City Circle Group – Decarbonisation of our industry
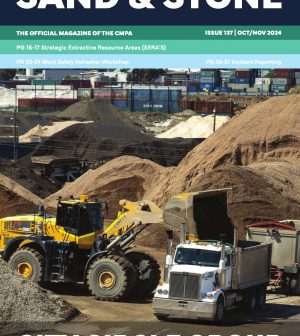
MATT SKIDMORE, General Manager of City Circle Group
CMPA materials are required in almost every industry across our state in order to enable development and progression of our society.
While the products that we produce largely have not materially changed in centuries the way in which we complete our works and the processes involved are ever evolving. This is both for the furthering of our own operations but largely to ensure that we are in lock step with the demands of society and the direction in which it is heading.
Decarbonisation and climate change, while buzz words for some are now at the core of our society direction and what started as a novelty is now a reality that we as producers and a wider industry need to accept and adapt to ensure that we are contributing to society and its ambitions as well as
ensuring the viability of our own operations.
Emissions and decarbonisation as previously mentioned are well known of as a concept however it is rapidly evolving into a “pay to play” piece of the construction industry.
The desire for decarbonisation has in large been driven by private capital to this point with people investing their money with a “green” conscience. This investment has provided opportunity for some operators to be seen as progressive while the remainder of operators were able to continue their operations uninhibited due to supply for building materials in our state largely outstripping demand. However, with legislation from government both federal, state and local ramping up as we close in on mandated targets, we as an industry will be required to invest and innovate within our operations to help realise these goals or risk being left behind and drastically reducing the avenues of sale of our material.
Decarbonisation for a produce essentially comes back to how much CO2 we emit to produce our materials. This draws back to 3 core focuses being inputs, efficiency and location or distributions. Elements of these are largely within our control and other elements require collaboration in order for us to contribute to the objectives.
City Circle Group has been a Voting Member of the CMPA since 2013 with Matt Skidmore currently on the Management Committee.
City Circle Group are passionate about decarbonisation and support the CMPA, especially for the work they have done to reduce EPA financial assurances on construction demolition waste and recycling sites.
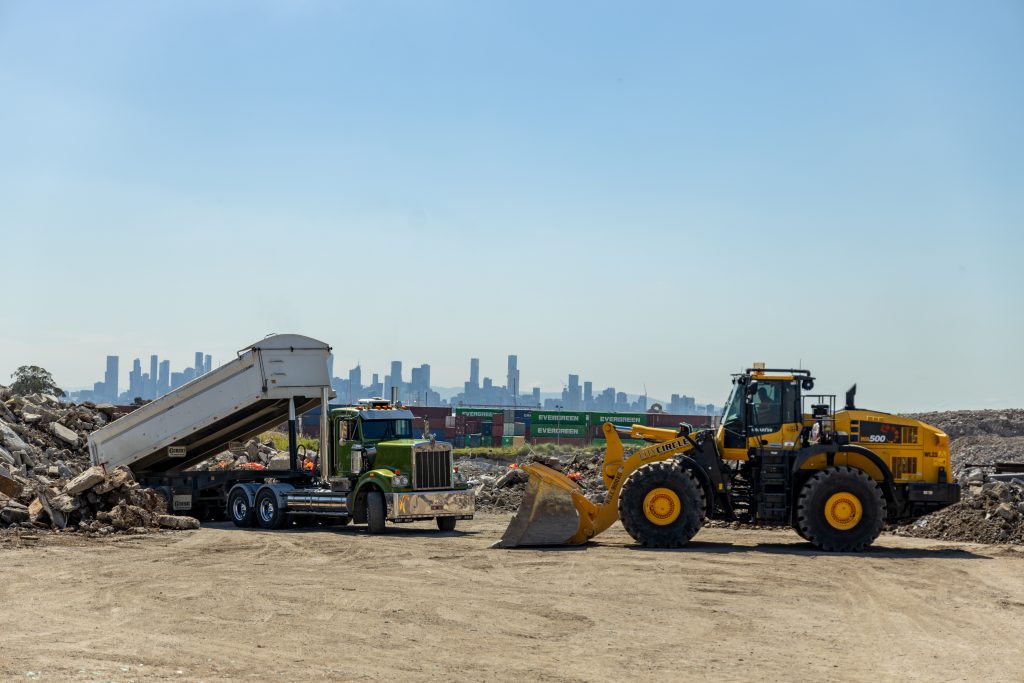
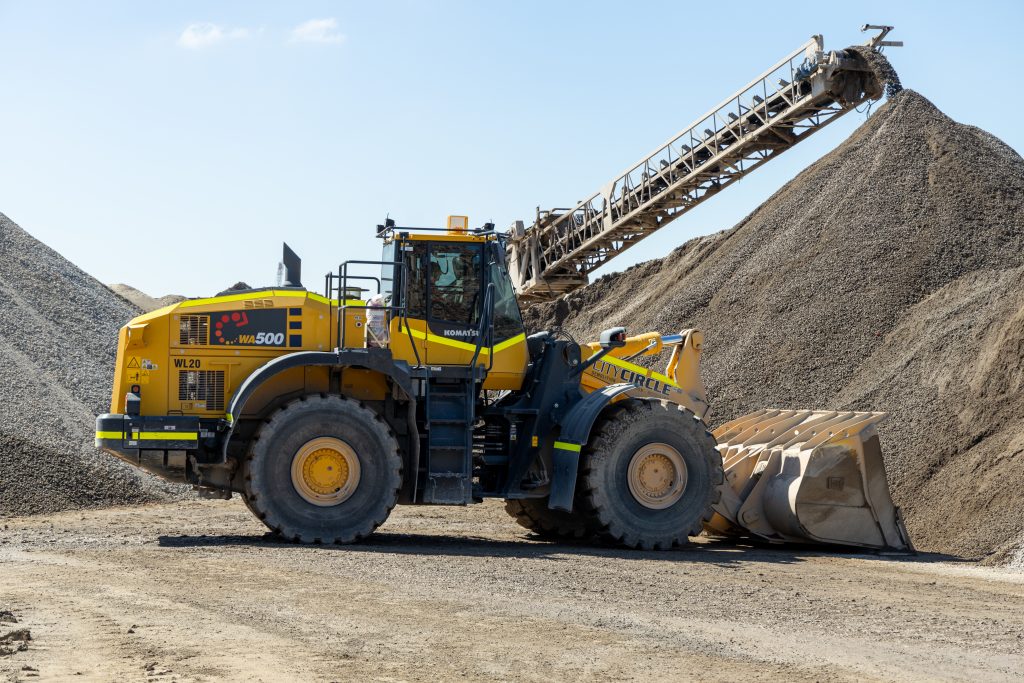
