Alex Fraser Group
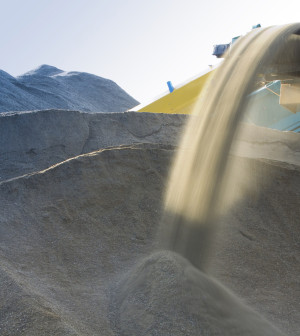
Alex Fraser Group – A new era in recycling glass fines
Victorian Recycling Production Manager Adam Somerscales shares how Alex Fraser Group is taking its glass recycling one step further by building an improved processing plant at our Laverton facility.
For nearly ten years we have been working to return recycled glass to its primary state of sand. Glass from kerb side collection is broken down and optically sorted into different colours. It is then sold to glass bottle manufacturers, who have strict quality guidelines for recycled glass.
When pieces of glass are too small to sort or contain large amounts of Ceramic, Stone and Porcelain (CSP) this glass is stockpiled. Alex Fraser takes these problem glass fines and processes them to sand for use in drainage and road projects.
A pilot plant has been used to prove the process and help develop a market over the last six years. In the past 12 months, we have been looking at ways in which we can more effectively separate the glass from metal, sharps and plastics, and increase processing efficiency.
One way is through screening technology. The process we use for crushing glass is quite similar to how we crush rock, concrete and brick, however the screens used are more suited to aggregate products than glass. Currently, the steel screens ‘blind over’ if the glass is wet, which means glass will fill in the holes in the 5mm screen where material should fall through. Our new plant will feature screens that vibrate faster and self-clean.
A lot of research has been done on magnetic separation of fine metal objects. We discovered a way to enhance the magnetic properties of tiny metallic pieces, and separate them off mechanically.
This new plant design increases our production capability from the 50 or 60 tonnes per hour, to 100 tonnes per hour. Through a long running series of laboratory tests and field trials, we have also demonstrated that we can increase the amount of recycled sand in road base while maintaining the specifications set by VicRoads and have precise mix registrations in place.
The key differentiator for Alex Fraser is our customers trust that we can make a consistent road base, asphalt or sand for their projects, all day every day. By researching different plants used overseas and local scoping and testing over the past 12 months, we now have been able to design a fixed plant at our Laverton facility. The plant will include crushing processes and multiple screening and separation processes.
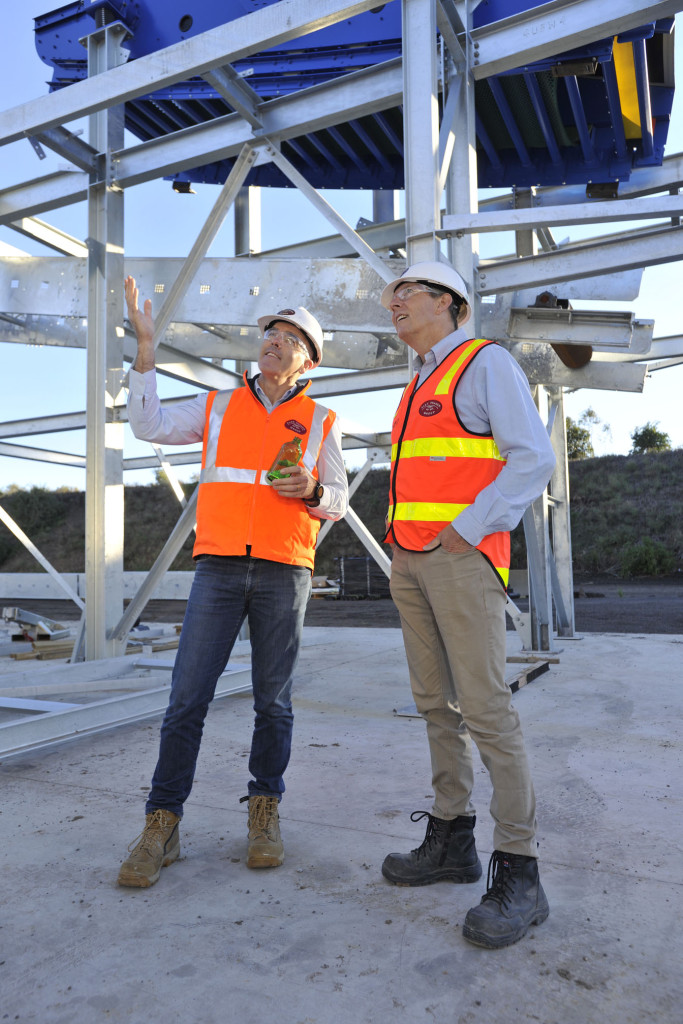
Alex Fraser MD Peter Murphy inspects the work at the company’s new glass recycling plant with Hanson CEO Phil Schacht
Conveyors will link it into our main crushing plant. This will substantially reduce mobile equipment movement and material handling costs, it will also maintain precise control of mix designs, and maximise the use of recycled sand in all our products.
This is an intricate project that we haven’t seen anywhere in the world, and there will be lessons to be learnt during commissioning and operation. The design process has included input from operators, maintenance personnel, consulting engineers and safety advisors.
We are aiming for an efficient plant that has excellent maintenance access, and makes a good product in high tonnages. Having finalised the design, we’re starting earth works, engaging electrical contractors to run power around the plant and starting work on fabricating the conveyors. The critical piece in our timeline is the screens and crushers that are being manufactured overseas.
The aim is to have the new plant up and running in the first half of 2018. It’s a challenging but achievable timeline. It will be the first glass recycling facility licensed under Victoria’s new regulations. There is potential to build more of these plants in the future, however in the short term this one plant will produce enough to supply to the Laverton, Epping and Clayton plants.
You must be logged in to post a comment Login