Risks Associated with Cement Silos
SEAN KINDER, Document Development Officer for the CMPA reports on the risks associated with Cement Silos.
CEMENT silos have several risks associated with their operation and service, due to service and maintenance tasks involving working from heights or in confined spaces.
Cement silo designs involve pressures and material properties, therefore potential of leak or blockages to form, ultimately causing incidents involving human health, plant structural integrity and environmental issues.
Recently, there have been several incidents involving silos, cements and concretes in these areas, including:
- Companies fined large sums of money due to employees inhaling excessive amounts of cement powder affecting their health.
- Leaks leading to plants, neighbouring and local wildlife reserves, being damaged by concrete slurry, due to poor waste management systems, or covered in cement dust, (in one case dust covered over 3 blocks in a suburb) and a site roof collapsing nearly missing a worker.
- Workers fatally injured due to silos collapsing, and workers being engulfed in material, crushed or workers falling from height.
These examples are just a few of many and it has been suggested that silos, bins and hoppers have incident frequencies, comparable with the most dangerous of industrial equipment. Whether this results in downtime repairs or in extreme cases environmental damage and loss of life, these cases are always costly, as the owner experiences halt in production, fines and/or exposure to danger, according to Carson and Holmes (2003).
Failures of silos may be a result of a number of different errors including design and construction flaws, improper usage and lack of maintenance. Design errors and construction errors relate to whether the silo was manufactured properly. Moisture and thermal expansion factors are also considered. Important checks which should be made regarding the construction of silos include checking for an even foundation and making sure all contractors building materials are correct (bolt sizes and strengths, wall type and thickness…etc).
Foundations and building materials should be examined regularly for faults and to make sure the structure is secure.
Silos must be routinely inspected and faults appropriately documented, monitored and actions taken accordingly.
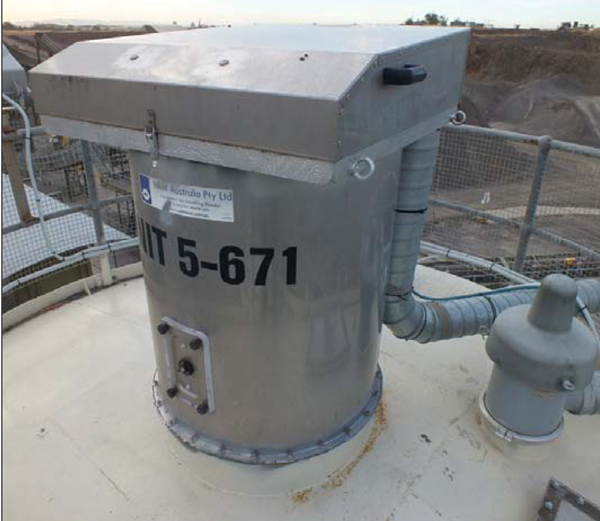
John Mawson (E.B. Mawsons & Sons Pty Ltd) suggests this should be completed according to usage requirements and dependent on exposure to the weather. Corrosion, due to exposure to weather can weaken side walls and support structure overall affecting its integrity, acting as a catalyst towards collapses.
The CMPA Conduct Blending Reference Manual recommends ‘visually inspecting all storage equipment pre-shift and post-shift for damages including cracked legs and welds, undermining of foundations, rust and other signs of fatigue’. Safety equipment including hatches, alarms, valves and filters according to a series of Holcim and Scope Engineering Services checklists should be checked regularly. Silos should be correctly signed and bollards/guards erected to ensure protection from truck drivers when being filled.
It is vital that any formation of blockages within silos (hang-up, bridging and rat-holing), be fixed appropriately once identified. Some operators have been reported standing on the blockage resulting in fatal events of engulfment, whereas others have been known to self-induce vibration on bins, hoppers and silos to resume the material flow. However this can be also dangerous long term.
According to Carson (2000), ‘most silos aren’t designed to resist dynamic loads caused by collapsing blockage’.
Mark Thompson (OLI Vibrators) states that ‘hammer-rash is also a result of hitting the external wall of the bins, hoppers and silos, which combined with altering overall integrity of the structure, misaligns the discharge end and creates potential for future hangup, bridging and rat-holing’.
Many items in the market may be installed on or inside silos as preventative and reactive measures against blockages including: air canons, vibrators and liners. These are designed to stop worker access to inside the confined space, eliminating the potential for engulfment or falls from height.
Over-pressurising a cement silo may result in a range of incidents from cement expelling into the atmosphere affecting the environment and suburban areas. As stated by many industry professionals, the most common incident involving a cement silo is over-pressurisation upon re-filling. Physical damage to the structure of the silo may occur with potential for fatal consequences. Various incidents have occurred recently involving over-pressurisation, which have cost organisation in lost time injuries (LTIs) and financially with damages to the silo, site offices and suburban areas.
The UK Minerals Process Association released a guidance notice which suggested recommendations of avoiding this problem including: Cement truck delivery drivers undertaking correct training in filling silos and quarry supplying adequate signage and directions to the fill station, correctly sized filters be installed expelling excessive air into the atmosphere, high level alarms systems operational, fitting adequately sized pressure relief valves to accommodate for any over-pressurisation and installing shut-off valves. These warn operators and prevent the silo from overfilling, over-discharging and satisfy any pressure changes. Several products are on the market for ensuring safe silo operation and filling including WAM Group’s KCS Silo Safety System package (containing pressure gauges, relief valves, filter systems, level indicators and alarms).
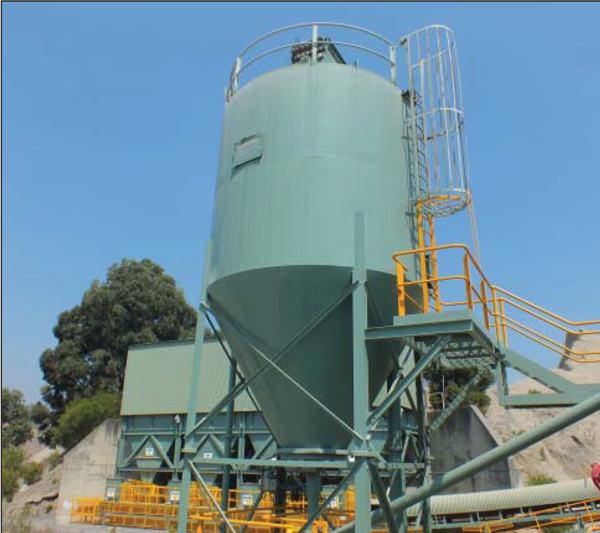
Wayne Hanson (WAM) also states that a pressure relief valve with discharge to ground pipe should be installed as a final safety device. This pipe lets the truck driver or operator/supervisor know that the silo has over-pressurised and contains the asset, by not releasing it into the atmosphere.
Knowing limitations of these sensors should also be taken into consideration according to Craig Cahill of CEC Electrics. Due to the conical base of the cement silos, level sensors need to be strategically placed to achieve minimal error. It should also be noted, that when silos are being filled, the powder won’t be uniformly distributed throughout the chamber. This should also be taken into consideration, when installing level sensors. Craig suggests measuring the capacity as a percentage reading, rather than a weight, because of the filling process. As stated by many service and operator checklists, these safety devices need to be checked and serviced regularly, to ensure safe working procedures.
REFERENCES –
Carson, John W., (2000), Silo Failures: Case Histories and Lessons Learnt, Jenike & Johanson Incorporated, Westford, MA.
Carson, John. W and Holmes, Tracy, (2003), Silo Failures: Why Do They Happen? Task Quarterly 7 No 4 pp (499-512)
You must be logged in to post a comment Login