Our inputs are broad ranging but specifically relate to fuels and machinery that we use to power our operation and the materials that we input into that operation. Ultimately these two items combined with the rate of material being produced will determine a products Environmental Product Declaration (EPD). An EPD will become common place for all products and will give the end consumer the information they need to achieve their desired outcomes and those where there is an inability to offset emissions at the production level will incur a cost to the end consumer in the form of offset purchasing.
When we look at inputs it relates ultimately to the fuels that we burn to create the energy to run our operations and the materials that we are processing. Fossil fuels in the form of coal powered electricity and diesel-powered generators create larger volumes of CO2 when they are produced.
At City Circle we have moved to eliminate diesel generators and focus on mains power as our primary source of power. This gave us a two-fold effect of aiding the production capacity of our sites and lowering the emissions. We then installed solar panels to again offset a small amount
of the emissions. The next input was our mobile plant, the equipment that we use to facilitate the process. Nominally wheel loaders and excavators fueled with diesel. We have chosen to move towards tier 4 engines that again burn more efficiently to a conventional diesel engine and prioritize fuel efficiency in our purchasing decision making. All of these inputs work to narrowly lower the carbon emissions and lower our EPD, however meaningful and substantial reductions will need more drastic action.
The other input is the actual material that we are feeding into our plants. Many CMPA members will be processing virgin material such as sand and rock. Recycling companies have a natural advantage with the material being treated as a waste thus a large portion of the processing emissions attributed to its previous life cycle. Currently the quality of materials produced are of exemplary quality and there has been a push to substitute waste materials into products to “offset” the emissions of the natural product. This method in many cases will deliver short term solutions but deliver longer term complications. When virgin basalt and sand are batched into concrete, the material has infinite life cycles. The product can be crushed and used in road base or even separated as reused in its original form. The more waste that is hidden in hi grade products the more we limit its reuse.
