Reflecting on WorkSafe Victoria Quarry Visits
TONY FERRAZZA, Senior Mining Engineer – Earth Resources Unit of WorkSafe Victoria reflects on safety in quarries for the 2012/13 financial year.
THE safety regulation of Victorian quarries came under the jurisdiction of the Earth Resources group in January 2013. With this new structure in place and as we enter the new financial year, it is a good time to reflect on the findings of the inspectorate over the last financial year.
Over the year, WorkSafe Victoria visited 137 Victorian quarries comprising a mix of operations from large to small and located in both metropolitan and regional areas. Of those quarries visited, 70 resulted in notices being issued. A quarry is defined as an operation where material is being extracted for processing under a Work Authority.
THE BASIC NUMBERS
- Primary visits – 137
- Total visits to quarries – 244 (figure includes dangerous goods visits and follow up visits)
- Visits to quarries resulting in Notices – 70
- The number of Notices issued – 166 (146 Improvement Notices, 2 Prohibition Notices & 18 Dangerous Goods Improvement Notices).
- The number of Voluntary Compliance – 21

KEY ISSUE
- Plant guarding is continuing to feature as a major area of concern. Examples include sub-standard guarding, poorly maintained guards (especially those on electric motor fans) and guards not replaced following housekeeping and maintenance activities.
- Plant Maintenance includes corroded or damaged fixed plant structure, inoperative conveyor pull wires, damaged hand rails, material falling from height and insecure and non-rated pallet racking.
- Plant lifting gear comprises plant not ‘tagged and tested’ or damaged. Also forklifts with illegible Safe Work Load ratings.
- Dangerous Goods – Explosives notices included inadequate signage, non-compliant explosives transport, and the presence of metal surfaces within the explosive magazines, the presence of combustible material within the magazine bunded area, inadequate earth stake and lack of explosives manifest.
- Dangerous Goods – Storage notices mainly related to the storage of oxygen and acetylene tanks.
- Traffic Management/Site Security – This has become more of a focus with the transfer of quarry regulation from the Construction Group to Earth Resources and includes inadequate unauthorised entry to site as well as truck traffic management around stockpiles and safety devices such as flashing lights not working or not in use as required.
- Manual handling has been identified as a new category. This is in line with the WorkSafe hazard targeting program.
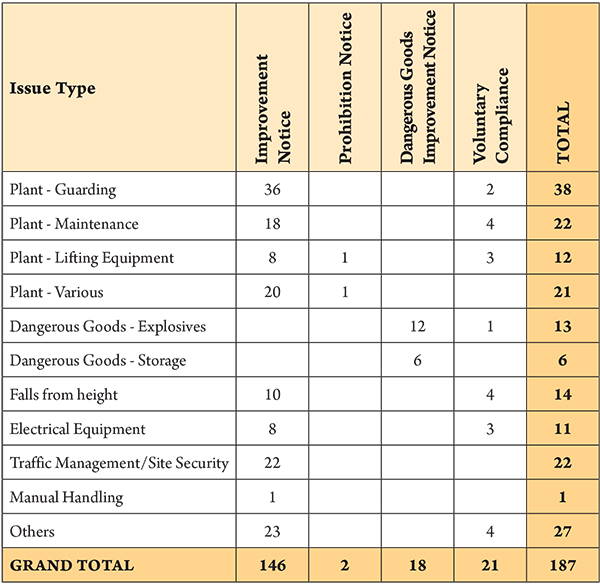
REPORTABLE INCIDENTS
Over the July 2012 to June 2013 period there were a total of 16 incidents reported (6 significant and 10 minor).
- 30t Excavator breaking rocks, track left ramp, excavator fell on its side. No injuries occurred.
- Worker placing rams for removal of crusher bowl, jammed index finger, surgery required.
- Loader tipped over on soft ground.
- Oxy-acetylene fire on crushing area conveyor 20m above ground – extinguished by employees.
- Semi Trailer tipped onto side. No injuries occurred.
- Water tanker slipped over edge of road and overturned.
- Piece of metal from Impactor Plant hit employee leg. Worker taken to local GP.
- Unloading PVC piping from truck – pipe slipped. Lacerated face.
- Employee hit by conveyor bearing. Sustained back injury.
- Agitator driver pinned between truck and mould. Worker hospitalised.
- Potential rock face explosives misfire.
- Dump truck hit dirt wall and tipped over. No injuries occurred.
- Contact with submersible pump resulting in minor shock.
- Non-reporting of a crushed rock bin collapse and the use of a decommissioned crane.
- Excavator bucket falling onto a B Double cab narrowly avoiding the driver.
- A batter slip occurred and although no one was in the vicinity it is considered significant.
CONCLUSION
These findings emphasise that, when it comes to safety, all workers in quarries need to remain vigilant. Even though a systematic approach to safety risk management is being progressively implemented by management in many operations, this in itself does not guarantee safety.
Ongoing safe work practices driven by a safety culture which understands safety hazards and controls should be the aim.
You must be logged in to post a comment Login