Safely Lifting Jaw Liners
Safely Lifting Jaw Liners Two quarries recently trialed alternative lifting methods for jaw faces without welding. Following are reports from, BRIAN CALOVIC from Conundrum Holdings, LEW DILKES from Crushing Equipment, ROSS OUTEN and ANDREW BROCKMAN of Boral.
ON Thursday, January 22, 2009 at Boral Wollert sixteen site managers, specialist welders and associated consumable suppliers attended a meeting to discuss the current practices of welding lifting lugs to manganese jaw liners in detail and to explore possible ways forward,.
Those present had a wide range of skills in foundry works, welding, installing and utilising the wear parts. Between them, there was over three hundred years experience!
Initial meetings concentrated on:
- The review of existing welder qualifications and welding procedures to ensure the best outcome was achieved with the current practice using weld on lifting lugs.
- A review of existing cast-on lifting lug arrangements
- Explore new lifting arrangements that will meet all today legislative requirements and company expectations.
The industry recognises changing out jaw faces as being one of the highest risk tasks and the issues relating to lugs breaking off and slings falling off open cast-on hooks are well documented. The committee quickly directed their attention to new approaches that will eliminate the known hazards.
The result was a CMPA report on reducing the risk of welding lifting lugs and a trial to be commenced with an alternative lifting arrangement which removed the process of welding lugs altogether. Following is a report from two companies and their suppliers on trials conducted to date.
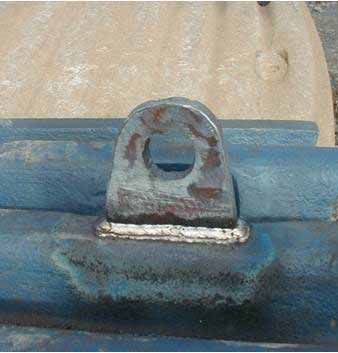
TRIAL 1
Conundrum Holdings Pty Ltd
(Stawell Quarry)–
Self-locking lifting device
BRIAN CALOVIC reports on the trial carried out at the Stawell Quarry site.
The current method for removal and installation has been to weld lugs to the jaw liners. This process can only be performed by qualified welders. Australian Standards AS 1554 part 1 SP provides a strict set of standards that welders must comply with to be considered sufficiently trained for the purposes of welding to manganese.
Industry is faced with the challenge of inconsistent manganese supply and casting quality. Issues such as unexpected elements being present within the metal are causing concerns for both the construction material business, the welders and the suppliers.
A ‘Material Certificate’ is an essential tool in assessing a wear part according to Quantec Solutions. It will identify the elements within the wear parts, and with an understanding of the envelope, can assist in identifying differences.
Physical casting faults such as air pockets, laminated metals and incorrect casts can oft en be hard to assess as the faults are often within the casting surface. This can also cause failure of lifting lugs even with the correct welding methods used.
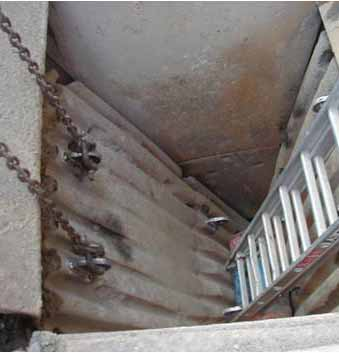
Working together with Crushing Equipment we began our trial November 2009 by fitting a set of jaw liners to our primary crusher with two holes cast to suit the trial lifting devices supplied by Crushing Equipment.
The cast holes are slotted so the lifting device could be easily fitted by inserting it into the slot and turning it 90 degrees. The two lifting devices are locked together using a pinned cross bar. Once in place the chains are attached and the liner can be lifted into place.
The jaw liner was then secured in place with the liner holding bolts fitted. The removal of the lifting device was then to release the chains, unpin and remove the cross bar, rotate the device 90 degrees and remove.
