Reducing the Cost of Ownership & Extending Electric Motor Life
JOHN TREIMANIS, BEAK Electrical Pty Ltd’s Business Development Manager, provides an insight on getting the best out of your electric motors.
Tired of losing valuable production time due to motor failure? Did you know that?
- quarry work can reduce average motor life expectancy by up to a factor of 10:1;
- most motor failure is due to moisture ingress & failure of the insulation system;
- for every rise of 10°C, the insulation life of a motor is halved;
- if you can’t rest your hand on the motor casing (approximately 50°C) then it is running too hot; and
- Vacuum Pressure Impregnation (VPI) can significantly reduce motor failure.
THE harsh operating environment of the extractive industry severely shortens the life of electric motors but, by being aware of the impact of the environment on motors and custom modifying them prior to installation, you can significantly extend the motor life, improve efficiency and reduce time lost through motor breakdowns.
However, to be fully effective, upgrades should always be undertaken by a reputable, authorised, motor service repairer.
Selecting a local business may be geographically convenient but won’t necessarily give you the quickest response time or best quality outcome. A good example of this is that a gold mining company in Egypt recently had an urgent requirement to repair 2 x 500kw poles.
BEAK Electrical in Melbourne, Australia won the job as it offered the fastest turnaround time, despite being 12,500 km away. Although a relatively new name to the extractive industry, BEAK Electrical Pty Ltd, located in Keysborough Victoria, is ISO 9001:2008 accredited and has well established facilities to provide the complete range of modifications and services for all major electric motor manufacturers including CMG, TECO,WEG, Toshiba, SEW and ABB.
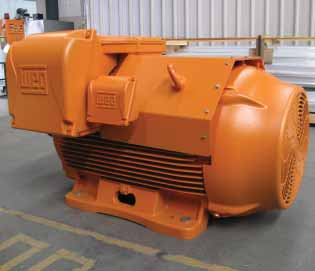
PROTECTION FROM THE ENVIRONMENT
Purchasing a motor with a higher IP rating will provide better protection from moisture ingress. Shielding the motor with a cover such as a sunshield or coal shield (as shown), will also greatly improve motor life by preventing build up of dirt between cooling fins and generally improving ventilation to stop the motor from running hot.
Warm motors in a cold environment will also produce surface moisture once the temperature drops below dew point. Fitting an anti-condensation heater that provides background heat will eliminate moisture ingress to overcome this problem. Installing thermistors in the windings will also enhance motor protection and eliminate the chances of overheating.
VACUUM PRESSURE IMPREGNATION (VPI)
Specialised services offered by BEAK Electrical include Vacuum Pressure Impregnation (VPI). VPI is the most cost effective treatment to extend motor life as it minimises moisture entering the winding and allows it to run cooler thus giving it thermal stability.
During normal operation, electric motors are subject to failure of the insulation system due to thermal, mechanical, voltage and environmental stresses that combine to reduce their service life.
The traditional solution to provide both a mechanical bond and strength is to apply varnish to electrical group windings in coils.
The application of varnish also retards the degradation, enhances the level of rewind quality and improves the performance of electric motors.
Varnish can be applied either by a dip and bake method or by the Vacuum Pressure Impregnation (VPI) process.
Solvent varnishes lose 50% to 70% of volume during baking and leave voids and air pockets in the windings which results in a weak sponge-like structure.
By comparison, VPI eliminates the dead air spaces that create hot spots within the motor winding coils as it provides a 100% solid mass structure with the greatest mechanical strength. The result is a cooler running motor due to superior heat dissipation and the highest level of protection from the environment.
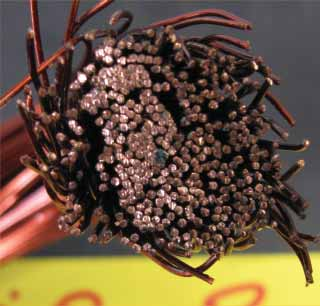
penetration of varnish
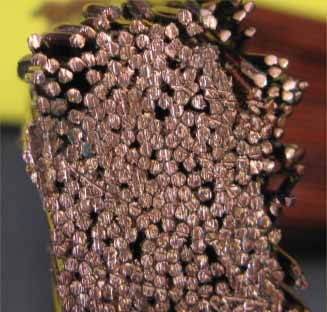
Estimated 88% penetration of varnish
The above photographs compare the results of applying varnish to identical coils of electric wires by the two alternative methods.
A motor winding that has undergone VPI is also virtually impervious to oil, moisture, and chemical contaminants.
SUMMARY
Observing the following few basic rules will ensure that you get the best out of your electric motors and minimise production downtime which in turn improves the return on investment (bottom line):
- Always purchase a reputable brand motor that is designed for your specific requirements;
- Make sure that the motor is suitably modified and adapted to suit the environment;
- Have your motors maintained in accordance with the manufacturer’s recommendations; and
- Always use a reputable, reliable and qualified electric motor repairer.
For further information contact John Treimanis, Business Development Manager BEAK Electrical Pty Ltd. Ph: 03 9701 5540.
You must be logged in to post a comment Login