Safe and Effective Bench Practices
SHANE SLAUGHTER, Senior Technical Advisor for MAXAM Australia reports on safe and eff ective Bench Practices.
ALL quarries are looking for both performance and compliance in their processes, with drill and blast being no exception. Costs and margins, particularly in the present domestic quarry market, are under constant pressure and review. There is also the constant scrutiny from both legislators and neighbouring communities on site operations. Compliance to meet and exceed expectations of this scrutiny does not always mean that costs can be reduced but in fact in some cases require increased investment, both capital and time, in process improvement and proper application of current technology just to keep the front gate open.
Focus must be placed on assessment and management of risk, knowledge of correct product application and what physically happens on the bench during loading and firing of the blast i.e. the bench practices. Safe and effective blasting is always at the forefront of MAXAM as it operates in all variety of rock types, bench geometries and work process found at sites supplied globally. Bench practices are very visible and it is quickly evident if the process is under control and risks managed by observing them. There is a direct link of safe and effective bench practices with correct application of explosives on the bench and therefore good and safe blast results. MAXAM understand this and place great emphasis on bench practices.
Good blast results rely on a controlled progressive process from initial planning to the final excavation of the blast muckpile, being;
- Design
- Preparation
- Drilling
- Priming
- Loading
- Stemming
- Timing
- Firing and checking
- Extraction
What we will now consider briefly is the part of the process from preparation to final checking of the blast, drilling excluded as this is a whole subject on its own. MAXAM place great emphasis on bench practices as they recognise that if they are not carried out as required, risk increases potentially leading to incidents and or ineffective blast outcomes.
MAXAM always endeavour to assist their customers with implementation of industry best practices including bench practices. Blast area preparation. Good blast results do not result when poor blast area preparation is in place. Sheeting of areas to be blasted and the formation of adequate access for personnel and equipment is essential.
Sheeting benches with excessive material will however affect the process with potential for lost blastholes and or loss of explosion gases due to poor confinement. Water management on the bench is essential to prevent damage to blastholes or the explosive within them.
Also if water is present in front of the face this will cause issues with confinement and or burden control. The delineation and securing of the blast area must also be carried out to a standard or risk and security of the blast will be compromised. Standards of blast delineation need to be sufficient to separate any person or equipment from the blast activities.
MAXAM abides by the principle that safety out ranks production and will not commence or continue activities on any blast site if it feels safety is or could be compromised.
Vehicle movement on blast must be controlled and once blastholes are drilled, vehicle movement within the blast area should be restricted to prevent loss of depth or of entire blastholes.
Stemming distribution must be carried out before loading commences and it must be carried out such that it does not interfere with blasthole collars or MSU access on the blast.
Practices that limit MSU movement or cover and fill blastholes with stemming should not occur. Stemming placed haphazardly within a blast area will also raise the risk of injury to personnel on the bench.
Careful placement of explosive accessories, boosters and downhole detonators, must occur such that they are not lost in drill cuttings or down blastholes.
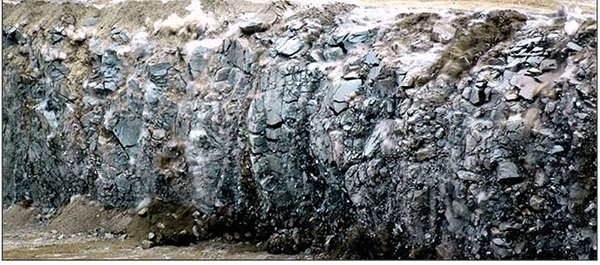
Priming of blastholes. If priming is not carried out as required, adequate initiation energy may not be transferred to the explosive and or misfires may occur. Primers are made of sensitive substances that should never be impacted upon and if mishandled will result in injury or misfires.
Loading of blastholes especially pumped explosive product must be carried out as per manufacturer’s instructions. Top loading of pumped product is not recommended by MAXAM due to potential sensitivity and density concerns as well as likely dislocation of explosive columns by disruption of material from the blasthole sides. Hose retraction rates must be carefully monitored to ensure complete explosive columns free of water or mud are loaded. Primers must be within this explosive column and not “floating” due to poor loading technique.
Stemming of blastholes is a very important part of the process and can add value to your blast. The right stemming can reduce powder factors, increase containment reduce environmental readings and increase fragmentation all these having flow on economic improvements to your site that can’t be ignored.
Surface connection requires following the connection techniques recommended by the manufacture. When personnel do not take care and ignore manufacture recommended procedures then issues do arise. This is where human error can be very visible and risk becomes unacceptable with misfires occurring as a result.
Also careful checking of blasts in a methodical manner by more than one person is essential. The most experienced shotfirer can still miss inadequate connections and any extra “checking” should be welcomed and implemented by them.
Firing of the blast requires very good disciple from the shotfirer and blast controllers otherwise unacceptable risk will occur. Clearing of personnel and equipment should be thought about well before loading commences not when the setup of the blast exclusion zone is commenced.
Checking of the blast post firing is an often overlooked bench practice that is vital in bringing to a close the bench activities. If the blast is not checked fully and misfires are missed then risk is raised to site personnel excavating the blast.
It is often the small things that make the difference when achieving good safe and effective blast results. This is especially the case when looking at bench practices. If variations to good practice creep into your bench practices major challenges will occur affecting the safety and economics of your site.
The MAXAM team can and will assist with advice on bench practices wherever asked. Every small improvement, every little correction to practices and application of products and services can and will improve your operation economically, productively and safely.
For further information contact Allan Dawson, Victorian Area Manager for MAXAM Australia 0408 456 966.
You must be logged in to post a comment Login