TEDGE: The Real Cutting Edge for Sales Loaders and more
TEJ PANESAR, Director of Operations for TSP Group of Companies reports on the advancements of the cutting edge.
LARGE investments in Wheeled Sales Loaders have a very simple yet important purpose – push the bucket into the stock pile, pick and load the material. It is the cutting edge that protects the front end lip of the bucket and is the sacrificial component that needs frequent replacement.
Despite good advancement in design of machines, operator cabins, ergonomics, engines, transmissions, drive trains, linkage and to some extent the buckets, the humble cutting edge – a regular replacement product which has a large impact on the machine efficiency as a whole has had very limited advancement.
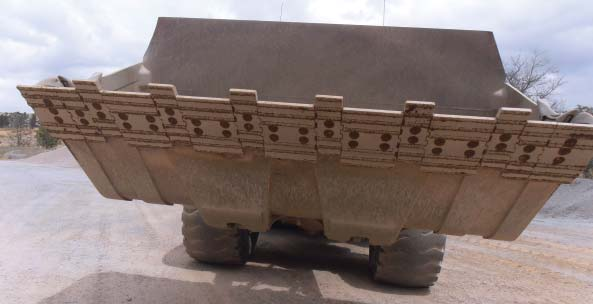
TRADITIONAL CUTTING EDGES
Let’s look at some of the disadvantages of the traditional cutting edge, which the industry has just learnt to live with.
Wastage
With the holes in the lip base edge being about 4” to 4.5” away from the front of the bucket and the cutting edge protrusion being 3” to 3.5”, the cutting edge width has to be around 15”, which is around the most popular width. Of this the maximum theoretical usable material is around 6” (40%). In real life the useful life is only about 30% -35%. This means that almost 2/3rd of the cutting edge material invested in has been wasted. The quandary is that more quality you build in the traditional cutting edge, the higher the cost, thus higher the loss.
Thick Edges
The popular solution to avoid frequent changes in cutting edges of low life is to put a thicker cutting edge e.g. a 50mm edge instead of a 40mm edge. While it appears to a simple logical solution a little look into the impact on its actual impact and equipment performance would read very differently.
Let me explain:
50 mm is 25% more than 40mm. Thus the bucket now has 25% more material at its further most part away from the equipment.
As an example let us take a 3.4m wide bucket which is quite popular in our quarries. A 40mm edge 15” wide cutting edge on a 3.4m wide bucket would weigh approx 400kg and at 50mm thickness it would weigh about 500kg. By putting this extra 100kg at the tip of the bucket the following disadvantages creep in.
- There is 100kg less material per bucket, to stay within equipment design parameters;
- With the bucket being filled to cubic capacity, this extra weight eats into the safety factor built into machine stability. 100kg x 3m from the front tyres causes and extra 300kg load;
- Thicker edge is more difficult to push into a stock pile than a thinner edge;
- The above causes an increase in load on the engine, transmission, drive train ect;
- Fuel consumption also increases.
OH&S: Challenges
- Handling a 400kg edge (a little less with the 3 piece and 4 piece options) requires material handling equipment and tackles for safe handling and is an extra expense and exposure to the business.
- It would need additional manpower assistance and substantial time.
- Need to necessarily replace cutting edges in a controlled workshop environment far away from where the machine is working.
Uneven Wear
Depending on various site conditions, material, stockpile & how it is approached and the operator factor, there is uneven wear on the edges which further reduces the useful life of cutting edges.
Bowed bucket lips
Many buckets bow over time and make it impractical to bolt on a standard cutting edge and frequent re-tightening of bolts is required.
Far too many holes in lips
With so many holes in the lip to allow for multi optional fit of cutting edges or bolt on tooths and adaptors, a heavy cutting edge causes lips to crack.
Too many Edges to stock
With so many brands and sizes of machines and buckets each having so many different bolt-hole patterns just creates a challenge to the customer in managing cutting edges stock.
Despite so much money locked in inventory, the non availability of the specific cutting edge causes machine down time, so more investment goes into stock and back-up stock.
Manufacturing
With the traditional cutting edges being a rather straight forward design, just about anyone now makes it and many a times, the bolt-hole spacing and alignment has had problems and on site fixes become necessary.
Production limitation
With the large size and weight of the cutting edges, the traditional popular method of production is to just cut it from a plate of steel.
It’s important to look at the total cost of cutting edges, keeping the above factors in mind. Unfortunately, over the years insignificant improvements have been made in their design which is very inefficient even in its current form. Improvements over the years have ranged from a single bevel to a double bevel reversible and from 1 piece to 3 or 4 pieces. It has still not solved the problem of the majority of the expensive cutting edges being wasted.
