The Effects of Accelerated Blast Timing on Primary Crusher Throughput
Quarries worldwide have experienced benefits using electronic initiation systems with improved and novel initiation sequencing. Unitronic Electronic Detonator Trial at E.B.Mawson & Sons Pty Ltd – Lake Cooper, reported by FRANK SANTORO and REZA GHAEMI of Orica Quarry Services Victoria.
VICTORIAN regional quarry company and CMPA Member, E.B.Mawson & Sons Pty Ltd and leading supplier Orica Quarry Services, recently trialed an electronic initiation system using accelerated timing at Lake Cooper quarry, which delivered significant crusher throughput increase and a reduction in crusher blockages.
The aim of the trial was to determine if fragmentation and production improvements could be achieved in the quarry that had been affected by oversize in the dolerite muck-pile.
In early 2010, a 45,000 tonne trial blast was divided into two sections and fired at the same time, the first section initiated by Unitronic electronic detonators and the second by a conventional non-electric initiation system (Exel).
Both sections had crusher data and visual differences recorded while the excavation process was completed separately to record production data and allow analysis of primary crusher throughput.
The outcome included improved rock fragmentation achieved from accelerated initiation timing using Unitronic detonators. Primary crusher throughput was 18.5 percent higher and crusher blockages were reduced by 32 percent compared to the Exel section.
Both the quarry manager and supervisor reckoned the trial delivered notable and measurable gains when compared to standard nonelectric blasting.
Orica Quarry Services’ ‘Rock on Ground’ program includes design and mark out of the blast, supply of initiating systems, mixing and loading of bulk products, tying up and firing the shot.
BLAST DESIGN
The blast was designed using three rows and divided into two approximately equal sections using the blast parameters listed below:
Blasthole Diameter (mm) – 89
Blasthole Angle – Front row (degrees) – 25
Blasthole Angle – Back row (degrees) – 15
Bench Height (m) – 15
Front Row Burden (m) – 2.8
Burden (m) – 2.8
Spacing (m) – 3.0
Sub-drill (m) – 0.8
Stemming (m) – 2.2
Pattern – Staggered
Powder Factor (kg/m3) – 0.86
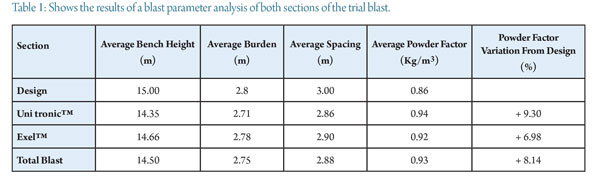
All down lines and surface delays used for the non-electric section are listed below. The electronic section used an accelerated initiation sequence delivered by Unitronic programmable detonators, designed to promote additional rock fracture.
Control Row Delay (ms) – 17
Echelon Delay (ms) – 42
Bottom In-hole Delay (ms) – 400
Top In-hole Delay (ms) – 425
BLAST RESULTS
Following the initial post blast inspection, a transition zone from the Exel initiated section to Unitronic initiated section was evident. Refer to Figure 1.
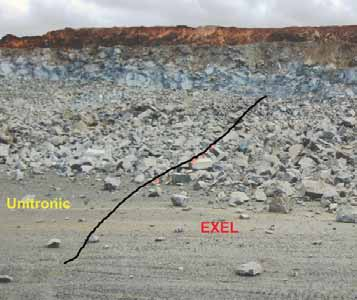
sections of the blast
All production data (truck loading, crusher throughput and blockages) was recorded. There was no specific effort made to record oversize production from this shot, however rock breaker visits are recorded as a number of subsequent Unitronic shots have been fired and excavated for comparative purposes.
ACTUAL BLAST PARAMETERS
To ensure any difference in blast results from either section of the blast can be attributed solely to the Unitronic initiation system, an analysis of the actual blast parameters was conducted. This ensures any bias due to blast parameters would be highlighted and considered during evaluation.
