SAFETY UPDATE (Issue 19)
Excavator Boom Collapses
Incident:
WorkSafe attended an incident at a construction site where the boom of an excavator collapsed across the tray of a tip truck.
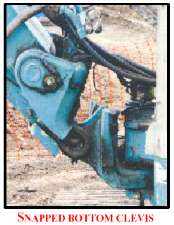
Preliminary Investigation:
Initial investigations into this incident found:
- No injury occurred
- Slight damage occurred to the tray of the tip truck
- The excavator had a rated capacity of 7 tonnes and was:
- A pivoting boom type
- Approximately 7 years old
- An Australian delivery model
- Fitted with a rake bucket
- Loading rock into the tip truck
- The bottom clevis (yoke), which allows the boom to pivot, snapped
- The clevis appeared to be a one piece casting
- Within the casting were old and quite deep cracks
- Cracks started at the inner surface of the clevis
Remedial Action:
WorkSafe issues a Prohibition Notice to prevent any further work with, or repairs to, the excavator until engineering and metallurgical reports were undertaken on the failed component.
Conclusions:
Without the availability of the engineering and metallurgical reports, WorkSafe can only speculate on the possible causes of the clevis failure:
- Fatigue due to cyclic forces
- Frequent overloading of clevis
- Pre-existing imperfections within the casting
- The design of the clevis
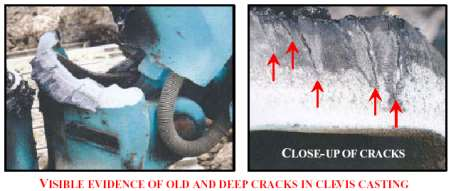
Recommendations:
As an interim measure, WorkSafe recommends that particular attention be paid to the bottom clevis of pivoting boom type excavators of all makes, models and capacities. Employers and owners of this type of plant should ensure the bottom clevis is inspected for signs of fatigue cracking at regular intervals.
Further information:
WorkSafe will continue to investigate this incident and evaluate the engineering and metallurgical aspects of this failure. Once the investigation has been completed and the underlying causes of the failure have been identified, WorkSafe will make final recommendations to the industry.
If you require information on your particular brand of excavator, contact the manufacturer or the manufacturer’s Australian distributor.
FATALITY REPORTS
MINER CRUSHED TO DEATH BY RIG—QLD
A miner using rock-drilling equipment on a cliff face died after his rig slipped and crushed him. Initial investigations revealed he was re-aligning the drill closer to the cliff face, when a rock slide occurred under the rig. The man fell more than 20 metres and was crushed under the falling equipment.
DOZER FALLS 150m INTO 4.5m DEEP MUD—Papua New Guinea
A D10 dozer operator was cleaning a bench on the 2400RL in preparation for drilling. He may have been blading towards the crest of the bench and went over the edge plummeting 150 metres into the 4 to 4.5 metres deep mud on the 2250RL bench. Only the top half meter of the dozer cab could be seen sticking out of the mud. Recovery was slow because of the unstable mud conditions and because the safety of the recovery team was paramount. The operators body was recovered from the cab of the dozer.
HIGHWAY WORKER RUNOVER—USA
A dump truck hauling stone backed over a highway department foreman, killing him. The foreman was walking behind the truck to repair a soft spot on a road. He had been directing the truck to pour stones in the hole, then walked behind it while making a work-related phone call. The driver could not see the foreman when he backed up.
MAN DIES IN COAL HOPPER ACCIDENT—Canada
The body was found buried beneath a pile of coal inside a coal hopper. An autopsy is scheduled to determine whether further investigations are necessary.
MINING FATALITY—QLD
A driller received fatal injuries when he and his air-trac drill fell over the face at a small open cut mine. The driller was working on a bench drilling ground support and blast holes when he and the drill rig went over the edge of the bench and fell about 21 metres to the bottom of the open cut. The driller received extensive head and leg injuries from which he died.
PROSECUTIONS FOLLOWING MINING FATALITY—QLD
In 2002 a loader operator was crushed in the articulations point of an Elphinstone R2900 loader when the secondary steering lockout which prevents articulation of the loader when the door is open was inoperative.
