WORKING AT HEIGHTS
John Mitas, Operations Manger, DPI
The 15th CMPA General Meeting was held at William Adams, Clayton, on Friday 26th of November.
The meeting encompassed a discussion of the contentious topic of quarry manager’s accreditation, and the Department of Primary Industries presentation of the OHS (Working at Heights) Regulations.
Occupational Health and Safety (Prevention of Falls) Regulations 2003
- Came into operation 31st March 2004
- Employer’s duty to identify tasks involving a fall hazard
- Employer’s duty to undertake risk assessment
- Employer’s duty to control the risk
- Hierarchy of control of risk
- Emergency procedures
- Information, instruction and training
- Employee duties
Following is the transcript of the presentation on ‘Working at Heights,’ as delivered on the evening by Mr John Mitas, Operations Manager, DPI.
“…Identify all those tasks that involve working at heights, that’s the first job that you have to do. Once you’ve done that you need to assess the sort of risks that your people are involved in with those sort of tasks, and you need to control them. We’ll talk about some of the controls that you can have in place. There is a hierarchy of controls…”
Basically with the hierarchy of controls, the first option is the best in terms of controlling the hazard. If you can do your job from the ground, and you don’t have to be working at heights, then that is the best control you can have in place.
If you have stockpiles, and you can limit their height and actually tip on the ground instead of driving up the stockpile to tip – then that is the best control you can have in place. If you have the room, and you want to make sure your trucks aren’t going to fall over the edges and injure or kill your people – start tipping on the ground.
If you have work to do at heights, for example with a screen or a crusher, you can just lift it up, put it down, and do your work on the ground. Work on the ground is the best control. If you can’t work on the ground, then the next best option is to set up some permanent platforms and ladders to provide access to the area.
If you have a screen or a crusher that’s up off the ground, put a catwalk up to it and a platform around it with handrails. This is also a good control as long as your people are working on a steady, solid platform.That is the next best control.
If the use of catwalks and platforms doesn’t work, then you need to have a device that can lift you up and put you down safely, like a cherry picker, or some other approved way of lifting people up. Front-end loaders are not an approved way of lifting people up! You need to use approved equipment that has all the safety controls in place for you to do your job.
I have some photos that will imprint the controls in your brain. The next control, if you can’t implement any of those previously mentioned, and somebody has to be working at a dangerous location is to have a system in place, where if he trips and falls off he’s not going to fall all the way to the ground, where he is captured, and he is safe. It must be a harness that is approved and is not going to break the fellow’s back if he falls. That is the next best control.
The last option, and it’s possibly not the best option really, is using ladders to get to situations. You are very limited in what you can do on a ladder. The ladder has to be fixed correctly so that it doesn’t slip. You need to have a hand on the ladder and therefore you can use only one hand, and you can’t really overt-stretch too much or else you’re going to fall off. It is therefore a very limited application using ladders to overcome height problems.
Working on the ground is actually the best way you can deal with the hazard. However, that is not the end of the day, you have sorted out their working at heights problem, but you also have to work out the hazards of doing the job, and that is what this picture is trying to demonstrate. You might be on the ground, but there are other hazards that are lurking around that could bite your head off.
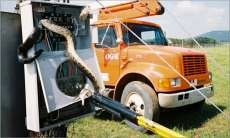
Think about the job on the ground, don’t think “I’m on the ground now – now I’m safe,” because there are lots of other hazards present.
This is a good example of a platform that you can you use to get up to your crushers, and you can actually work on the things, up high, safely.
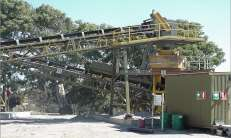
You also have access to platforms there which are in compliance with the standards, you have good handrails, there are kick rails in place, there are also intermediate rails. There are standards about these platforms, and you need to comply with the requirements.
Here is an example of a control mechanism that is not adequate really, you’re working at heights, people can just fall off, no kick rails, tripping hazards, no intermediate rail, there is a bit of trip wire there that looks like clothes-line wire.
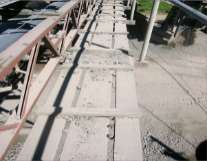
You’re not even sure that it’s working, to me it doesn’t even look like there is any tension on it. They tend to be dealing with the working at heights issue, but not very well. You still have some big problems there.
Question: Just mentioning the trip wire – there is a bit of confusion within the industry about whether it has to be a particular colour.
Answer: There is a Standard again that talks about trip wires and tensioning etc, but I have no particular colour requirement. I have seen a lot of yellow-coated trip wires, it has to be visible in all light conditions. Its good to have a colour that’s bright in the dark, so people can see where it is. You have to use it in emergencies, so you have to be able to see it, and it has to be accessible. Just a colour that is pretty visible in dark conditions, like yellow or red. Yellow is probably better because there is already a lot of other red coloured objects around the place to indicate danger.
Question: I know it doesn’t say anything in the Australian Standard, but I’ve been told it does mention the colour red in some other Standard.
Answer: The idea is to use a colour that’s got visibility in conditions that are not ideal. I’ve seen yellow and I’ve seen red.
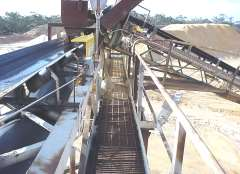
This is another example of – you have access, and you have a catwalk, but you’re creating other hazards. You are probably ok in terms of working at heights on the platform, but in terms of getting across there, you almost have to crawl on your belly to get under the conveyor. If you are forcing people to be unsafe by jumping across a conveyor, then it isn’t a good design.
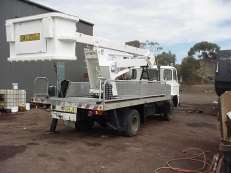
This is a good set of equipment. As I mentioned before, for getting to those areas that you really haven’t got any other way of getting to—and you’re not using a front end loader or any other way that could cause you some problems. This is an approved piece of equipment for working at heights. If you haven’t got one it may be a good idea to plan your maintenance and get one.
As I mentioned before, tipping off stockpiles is working at heights. If you have a stockpile that’s 20 – 30 metres high, you need to be able to go through and look at your controls.
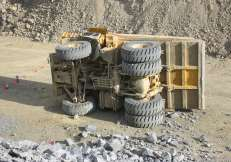
This is one of the most prominent incidences that occur in our industry. Very common, 2 or 3 a year, and basically you’ve got to be lucky to survive them.
We had an occurrence that happened 2 – 3 months ago, a driver actually drove onto a stockpile, not very high, and just tipped over. He wasn’t wearing his seatbelt, and he actually fell through the emergency exit of the truck. He fell through it, about 3 metres. He landed on the exhaust pipe and burnt his legs.
That guy could have walked away if he’d had a seatbelt on. He could have walked away, no injury, no scratch, no drama. So it’s another one that really, you’ve got to have some other controls in place that can protect you after an incident happens.
To be continued in Issue 20 of the CMPA News
You must be logged in to post a comment Login