Tracking Conveyor Belts
Conveyors are integral to the operation of many processing plants, and as such need to be well maintained. One area that requires attention is the tracking of conveyor belts as reported by NEIL KINDER, Kinder & Co.
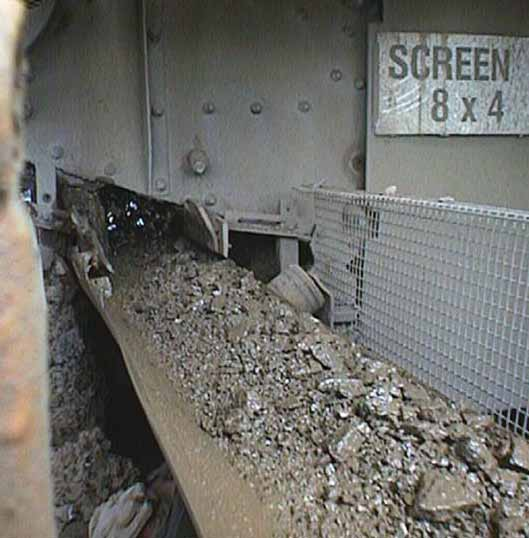
TRACKING (training) is defined as the procedure required to make the conveyor belt run ‘true’ under all operating conditions. A conveyor belt must run ‘true’ to avoid material spillage at the transfer points. A conveyor belt must run ‘true’ to avoid damage to the edge of the conveyor belt.
RULE 1
The basic and primary rule of tracking a conveyor belt is simply ‘the belt moves towards that end of the roller it contact first.’ The conveyor belt will travel where directed if it has been manufactured, slit and spliced correctly.
RULE 2
The conveyor structure must be ‘true’ (relative to the centre line) and level (side to side).
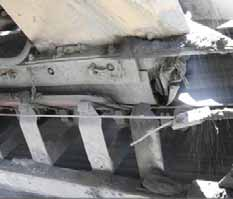
RULE 3
Belt tension must be great enough to:
- Prevent slippage between the drive pulley and the belt
- Force the belt to conform to the crown on the crowned pulleys, if they are used.
The belt should not be over-tensioned. Consult your belt manufacturer.
RULE 4
Cleanliness is essential to good belt tracking. Foreign matter creates a new and changing surface to rollers and pulley faces – adversely affecting tracking.
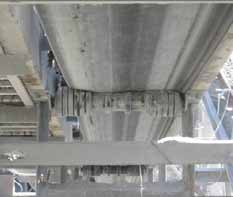
RULE 5
Conveyor belts must be straight and ends must be squared and spliced properly.
RULE 6
The normal sequence of training is to start with the return stand working toward the tail pulley, following with the top side in the direction of belt travel. Start with the belt empty. After tracking is completed, run the belt with a full load and re-check tracking.
RULE 7
Tracking adjustment should be spread over some length of the belt preceding the region of trouble. Permit the belt to run for at least three full revolutions after each idler has been adjusted to determine if additional adjustment is required. If the belt has over corrected it should be restored by moving back the same idler and not by shifting additional idlers or rollers.
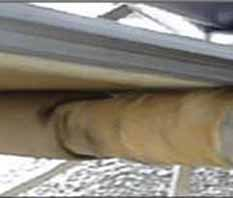
COMMON CAUSES OF BELT MISALIGNMENT
- Sunken or not level foundations
- Driving and idler pulleys not normal to the conveyor centre line and not parallel with each other
- Seized or out of round rollers
- Transverse forces applied to the belt by items such as over tight or angled belt scrapers
- Material build up on the pulleys, belt or rollers
- Damaged, twisted and/or missing conveyor idler frames
- Uneven placement of load on the belt or the belt being loaded off centre
- Uneven skirting pressure
- Worn pulley faces, pulley lagging unevenly worn or pulley shaft locking elements worn
- Trough and return idlers not installed at right angles to the axial centre line and therefore the belt not making proper contact with the rollers
- Trough idlers installed back to front with the lead roller not leading
- Offset trough idlers being used on reversing conveyors rather than in-line idlers
- Out of round or seized rollers giving the belt contact forces asymmetric to the centre line
- Poor belt quality with the weave/fabric asymmetric to the centre line
- Belting of a different manufacture in the same length
- Mechanical fasteners not installed square
- Conveyor rollers of various diameters installed
- Poor workmanship with belt splicing/slitting/ends squaring, this includes localised edge repairs with associated tension differences
- Transition idlers not installed or unevenly adjusted
- Poor quality pulley manufacture with the diameter not symmetrical to the centre line of the belt (pulley faces may be worn)
- Excessive tensioning of the belt preventing all of the idlers from helping to direct the belt
- Under tensioning of the belt which restricts the pulleys from controlling the belt, this also applies to all pulleys including take ups
- Uneven or misaligned pulley take-up carriage forces
- The belt hotter on one side than the other, for example near a furnace
- Traveling trippers and shuttle not running true
- One side of the belt running wet
- Extraneous articles fouling the conveyor belt
- Belt too stiff for the idler width or trough angle, therefore not allowing idlers to direct the belt
- Return idler spacing too great to direct the belt
- Existing self-aligning idlers worn out, seized, or locked into position
- Existing self-aligning idlers installed incorrectly or in wrong location
- Incorrect belt storage which has caused the belt to warp or bow
- Crosswinds
You must be logged in to post a comment Login