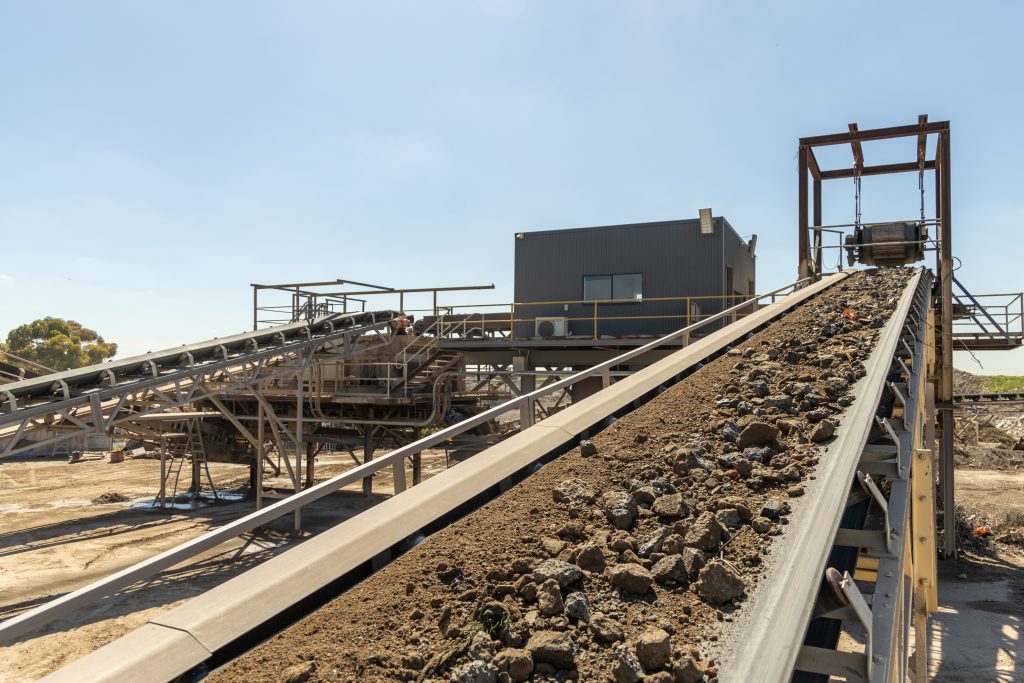
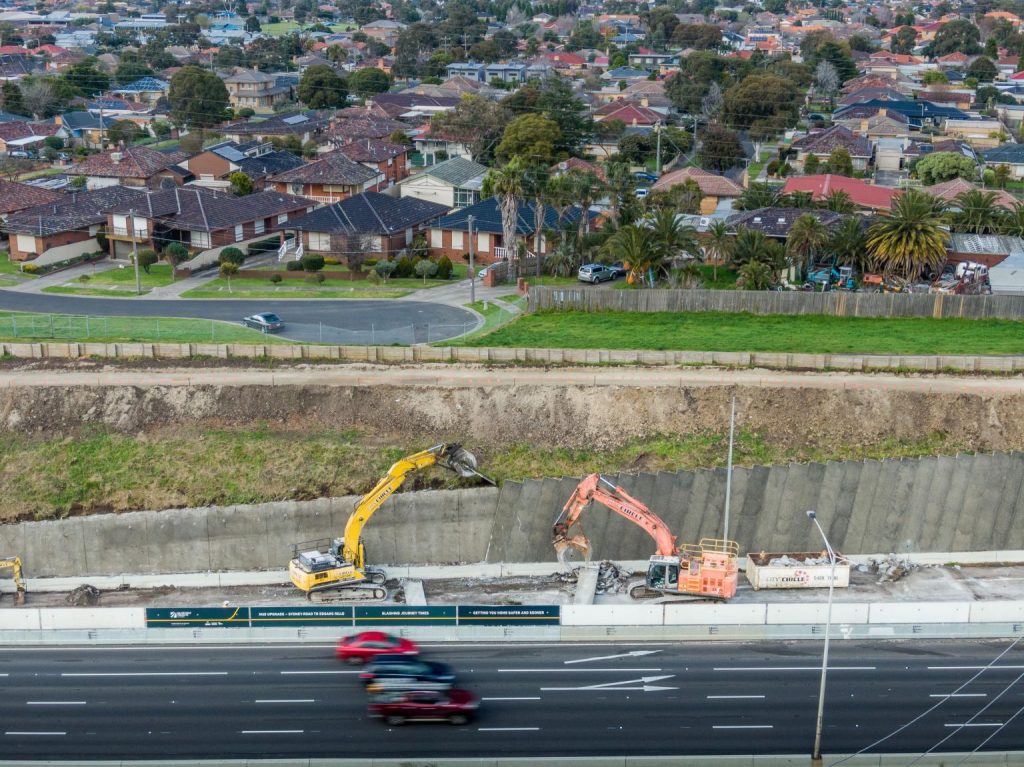
Alternative fuel technology in mobile plant is not at a price point or a stage where there can be confidence using it as an alternative to diesel powered equipment and that ultimately leads us with two major items that will require collaboration with government if we are going to be able to play our part in the push to net zero. Power inputs and Material Delivery.