The advantage of this device was not having any welding required through the procedure. Risks associated with welding lugs to manganese include:
- Metal composition and quality of casting
- Type and size of welding rod
- Welding method
- Reliance on welder having appropriate skills and experience
- Location of lugs and testing welds
Other advantages are:
- A simple method of lifting the liner
- Less time with no welding of lugs required
- Crane time on site is greatly reduced again reducing costs.
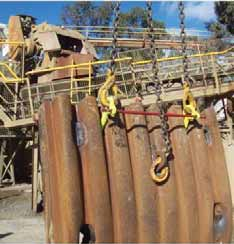
Removal of the liners was basically the reverse procedure of fitting them. We had used expander-foam in the holes during assembly to try to keep dirt out of the tool recess. This proved to work well as they did stay reasonably clean and we had no problems scraping them out and refitting the tool for removal.
As a safety measure for the trial, we welded a lug to the liner using a third chain just in case of tool failure. We found the lifting device easy to use and had up to 4 tonnes of lift on the crane to break out the upper jaw liner. This has proven a successful trial that has removed the need for us to weld lugs to jaw liners and therefore along with risk assessments and safety analysis it has reduced the risk of the task.
We would like to acknowledge efforts made by Crushing Equipment, Trevor Box and Lew Dilkes in their efforts to develop a safer method. We are continuing to work together to further improve the design.
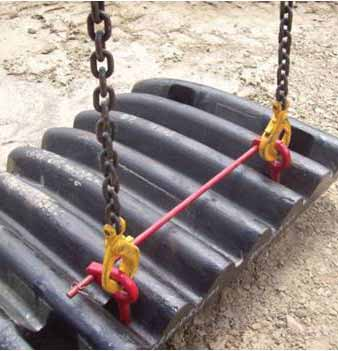
TRIAL 2
Boral Montrose –
Bolt on lift ing tabs with lifting rings
ANDREW BROCKMAN, a Maintenance Fitter at Boral, reports on the trial conducted on their site.
I have been involved in quarry maintenance for over 20 years. I am qualified as a boiler maker/welder and am responsible for the welding of lifting lugs onto manganese liners at our Boral Quarries in Melbourne.
Over the years, we have refined the method for making lugs and attaching them to manganese with the use of design engineered lugs and very strict welding procedures.
Despite this, we have never been able to make the task entirely safe. Varying metallurgical composition of the steel is a major concern. I have seen lugs torn out of the parent steel as a result and have also come across some very dubious casting with hollows below the surface of the steel which only become evident when you start welding.
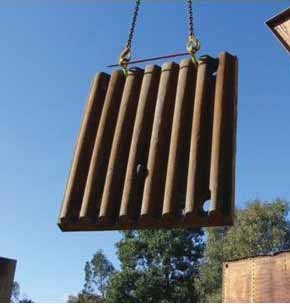
Fortunately we have never had a major incident, but I have certainly heard of numerous cases of people in our industry being seriously injured as a result of lifting lug failures.
When the idea of developing lifting equipment for liners was suggested we jumped at the opportunity to be involved. We approached our trials differently, utilising Our Man Flynn.
Thank you to Mike Flynn and his team who helped to incorporate a lifting method which did not rely on welding.
Early this year, we installed our first set of liners into the 60” x 48” jaw crusher at Montrose Quarry. The trial was very successful and our team was very relieved to finally have a far safer means of carrying out this task.
I hope that this is adopted across all quarries and for all machines – the sooner the better!
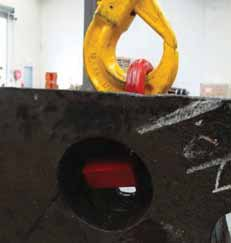
DEVELOPMENT OF THE FINAL JAW LINER LIFTING TOOL
LEW DILKES from Crushing Equipment also reported on their trial, particularly from the supplier’s viewpoint.
The jaw liner lifting tool was presented to the CMPA Committee as an alternative and the members from Crushing Equipment Pty Ltd accepted the opportunity to explore the challenge.