What we really need is a reasonably priced improved design. To this important cause we introduce a revolutionary cutting edge named TEDGE. It is so named to rhyme with cutting edge & my name Tej.
TEDGE, a revolutionary cutting edge which smartly dissects the whole cutting edge into small manageable size special design pieces with three holes and a locating system that allow the cutting edge to take a tooth pattern and still remain a flat edge a the same time; a unique combination.
TEDGE CUTTING EDGES
Let us compare TEDGE on all of the above issues with traditional cutting edges.
Wastage
No wastage. TEDGE has three bolt-holes per piece. This allows it to be moved forward as it wears thus increasing the useful life as a cutting edge. Furthermore the left over piece is about the size of a side cutter and can be used to get virtually 100% usage.
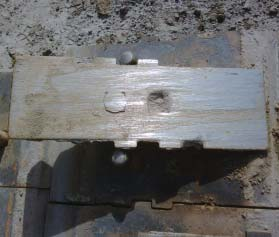
Thick Edges
Thinner TEDGE. Since the bolt-hole design allows for greater uses of wear material one can go with a thinner TEDGE.
- More material per bucket load to stay within equipment design parameters:
- With the bucket being filled to cubic capacity, the machine stability is not compromised:
- Thinner edge is less difficult to push into a stock pile than a thick edge;
- The above causes decreased load on the engine, transmission, drive train, ect; and
- Fuel consumption also decreases
OH&S: OH&S Friendly.
- Handling a 35mm 20kg TEDGE does not necessarily require material handling equipment and tackles for safe handling and is a reduced expense and exposure to the business.
- It would not need additional manpower assistance and substantial time.
- No need to necessarily replace cutting edges in a controlled workshop environment far away from where the machine is working. It can also be done on site by trained operator.
Uneven Wear
Easy Fix. Depending on various site conditions, material, stockpile & how it is approached and the operator factor, there is uneven wear on the edges, but TEDGE can be moved front and back, left or right, from centre to ends and also rotated 180 degrees in its own place, which further increases the useful life of cutting edges.
Bowed bucket lips
So what. Many buckets are bowed over time and make it impractical to bolt on a cutting edge and frequent re-tightening of bolts is required. TEDGE being of small width can fit around the bow and let you continue to work till needed to stop for full repairs.
Far too many holes in lips
No issues with TEDGE. With so many holes in the lip to allow for multi optional fit of cutting edges or bolt on tooths and adaptors, a heavy cutting edge causes lips to crack. However, TEDGE uses only one hole per TEDGE in the lip, thus does not weaken the lip.
Too many edges to stock
Hardly any stock. Despite so many brands and sizes of machines and buckets no such money locked in inventory and back-up stock by using TEDGE. The one or more sizes of TEDGE generally cover all sales Loaders on site. It therefore reduces machine down time. When less investment goes into stock it improves cash flow and profit.
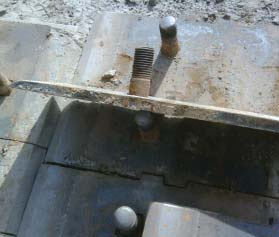
Manufacturing
Error friendly. TEDGE allows for a slight error in bolt-hole misalignment.
Production Limitation
What limitation! TEDGE can be forged, cast or plate cut. In addition TEDGE offers the following advantages:
- TEDGE is the only cutting edge that offers the combined benefits of a tooth system and a flat edge at the same time
- The TEDGE style flat-tooth configuration allows for easy penetration thus potentially saving fuel and reducing engine, transmission, drive train, linkage and tyre wear.
- With a TEDGE style flat-tooth configuration the forward movement sweeps the ground better to reduce need for back-blading.
- By cleaning the work are in the forward stroke, TEDGE allows the machine tyres to roll on cleaner ground thus reducing the chances of damage and/or accelerated wear otherwise caused by loose material.
- The approach to the stock pile by coming flat on the ground as opposed to an angled approach for penetration will virtually eliminate cutting edge scalloping.
TEDGE was presented to the Victorian quarry group at their official technical night in Melbourne and major quarry operators have started to move over to TEDGE and reap the benefits.
TEDGE has now been successfully deployed in various material applications and on various brands of loaders like CAT, Komatsu, Volvo, Doosan and Hyundai. It is one single improvement that will ultimately revolutionise the way cutting edges were ever looked upon and the quarry industry will benefit vastly from this change over to TEDGE and will possibly become an OEM product from sales loader suppliers.
Proverbially speaking, in the quarry sales loader application:
The best thing since sliced bread is…..the sliced edge….TEDGE.
For more information contact TSP Group on 0421 380 700.
You must be logged in to post a comment Login