Mains power is continuing to become greener with the governments push towards renewables in favor of the traditional coal and gas fired generation. This will materially impact our footprints. The second is bringing the source of material closer to the consumer. Much like mobile plant the market is yet to present a viable alternative to diesel powered transport (trucks) and as such the longer distance that the material is required to be carted the higher the emissions. In Victoria nimbyism along with government policy has seen a reduction in new quarry permit approvals meaning that as existing quarries are exhausted any new sources of material will be pushed to more remote locations and the remaining operations forced to deliver material to a wider geographic footprint. A truck and trailer carting crushed rock will emit roughly 12kg of carbon per ton of rock for every 100km it is carted.
Building efficiency is nothing new to our industry the challenge exists in the distribution of these materials and the availability of viable inputs and find these solutions in a way that does not materially increase the production price of our material and place even more upward pressure on the cost of building and construction projects and further decrease project feasibility. The fear around most changes in our industry is always how much it is going to cost and who is going to pay for it. Current evidence would suggest that the end consumer is no longer in a position to accept increasing construction prices, so the solutions need to be
collaborative and unique.
The answer to decarbonisations is in every element of the supply chain and operators will need to update and modernize their operations as they have over generations, however it will mean little for the end outcome if contributions does not come from all levels.
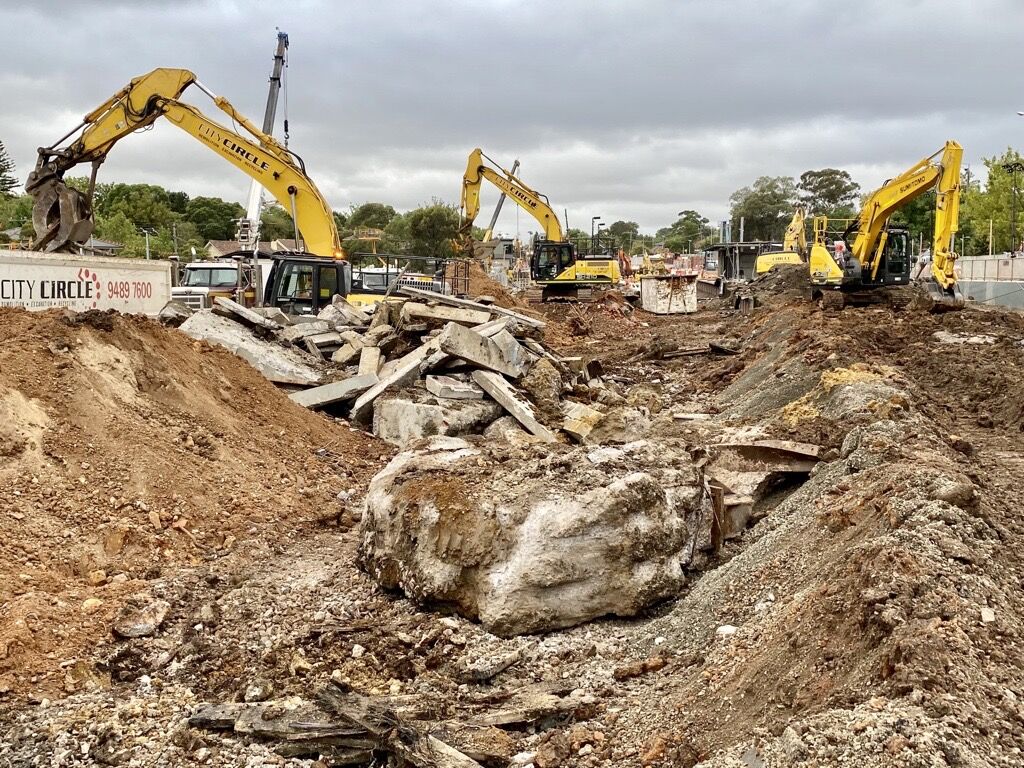
You must be logged in to post a comment Login