing for fast and controllable hardening of the mould, depending on the ambient temperature and humidity conditions. This means there is little manual compaction and ramming required. Patterns and moulds may be produced in halves, depending on the size required. Once the sand and binders have hardened, the inner section (contact areas of the casting) of the mould is painted, swabbed with an AL-FLAM liquid, and then lit. This process allows the overall surface finish of the mould to be smoothed, therefore achieving an easier cast removal and an improved surface finish of the final casting.
Melting and Pouring the Metal
Electric induction furnaces are used to heat a combination of scrap metal, pig iron and specific alloys to produce the required casting composition. These metals fill the cavity of the furnace, which is heated to 1620˚C – 1630 ˚C.
Induction furnaces produce heat by using an alternating current to excite the metal atoms, in a solenoid coil, which the pot containing metal, is placed upon. Depending on the size of the product, Davies Baird has a number of furnaces with different capacities, meaning multiple pours can be completed in one day and raw material isn’t wasted.
Speed and accuracy are crucial in the next few steps, as the ambient temperature surrounding the crucible starts to cool it. Immediately upon leaving the pot into the crucible, over a hundred degrees is lost. Once the metal is heated, it is sampled and tested a first time, using a spectrometer, to determine the chemical characteristics, and any minor adjustments and additions are made, to ensure a correct job-mix formula.
A crucible is pre-heated to the required temperature and then the material is poured from the furnace into the crucible. Before the metal is poured into the mould, a second similar test is conducted, for quality control and to determine whether any impurities or contamination’s are present. The crucible is positioned above the mould and molten metal is gravity fed through a valve, until the cavity is full. Any left over metal in the crucible, is cleaned out, recycled and used in other pours.
The poured product is stored in the mould, until it has completely solidified, which may take some days, depending on its size. Using clasps or weight the 2 parts of the mould are held together, to ensure no movement, as the thermal energy and gases may cause movement, resulting in a poor quality or failed product manufacture
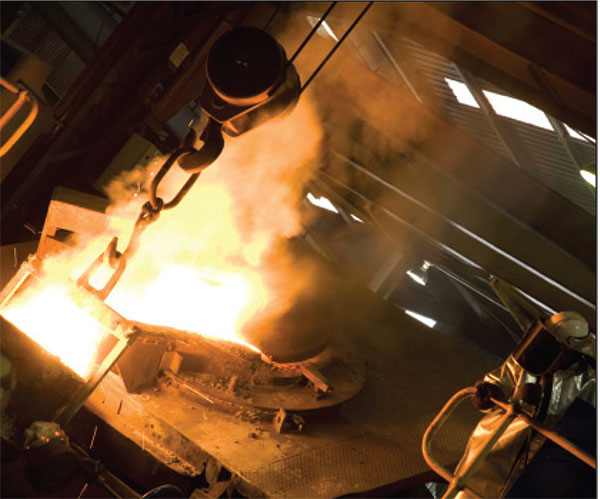
Cooling, Re-heating, Quenching and Work-Hardening
Once the mould has completely cooled, the casting is removed. Due to the pouring process, all surfaces are flaky and the structure, relatively brittle. The casting is placed in a reheating oven, and heated to approximately 1100˚C, which is left running overnight, and this is quenched directly the next day. Quenching is the process of rapidly cooling a metal by lowering it into a deep-water tank after it’s been heated to maintain a particular crystalline structure, strengthening and increasing the hardness of the product.
Grinding and Machining
After re-heating and quenching, all excess steel from the pour (vents, risers and the runner bar), are ground off and then the cast is placed in a shot-blaster, which surface finishes and cleans away any excess scale. Finally, the concave and mantle are machined and dressed by a vertical turret lathe, to ensure all surfaces are cleaned and all dimensions are correct. The final product is measured against original drawings, satisfying customer requirements.
Testing
Sample blocks and bars are produced alongside the primary cast (including the reheating and quenching processes so they have the same properties as the casting itself), so manufacturers can do chemical and physical tests once the product is finalised, making sure that it satisfies Australian Standard and customer requirements. Tests may include impact testing , bend bar test (used to test a material’s ductility and whether it will break or fracture under pressure) and hardness test which can be measured in various international standards such as Brinell, Rockwell etc.
Sand casting is a very versatile and productive way of manufacturing steel products, providing a method of producing a variety of different products with complex shape and configuration, with combinations of metals and alloys to provide a product to meet the customer requirements for material properties, performance and dimensional accuracy.
You must be logged in to post a comment Login