In 2003 prosecution proceedings for failing to meet obligations imposed by the Mining and Quarrying Safety and Health Act 1999 began against the mine operator, the site senior executive and the mining contractor. In 2004 the site senior executive received a penalty of $3500 and $313.50 costs and the contractor a penalty of $30,000 with $12,590 costs. The mine operator pleaded not guilty. Following the hearing the case was dismissed on the technicality that the prosecution failed to prove that the company was indeed the operator of the mine at the time of the accident.
CORONER’S REPORT
Please note that the Coroner’s report on the death of an operator of a drilling machine during quarry operations has been released.
This report is available on the CMPA website:
www.cmpavic.asn.au and is also enclosed with this newsletter.
INCIDENT REPORTS
FLUID INJECTION INDICENT
A maintenance technician was attempting to release grease pressure from a crawler track adjuster on an excavator. The technician was struck in the arms, face and chest with the pressurised grease.
CRANE DRIVER INJURED WHEN RIG TOPPLES
A crane driver and members of the public were hurt when a 200 tonne rig collapsed on a construction site.
FAILURE OF A QUICK HITCH MECHANISM—QLD
A person was seriously injured while working in a trench when a bucket detached from an excavator and fell into the trench striking the person.
PROSECUTION OF A MINE WORKER
A former mine worker pleaded guilty to the charges that he had used an electronic tagging system to falsely show that he and two other workers were in a safe working area during blasting time when in fact they were in the blasting area.
RIG COMPRESSOR FIRE
A Longhole Drill Operator was operating a rig when the compressor on the rig caught fire.
DRILL RIG ROLLOVERS
Two drill rig roll-overs occurred recently in quarries. On both occasions the drill rig was being trammed on uneven uncompacted ground with the mast upright and with the mast positioned to one side of the machine; and, detailed ground preparation procedures were not in place.
TRUCK ROLLOVER
A 50 tonne truck rolled over after running into a stockpile of rock on a bench in a quarry.
FLYROCK GENERATED BY PENETRATING CONE FRACTURE CARTRIDGES – QLD
A flyrock incident was reported when using a penetrating cone fracture “PCF” cartridge to break oversize rocks on the surface near the workshop and cribroom area.
DOZER COMES OFF BACK OF TRUCK
Three people were lucky to survive when a dozer fell off the back of the truck they were following.
EXCAVATION AROUND ELECTRICAL CABLES
Near miss—excavation around electrical cables—Contractor failed to follow procedures and did not isolate the power supply. Improvement notice issued.
QUEENSLAND INCIDENTS:
- Slab of coal came off face striking worker
- A rear dump truck veered off a haul road into a windrow after a tyre blew out
- A fire occurred on a rear dump truck when a hydraulic hose burst and sprayed oil on the hot turbo charger
- A dozer was pushing a track down into an open pit when a section of the highwall approx 30m in length and 12m high slumped, covering about 3/4 of the machine
- A rear dump truck rolled onto its side after hitting the end wall on a straight section of road on a ramp that had recently been watered
- An operator of a rear dump truck lost control whilst going down a ramp that had recently been watered and rammed into a roadside berm
- A front end loader was digging a stockpile when the material rolled onto the loader, breaking the windscreen and covering the operator up to his waist.
Orange Ponders Asbestos Removal
An OHS consultant has visited a site in Orange, NSW, to determine how to safely remove and dispose of more than 100,000 tonnes of asbestos, which was discovered in a rock seam by a local geologist “by chance” during road works, Orange City Council Director of technical services Michael Ryan has confirmed.
He said 50 council workers who were potentially exposed would undergo lung function tests and chest X-Rays on Dec 7, when a WorkCover ‘lung bus’ would visit the area. It is expected the workers will be monitored every 12 months for any signs of asbestos-related disease.
“The asbestos was found at an industrial estate that adjoined a quarry, north of the city. The workers were involved in leveling the site,” Ryan told OHN. “Because the asbestos is mixed up with rock it doesn’t fit the normal criteria under the regs. Options for its disposal include locking it in with concrete slabs and burying it under roads,where it could not be disturbed.”
A spokesperson for NSW WorkCover said inspectors visited the site to investigate the incident. “As soon as the council found out what it was, they did all the right things,” he said. “We were very happy with their response.”
It is understood the location of the asbestos was not identified on council or EPA geological maps of the area. The council has engaged Noel Arnold and Associates to advise on asbestos safety and disposal recommendations.
Reprinted courtesy of Occupational Health News, published by Thomson, phone: 03 9205 0681
You must be logged in to post a comment Login