Reducing the risk of lifting lugs
Lifting wear parts into crushers is a difficult and dangerous task that will oft en rank highly on site risk assessments. Particular challenges are faced when maneuvering jaw faces, mantles and concaves into position. Report by SARAH ANDREW, CMPA Project Manager.
TO discuss the current practices in more detail and to explore possible ways forward, 16 site managers, specialist welders and associated consumable suppliers attended a meeting on Thursday 22 January at Boral Wollert.
Those present had a wide range of skills in foundry works, welding, installing and utilising wear parts. Between them, there was over 300 years experience!
This article will cover the issues of current practices specifically training, planning and procedures. The next edition will look in depth into current manganese practices and where to from here.
CURRENT PRACTICES
Wear parts have lifting lugs welded onto them at the quarry site for both installation and removal of the jaw, mantle or concave. This process is generally undertaken by designated company welders or contractors.
Issues held by those in the industry include:
- The risk of lifting and lack of confidence in all aspects of the job
- Difficulty of the task and exposure during installation and removal
- Lack of planning both for the job as a whole and site preparation
- Pressure on downtime (lack of resources)
- Unplanned or unexpected change-outs
- Variation to procedures
- Testing before lifting
- Lack of clarity in electrode type
- Variability of manganese and casting quality
- Lack of documentation from liner suppliers
- Care and attention required for the task
- Lack of experience
- Lack of understanding of what is being done
- Lack of training and specialised skills
- No good alternative to welding available
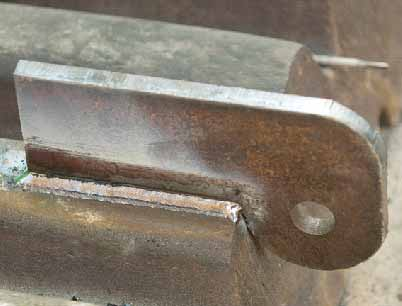
TRAINING
Training in the industry tends to consist of informal, on-the-job type arrangements with most welders coming from within the industry rather than being welders by trade.
It is important that industry moves towards including formalised training requirements into their existing practices.
Australian Standards provide a strict set of standards that welders must comply with to be considered sufficiently trained for the purposes of welding to manganese.
These requirements are:
- They should hold a welding qualification that complies with AS 1554 part 1 SP. Alternatives include:
- AS 1796 Cert. 3E
- AS 3992
- AS 2980
- ISO 9606-1
- The training should be current
- The welder should have experience
- The welder needs to be able to inspect the welds
- The welder must document events
As this is a highly specialised area, there are only a limited number of trainers who can assist the industry. One such trainer is Quantec Solutions. They have developed a course specifically for the construction materials industry that assists sites in addressing these issues.
The course is structured as either a one day course (for welders who are highly skilled and experienced) or a five day course (for all other welders).
The main difference between the one and the five day course is the ability of the trainee to retain the knowledge over time and the depth of the skill attained.
PLANNING AND PROCEDURES
Procedures will vary between sites, and particularly weld procedures, although developed, are only available to those persons who have undertaken formal training and in some instances from the supplier.
That said, there are a number of areas that can be considered in any site’s procedures for replacing wear parts. Such procedures or risk assessments need to be revisited (and if necessary, reviewed) each time the process is undertaken.
These are outlined below:
Where possible, plan replacements ahead of time. This can be done by considering the wear rate of the liner. In the time leading up to the replacement, the following tasks can be undertaken:
- Ensure replacement liners are ordered and on site. If they are unusual or customised, it might be appropriate to keep a spare on hand. It is important that the dimensions of the casting are checked at delivery and that they conform to the requirements of the particular machine. If there are any discrepancies, contact the supplier ASAP.
- Engineer and prepare lifting lugs in the correct steel. Lifting lugs are best if they are profile cut from AS 3678 grade 350 plate to an engineer’s design that is appropriate for the crusher size and properties. The thickness of the steel will be dependent upon the total weight being lifted and this should be considered when engineering. Consider the placement of the liner – it is easier to design the lifting lug to lift the wear part on the correct angle than correct it while lifting.
- Ensure the correct consumables are available in sufficient quantities. This will include lifting lugs and electrodes. Electrodes should be from the austenitic range (E309L-16 or E312-16), and no larger than 3.2mm for a vertical up and 4mm for down. Ensure electrodes are stored in a dry evening.
- Attach lifting lugs to the new wear parts to make one less job during change-over. Ensure these are attached in accordance with any procedures and test integrity before lifting. When welding lifting lugs, there are several key points to be considered:
- Grind the surface of the lug but do not pre-heat
- Use correct electrodes
- Quench the area aft er welding to ensure the manganese does not soften
- Use twin lifting lugs at minimum
- Ensure records are kept of the weld. This would include the welder’s name, type and size of electrode used, supplier of electrode, weather conditions including moisture content of electrodes, temperature of area to be welded before during and after, the size of the lifting lug, and time taken.
- Ensure all tools and equipment (such as platforms and ladders) are in safe working order and available.
- If necessary, arrange an appropriately rated mobile crane to be present at change-over. Ensure that mobile crane operators hold a licence issued by WorkSafe or a similar authority. If possible, select an operator who has had past experience in lifting wear parts.
Prepare the work area so access is safe and stable for all participants. For instance:
- Clean up any spillage and, particularly on sites containing silica, wash down the area
- If necessary, ensure there is a safe and stable work area for the mobile crane
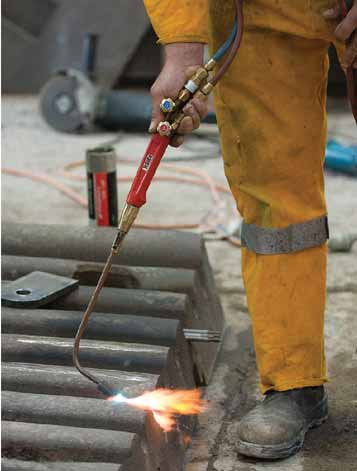
Remove the existing wear liner.
- This is a very high risk activity and will require a risk assessment on site prior to conducting the activity. Ensure all participants are aware of what is being undertaken and how it will be done, and that all lifting equipment is appropriately rated for the task. This may require referencing OEM manuals to ensure proper procedures are followed. Where possible, ensure people do not position themselves where the wear part could fall or crush them. If this is unavoidable, ensure there are secondary protections in place (i.e. a drum inside a jaw crusher).
- Isolate the plant, and install any access ways (such as ladders and platforms). Ensure all tools are on hand.
- Access to the liner may require other items of plant be moved. This should occur now.
- Weld lifting lugs onto the liner in appropriate positions. This must follow a welding procedure that incorporates appropriate recording. It is important to consider that the manganese has work hardened and has surface effects from initial heat treatment during manufacture which will require surface material to be removed by grinding prior to welding.
- Test lifting lugs before lifting if possible. This will consist of giving each lug a good tap with a sledge hammer. This will not damage the weld and should be carried out when the weld has not cooled and once cooled.
- Remove wear liner according to OEM instructions and clean the backing area. Ensure access is clear, bolts are loosened or removed as necessary, the liner is loosened if possible, and lifting devices are clear and have free movement.
Install new wear liner according to OEM instructions using lifting lug and then cut off lifting lugs. The used lugs should be destroyed as they are not safe to reuse.
Pack away tools, remove access equipment or permits, and replace any plant that was removed.
You must be logged in to post a comment Login