WORKING AT HEIGHTS
John Mitas, Operations Manger, DPI
Following is the transcript of the presentation on ‘Working at Heights,’ as delivered by John Mitas, Operations Manager DPI, at the 15th CMPA General Meeting, continued from Issue 19.
…The idea is to stop the incident happening. Stop the rollovers, that’s the priority. However, you need to have controls in place that will limit the damage to the person if an incident does occur.
One of those controls is seat belts, another is rollover protection cabins (ROPS cabin). You could spend $15,000 and put a ROPS cabin in, but it’s useless if you don’t wear your seat belt. For the ROPS cabin to work, you have to stay in the capsule, that’s the idea of it.
Firstly you need to look at your controls for stopping an incident from happening, secondly you need to get your drivers to wear their seat belts. How often do you stop your drivers and check if they are wearing their seat belts?
Question: Is there a rule regarding the replacement of seat belts, or can you look at the seat belt and think its okay?
Answer: Seat belts are like every other bit of equipment. You need to maintain them. Part of the maintenance of your truck should include looking at the seat belts to determine whether it’s functional. It has to be put on your maintenance schedule. I don’t know what the appropriate period to do that would be. If you look at your trucks and the seat belts have got a tonne of dust on them and therefore haven’t been used, you know that there is something wrong. It is your responsibility as an owner to have functional seat belts for your drivers. It is your responsibility to teach them to wear it. It is your responsibility to take some action if they are not.
Question: Is there a company that tests them for you?
Answer: I would say the manufacturer. I would suggest that Caterpillar for example should have some a tick in their maintenance for such issues.
William Adams Spokesperson: Our policy is replacement every three years. You need to at least follow the manufacturer’s guidelines. I would suggest that it is money well spent. As an industry we don’t supervise and physically check that these types of things are being done. You need to tell your people to wear seat belts, then you need to check them. Pull up some one and check that they are wearing their seat belt. If not take some sort of action. We need to reinforce that sort of culture.
Stockpile tipping – You don’t tip over faces unless you are 100% certain that no one is going to go over. A lot of people, usually drivers, when reversing to a place to tip actually guess where the edge is. They can’t tell, they are about 20 metres away from the edge looking through a glass. It’s a bit of a hit and miss to know where the edge is.
You need to have windrows in all your stock piles Make sure that if they make a mistake that there is a windrow there to stop them from going over. You should be tipping back from the face and pushing over with a dozer or loader. That is common industry practice that should be widely adopted.
There is no logic in allowing your drivers to rollover your million dollar trucks. You are losing a lot of money in terms of equipment, and you are also putting your drivers in a situation where they can be killed. We’ve had a couple of fatalities in South Australia in which a truck was going down the ramp, went over the windrow, dropped down 30 metres, and the operator was killed. This a serious issue.
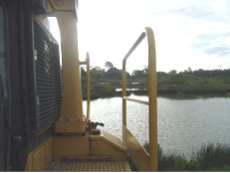
This is a dozer that the operator was trying to fuel. He had the hose and was trying to get to the fuel tank. It was wet and slippery and he fell off and injured himself. If you have loaders that are more than two metres off the ground, it becomes an issue of working at heights.
We’ve had people in Victoria fall off a 992 trying to clean the front windscreen and nearly break their shoulders and almost killed themselves. People can die from this height, especially if they fall the wrong way. It is a serious issue in terms of equipment. I think you should put on the list I mentioned before, all of your front end loaders and dozers, and have a look at the controls that you have got in place.
Ladders as we said are not very effective, you can’t do much with a ladder. You can only use half your arm, you can’t extend too much, you need to have good access to stop people from falling off. This is an issue that we have talked about before. If you have to spend a million dollars to buy a piece of equipment, I suggest you demand that when it hits your yard it’s got all the safety gear.
Question: On the issue where you have a fuel tank that is up high, there should be a design put in place for fueling to take place.
Answer: It’s a good point, you need to find the best control. If you can do it from the ground, that’s better, if you can’t another way is to have a platform so that people can drive their machines there and have a solid platform under them.
Question: On the heights issue, what am I to do if I need to drill on the front row of a 10 metre bench?
Answer: You need to put it on your list as a hazard. You and your team need to do a risk assessment on the hazards and risks to come up with the controls that I mentioned, and choose which of those controls is the most effective. There are a number of options. Ron Kerr had in place some ‘temporary’ controls when we had the Drilling Workshop. Another option is to put a windrow in.
With stone, its not going to contaminate your shot. You build a windrow and then you drill behind it. Another possibility would be to drill remotely. In the front row you drill where the operator doesn’t have to get close to the hole, etc.
As an organisation you need to get together and combine your experience so that you can come out with some practical controls that suit the industry.
Question: I recently received an email on a drilling fatality. Could you please elaborate on that.
Answer: All we know is what’s in the email. We have an agreement with the OH&S inspectors that if there is a fatality they circulate it. The way I read it, a drill was drilling on a bench and the whole bench just collapsed. The drill and driller went down with it and the driller died. I don’t know the circumstances of the geology, I don’t whether he was on a slip plane, I don’t know how wide the bench was, that will all come later. When it does we will circulate it around.
A couple of things about Minerals and Petroleum, we are restructuring the
operational group. We advertised the new positions not so long ago and I was selected as the Operations Manager for Victoria. There is going to be five District Managers who will report to me and we are advertising those positions internally.
Graeme McLaughlin who was previously in Bendigo will go to Ballarat. The other four have been advertised and as soon as we fill those positions we will let you know. Basically you will have a Manager for each district, an Environmental Officer, and the Regulation Officer who will report to the Manager. It will hopefully provide a bit more consistency across Victoria.
The other issue is that we have to make slight revisions to the map that we have for your regions. We’re basically going to try to match the boundaries of the Department of Sustainability and Environment because we consult with them quite regularly. Copies of the map will be made available as soon as we finalise it.
Question: issues with audits…
Answer: Part of our job is to assess you and your compliance with regulations, and to provide you with guidance notes and guidance materials etc. Today is part of that package and we are happy to do that as part of the job.
At the moment we have John Young, an ex WorkCover inspector and ex EPA inspector. He is not an inspector under our Act and doesn’t have inspector powers. All he is doing is going through some of the sites that we haven’t been through for a while. The idea is that he will come in, audit your site, give you some assistance in terms of how the system should be working, if there is some serious issues about certain things then we will have to come back and look at those things as well, maybe we will then follow that up.
The idea is to give you an idea of how your system should be working, to give you some tips and help on some of the key issues.
Comment: John Young was very cooperative and we talked about a variety of issues. However, I think we already had most of the systems in place through those that the CMPA had generated. He was quite impressed with the systems as a person from outside the industry.
He’s going to be in South West Ballarat for the next 2 – 3 weeks, then we’ll consider sending him around to some other districts that haven’t been visited for a while.
William Adams Spokesperson: We have a new seat that is retro-fittable to
all older CAT trucks, and as you can see the seat belt has got a red band so
you can identify if the operator is wearing it or not. This is a new item so I thought I’d point that out for you. It’s like a toggle link type suspension seat, it’s very different, it’s the same as what’s in the G series machines.
Grant Phillips, Chairperson: On behalf of the CMPA I would like to wish John all the very best in his new position, congratulations, and we certainly appreciate all his support and look forward to that ongoing.
You must be logged in to post a comment Login