Safe Work Procedures or Safe Work Method Statements?
Written by DAVID MCKELVIE, Director of SafeMix, a WHS consultancy that specialises in supporting the Construction Materials Industry. (CMPA Member since 2004).
Providing instruction to workers on how to safely conduct their roles is not only imperative to ensuring a safe workplace but a fundamental duty under section 21 of the OHS Act.
Over the last two decades many employers have relied upon Safe Work Method Statements (SWMSs) to provide these instructions.
From my observations SWMSs have become the “norm” and many employers believe that they are legally obliged to use SWMSs as a means of instruction.
This belief is correct if the employer is engaged in construction activities as the OHS Regulations Chapter 5 Hazardous Industries, Part 5.1 Construction mandate the establishment and implementation of SWMSs for High-Risk Construction Work.
These regulations state clearly that the exploration for, or extraction of minerals or stone is not construction work therefore a SWMSs is not required, although instruction still is under the OHS Act.
Why not use a SWMS?
A SWMS is a document that presents three columns that list the key steps of the task, the hazards associated with those key steps and the controls required to either eliminate or reduce the risk arising from the hazards.
Along with other requirements the regulations state that a SWMS is a document that is set out and expressed in a way that is readily accessible and comprehensible to the persons who use it.
The majority of SWMSs I have attempted to read are clearly not comprehensible to the workers who use them. This not only my view but is also the view of countless workers I have discussed this matter with.
The SWMSs I regularly come across in the extractive industries are generally cumbersome, generic to many industries and contain over ten and up to fifteen plus pages.
The reason being is they tend to include a lot of unnecessary information, including listing all potential regulated High Risk Work activities, referring to relevant legislation and Australian Standards, tabling likelihood, consequence and risk matrixes and listing both residual and inherent risks values for each hazard in every step of the task.
Hardly comprehensible when many workers may need to acknowledge and commit to several SWMS as part of their role.
Many of these SWMSs are generic to the civil works/ earthmoving industry and are not specific to the quarry, its workplace environment and the methods of extracting and processing materials that are being applied. These SWMSs are often purchased online and provided as a template that the employer can amend to suit their needs, but unfortunately for the workers who use them these amendments often only include company details such as titles, logos and addresses.
Many SWMSs have become overly crowded documents that lose focus on what counts, e.g., site specific hazards and controls presented in a manner that is clearly comprehensible to the workers who use them.
SWMSs or Job Safety Assessments (JSAs) when written in a clear and brief manner, without all the unnecessary content are an excellent means of identifying safe work practices when undertaking one off or non-routine repair, maintenance and installation work where risk is foreseeable.
Why use a SWP?
SafeMix has been providing Safe Work Procedures (SWPs) to several CMPA Members over the last 10 years. The SWPs have evolved over time, through the sharing of knowledge and experiences and the input of workers.
Most importantly these SWPs are brief, generally between 2 and 4 pages and only contain relevant information.
An SWP for a Sales Loader is inclusive of the following content:
• Potential hazards associated with the activity,
• Fit and competent to work requirements,
• Prestart inspections requirements,
• General operations plus,
Interaction with mobile equipment and pedestrians
Loading trucks
Stockpiling
Working below faces:
• Shut down requirements,
• The Never Evers,
• PPE pictogram.
It is now more important than ever for employers to provide instruction and retain knowledge in regards to safe work practices for reasons such as:
• A lot of older workers are leaving and have left the industry taking their knowledge with them,
• We are facing worker shortages and are often forced to employ workers without industry specific knowledge, e.g., the hazards associated with operating an excavator on a road project are very different to the hazards workers are exposed to operating an excavator under a face,
• Due to worker shortages workers are often operating
several types of mobile equipment and are not necessarily
specialist operators, as once was the case
• The benefits of operating a safe workplace are now better understood. Workplace safety is now both a company and personal value of absolute high priority and delivers operational efficiency and worker ownership and accountability.
It is my experience that SWPs for routine roles and or activities that take into account site specific requirements and are written in a manner that is brief, targeted and easy to read is a very practical and economical means of
providing instruction and retaining knowledge.
Along with other services SafeMix can assist members in establishing practical and site specific SWPs, Worker Induction Manuals and Safety Management Systems.
David McKelvie has been working in the Quarry and Concrete Industry since 1984 and SafeMix has been supporting the CMPA and its Members with Workplace Safety Solutions since 2013.
If you require support, you can contact David on 0407 022 117
or email [email protected]
Alternately visit our website www.safemix.com.au
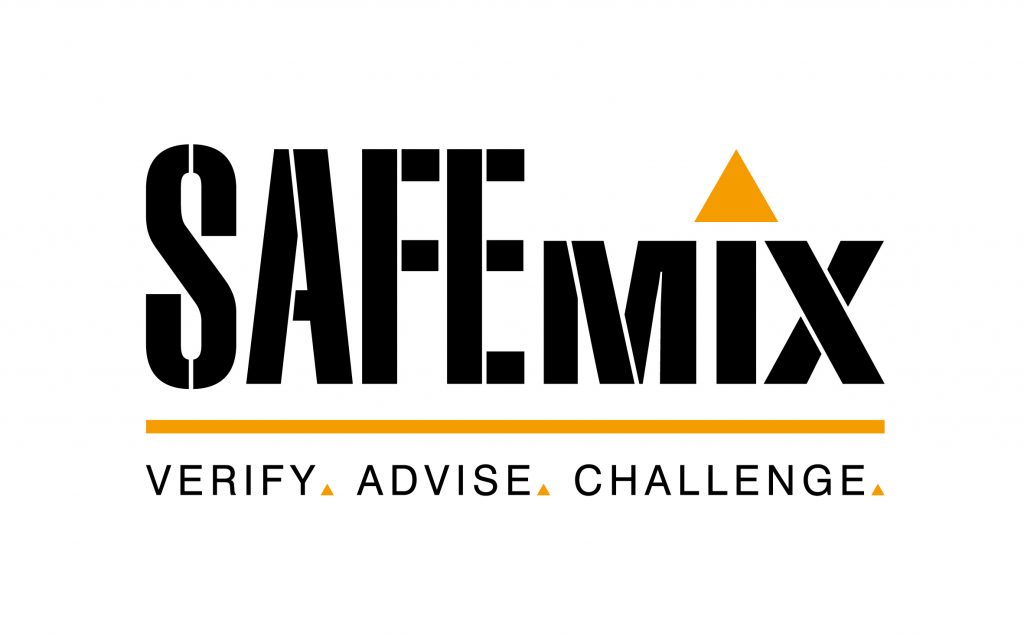
You must be logged in to post a comment Login