The shot comprised of 122 blast holes, the Unitronic section consisted of 62 blast holes and the Exel section 60 blast holes.
PRODUCTION DATA
Crusher Throughput
The total tonnes crushed by the primary crusher along with total operating hours were recorded each day. As the quarry needed to produce different material from different areas of the pit each day, it was not possible to concentrate just on production from the trial area alone. This meant data recorded was only for the timeframe when the quarry was working in the trial site. Referring to Figure 2, an improvement in the back of muck pile is evident.
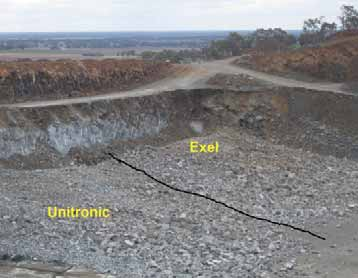
An average crusher throughput of 191 tph was calculated from the Exel section of the blast and 234 tph from the Unitronic end – equating to an 18.3 percent improvement in primary crusher throughput.
Crusher Blockages
Data also captured the number of blockages per day and production lost time per blockage.
Figure 3 is a graphical analysis of raw data captured during production of the total trial blast area. The (total blast) average time required to recover a blockage in the primary crusher was approximately 12 minutes.
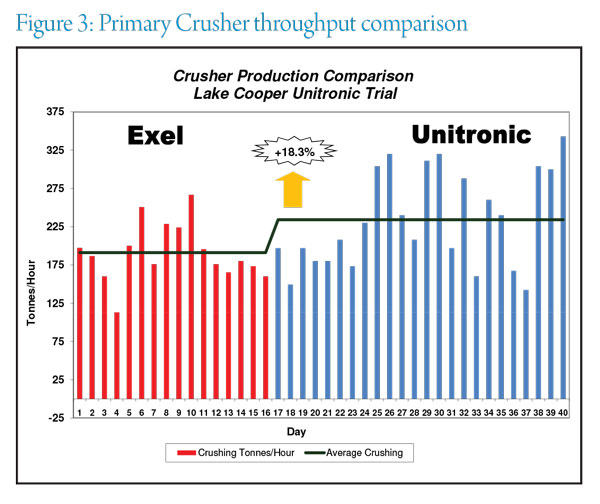
Considering standardisation, per 1,000 tonnes of production, it was calculated that production lost time due to blockages was reduced from 3.66 blockages/1,000 tonnes in the Exel section, to 2.47 blockages/1,000 tonnes in the Unitronic section of the trial blast.
Converting this to availability of plant, it means that 44 minutes/1,000 tonnes was lost recovering blockages compared to only 29 minutes/1,000 tonnes lost crushing the electronically blasted portion of the blast. This equates to a savings in lost crushing time of 32.5 percent.
With an overall average blockage recovery time of 12 minutes, the primary crusher operator also made mention that there were fewer blockages from the Unitronic component of the blast and that they were notably easier to recover.
From the actual operator data, it was found that the time taken to recover a blockage from the Exel section of the blast was almost twice that of a Unitronic blockage.
Over the course of five full Unitronic blasts fired at the Lake Cooper quarry using accelerated initiation, it was observed that the remnant oversize material encountered contained greater fracturing making both blockage recovery and on-bench oversize management much easier and faster.