A project (project number CE011) was established and developmental work began early 2009.
The team included Lew Dilkes and Trevor Box of Crushing Equipment Pty Ltd to design and manufacture the initial prototype tool and Brian Calovic and his team at Conundrum Holdings Stawell Quarry who carried out all the onsite testing.
Brian and his team provided valuable feedback for the development of the tool through to the final stages. Further assistance was provided by the Scaw Foundry Group with the manufacture of modified crusher Jaw liners along with Crushing Equipment Pty Ltd sister company PWB Anchor Limited and Townley Drop Forge Pty Ltd who played their role with the manufacture and certification of the final forged components.
The Jaw Liner Lifting Tool will besupplied with Test Certificate traceable to the forging manufacturer and material supplier along with a specification document. A specification sheet is supplied with the Tool.
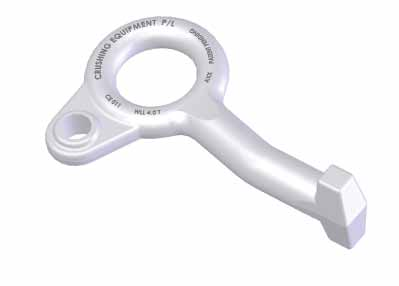
At the end user’s request the Jaw Liner Lifting Tool can be returned for inspection and include:
- Visual and dimensional inspection to determine any distortion
- Crack test inspection
- Proof load test
- Test certificate
All testing has been completed and a final report will be presented to the CMPA committee shortly.
Benefits of the Jaw Liner Lifting Tool CE011 include:
- Elimination of the requirement for welding on lifting lugs.
- Eliminate the hazards associated with welding on lifting lugs.
- The forged lifting components of the Jaw Liner Lifting Tool are load certified to AS3776-2006 and the WLL is included in individual identification.
- No threads
- The stabiliser bar once attached to the tool will not allow the Jaw Liner Lifting Tool to separate from the jaw liner in the event the lifting chains or sling becoming slack.
- The Jaw Liner Lifting Tool can be attached without removing or loosening bolts retaining the jaw liner.
- Jaw liners can be reversed without additional lifting attachments.
- Minimal aid required to position the jaw liner against the jaw face.
The cast holes and Jaw Liner Lifting Tool is designed this way for the following reasons:
- Easy to use
- Easy to manufacture, test and maintain
- There are no threads or hidden areas difficult to test
- One design suitable for all common jaw liners regardless of tooth profile and size up to the load limit.
- Lift holes are easy to produce at the Foundry and no machining required
- Holes positioned to allow new or worn liners to be lifted from any position
- Holes positioned on the fitting face can be filled with foam for easy cleaning for liner removal
- Holes positioned in the wear face for lifting at correct angle for installation and removal
- Holes positioned in the end for a vertical lift as required
- Holes positioned to ensure crane support is maintained while retaining bolts or wedges fitted.
- Holes do not interfere with the crushing operation
- Holes can be easily plugged (metal plug) if required
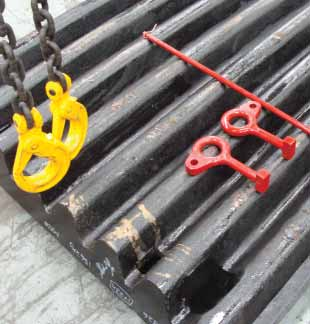
Crushing Equipment Pty Ltd welcomes the opportunity to work with the CMPA and its members on safety improvements and production cost saving initiatives that can be made. The jaw liner lifting tool development was a rewarding project. The experience within the Australian team along with the support from the Scaw Metals Foundry team members and the resources they have to offer are available for ongoing projects.
Further details are available from Lew Dilkes of Crushing Equipment Pty Ltd by phoning 03 9338 0200 for those who would like additional information on the Jaw Liner Lifting Tool CE011.
You must be logged in to post a comment Login