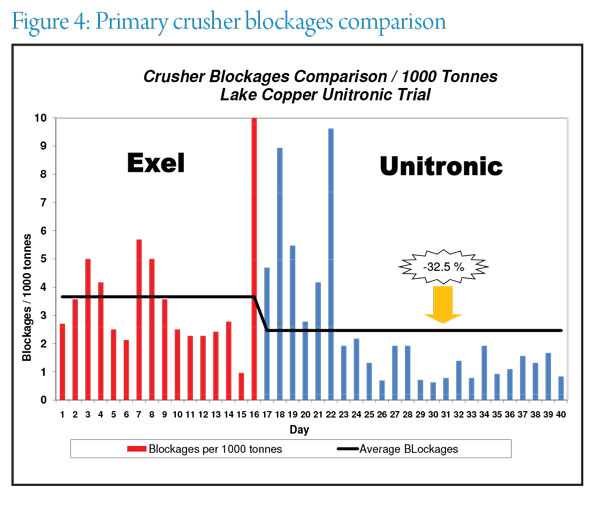
Figure 4 shows two significant peaks captured during the early excavation of the Unitronic blasted material – this is the oversize encountered from the top section of the Unitronic blast, associated with the stemming zone and some heavy burdens in this area.
Figure 5 illustrates the side, or excavation profile of the Unitronic section, showing improved and more uniform fragmentation in the body of the blast and also highlights the oversize material coming from the top portion or stemming area of the blast.
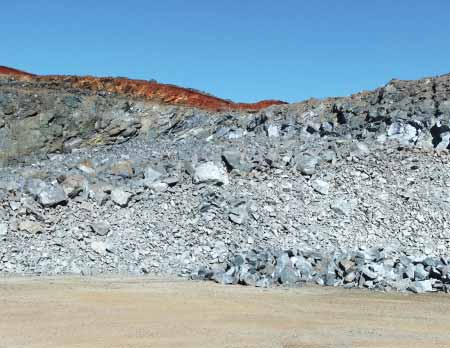
BENEFITS TO QUARRY PRODUCTION
Primary Crusher throughput increased
Unitronic blasting using accelerated initiation timing has shown a notable improvement in the primary crushing process with throughput increased 18.3 percent, from 191 tph to 234 tph.
This result was further calculated to show accelerated electronic timing delivered an additional 28,372 tonnes of primary crusher throughput with no additional operating days compared to a typical non-electric system. This means that the time taken to crush or process 100,000 tonnes from a standard non-electric blast, would deliver 128,372 tonnes processed from an electronically fired blast in the equivalent time. This equates to a 28.3 percent improvement in overall primary crusher throughput.
Oversize Rock reduced
The use of Uni tronicτМ blasting with accelerated timing also saw a reduction in the use of rock breakers.
Baseline data captured in 2009 calculated a value of 2.09 rock breaker hours per 1,000 tonnes of product throughput, while 2010 data recording 1.43 rock-breaker hours per 1,000 tonnes of product throughput. This equates to an overall reduction of 31.6 percent in rock-breaker hours during the electronic trial period.
Anecdotal Comments
The benefits to quarry productivity are not just limited to the analysis of production data. This direct comparative trial is a first at Lake Cooper Quarry and targeted the key area of primary crusher production.
Both the Quarry Manager, Adrian Bull and Supervisor, Maurice Kerrins, also offered comments regarding additional benefits noted from the Unitronic trial.
Loading efficiency in the electronic blast section was improved with use of a second dump truck to haul oversize eliminated, leading to savings in fuel and operating costs.
There was a reduction in expenditure of ground engaging tools, wear parts and crusher maintenance. Quantifying this particular benefit accurately is always a challenge and can only occur over longer periods of time.
Unitronic electronic blasting at Lake Cooper commenced mid 2009 and to date approximately 158,000 tonnes of material has been blasted using this technology, which is generally applied to the harder areas of the quarry.
And finally, quarry staff noted an improvement in floor control during excavation of the blasted rock pile.
CONCLUSION
The result of this trial has identified significant benefits by using the latest blasting technologies.
This site is not only seeing a productivity improvement, but most importantly a financial benefit.
New blasting technology can be applied to many sites, with key elements being capturing data, recording outcomes and completing accurate analyses. This is the only way to determine if the application of new technology delivers benefits to your site.
Note: A full version of the technical results of the Unitronic trial is available by contacting your local Orica representative.
You must be logged in to post a comment Login